Zircon (ZrSiO4) belongs to the tetragonal system. The theoretical composition is 67.2% of Zr02 and 32.8% of SiO2, which is the only compound in the binary system of Zr02-Si02. 65% Zircon Brick. The thermal expansion coefficient is small, the load softening temperature is high, the thermal shock stability is good, and the thermal conductivity decreases with increasing temperature. Therefore, As the refractory materials manufacturer said, the zircon refractory brick is an indispensable material for industrial kilns such as building materials, light industry, electronics, metallurgy, and so on.
In recent years, with the advancement of glass industry technology and the application and promotion of kiln insulation technology, the amount of machined 65% Zircon Brick has been increasing. Mainly used in the gap, upper partition wall, fire observation hole, temperature measurement hole, and other parts of the glass kiln. The temperature of this part is high and it is eroded by flying materials and eroded by hot airflow, so the environment is very engraved.
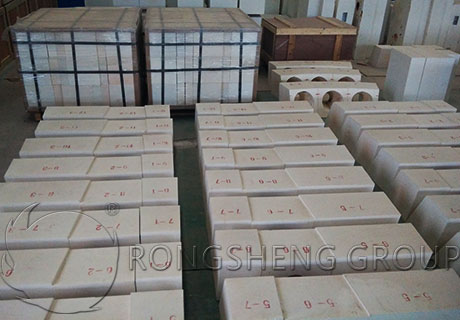
Preparation of 65% Zircon Brick
To produce zircon bricks with a Zr2O3 content greater than 65%, the content of the raw material Zr2O3 used must be greater than 66%. The decomposition temperature of the zircon is 1676℃. As the content of impurities increases, the decomposition temperature decreases. The high purity of the raw materials is the primary condition for the production of zircon refractory bricks with 65% zirconium with excellent properties.
The raw material of zircon is granulated and cannot be directly used for making bricks, but must be ground into a fine powder. Because zirconite has a large wearability index, the fine powder is obtained by vibrating mill and air-jet mill.
Due to the use of 65% zircon brick containing ZrO2. The material should have good high-temperature physical properties, and the aggregate is closely related to it. The zircon sand is ground first, then made into a green body, which is crushed into different particle sizes after high-temperature calcination. Because the zircon material is brittle, the broken particles are in the form of flakes. The normal temperature compressive strength of sheet materials is about 50% higher than that of granular materials. On the contrary, under the same conditions, the bulk density of granular granules is 0.12g/cm³ higher than that of flakes on average. Taking into account the compressive strength and density performance, the crushed material must be properly treated before it can be used.
The batch materials are mixed on a wheel mill mixer, and the materials are trapped for 16 hours, and then formed on a large-tonnage friction brick press. The forming pressure is 700~1000Kg/cm³. Applying large pressure can cause the average distance between adjacent particles to decrease and the contact area to increase, which is beneficial to sintering. But after increasing to a certain level, the effect is extremely insignificant. Appropriate pressure and pressurization methods are the keys to solving the formation of barren materials.
The sintering of zircon is more difficult, and its speed is slow due to solid-phase diffusion at high temperatures. Adding MgO, CaO, Y2O3, TiO2, ZnO2 can reduce the sintering temperature and promote its sintering. In this sintering, 1.5% to 2.75% of Y2O3 and TiO2 were added as sintering accelerator, sintered in a shuttle kiln, and the firing temperature was 1580 to 1650℃.
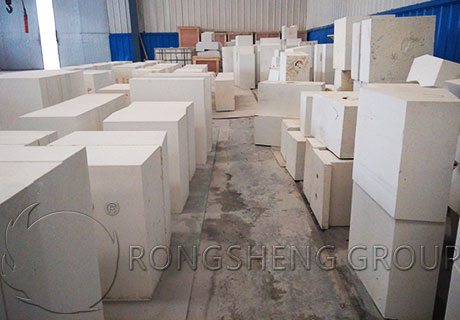
Use Performance of Zircon Brick in Steel Ladle
The use performance of zircon bricks in steel Ladles is also called zircon bricks in steel Ladles. It is made of zircon as the main raw material and participates in the combination of a certain amount of fused alumina, high-silica content of clay soil, clay, and chromium oxide. This kind of steel barrel lining bricks has been developed abroad for a long time. In order to improve the uneven erosion of semi-silicon brick steel lining bricks, it gradually expanded from strengthening local lining to all lining bricks. As a result, the service life of large steel Ladles is increased by 2 to 3 times. In order to meet the use of the first phase of Baosteel in China, this brick has been developed and used.
The defects of zircon bricks are slag, steel, and spalling. The main reason is that it is not easy to reduce the porosity due to the zircon brick, and it is affected by the infiltration and the glass property generated in the matrix part. The advantage is that the service life can reach more than 100 times, which is conducive to the turnover of the steel drum. The high cost of this kind of brick is also limited by the source of domestic raw materials, which restricts its development.