For a long time, high silica bricks have been used for tundish refractory. Today, low-cement and high alumina castables have widely replaced high-silica bricks by increasing life to reduce costs and improve working conditions. Because MgO coating must be applied to the tundish permanent castable. For high aluminum castables, volume stability is very important.
Although high-alumina refractory castables have higher mechanical strength and better corrosion resistance, cracks occur due to insufficient volume stability. Metal attachments penetrate through the cracks, resulting in a reduction in their life and an increase in local maintenance.
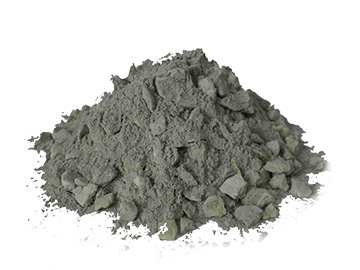
Performance of Light-weight High Alumina Castable
High-performance light-weight high-aluminum castable improves its strength and reduces thermal conductivity. The castable has better construction performance and higher medium-high temperature strength. The compound combination method of hydration combination and coagulation combination can improve the normal temperature and high-temperature performance of the castable. The developed high-performance light-weight high-aluminum castable has low thermal conductivity, high high-temperature strength and volume stability. It is used in high-temperature parts of various industrial furnaces from 1200 to 1500 ℃ and has achieved good results. The energy-saving effect is obvious.
Experiments have shown that:
(1) The method of adding ultra-fine alumina powder can improve the construction performance of high-aluminum castables. However, as the ultrafine alumina content increases, the volume stability after firing decreases.
(2) If mullite is added to the matrix instead of alumina, the volume change after firing will decrease, but the construction performance will also decrease with the increase of mullite content.
(3) When andalusite is added to the matrix, the construction performance is reduced a lot, but the volume stability is greatly improved. Therefore, if the plasticity of andalusite is improved, andalusite is a good material of choice for the matrix of high-alumina castables that require high volume stability.
The high-performance light-weight high alumina castables are fully considered, and various related factors that affect the castables are fully considered. In the case of reducing production costs and meeting the conditions for the use of castables, optimize the composition and configuration of castables, formulate a reasonable production process, and strengthen process control. Castable manufacturers have produced a series of high-performance light-weight high-aluminum castables with a bulk density of 1.30 g/cm3, 1.50 g/cm3, and 1.80 g/cm3 to meet various working conditions.
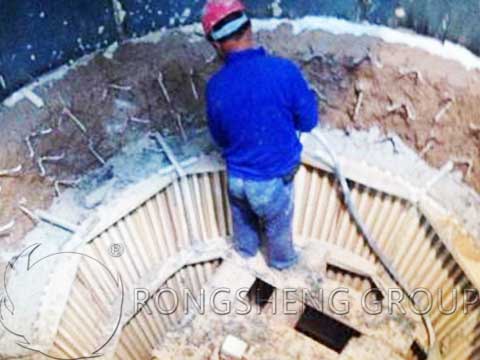
Application of Lightweight High Alumina Castable
The performance of lightweight high-aluminum castables determines the energy-saving effect of thermal kilns. With the rapid development of various industries, the number and scope of light-weight castable applications are gradually expanding. From the permanent layer, the heat insulation layer to the working layer, from the low-temperature part to the high-temperature part, the transition from low load environment to high load environment. insulating castable. At present, the technology of lightweight high-alumina castables used in the working layer in the middle and low temperature (<1 200 ℃) and high temperature (>1 500 ℃) parts has basically matured performance. However, the performance of lightweight castables used in the medium and high-temperature range (1 200 to 1 500 ℃) needs to be improved to meet the new requirements for the use of lightweight high aluminum castables.
Rongsheng Refractory Castable Manufacturer
Rongsheng refractory castable manufacturer has a fully automatic refractory castable production line. The high-performance light-weight high alumina castables produced by Rongsheng are characterized by high strength, low thermal conductivity, and excellent construction performance in the working environment above 1200 ℃. And it has great significance in the research and application of energy-saving technology, energy-saving equipment, and energy-saving materials.