Magnesia-chrome bricks are the most commonly used refractory bricks in copper smelting thermal kilns. Configuration of magnesia-chromium bricks for copper smelting thermal kilns. In common copper smelting thermal kilns such as top-blown converters, horizontal converters, anode furnaces, flash furnaces, electric furnaces, Kifset furnaces, Ausmet furnaces, reverberatory furnaces, oxygen-rich bottom-blown furnaces, etc. Magnesia chrome bricks are the main configuration.
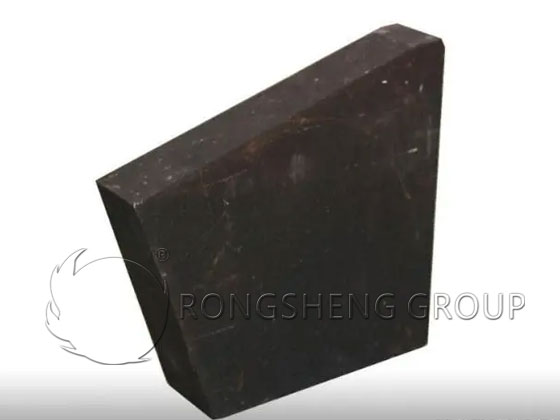
As the name suggests, magnesia-chrome bricks are made of sintered magnesia and chromium sand according to certain proportion requirements and are shaped and sintered by adding additives. According to their chemical properties, magnesia-chromium bricks are alkaline refractory bricks. It is most widely used in non-ferrous metals, especially copper smelting. Secondly, it is also widely used in cement production.
Magnesia chrome bricks can be roughly divided into six different types according to their production methods. 1) Silicate bonded magnesia chromium brick. 2) Directly combine magnesia chrome bricks. 3) Electrofusion rebonded magnesia chromium brick. 4) Semi-rebonded magnesia-chrome bricks. 5) Fused magnesia chrome bricks. 6) Chemically bonded unburned magnesia chromium bricks. Among them, among the thermal kilns for copper smelting, the most widely used ones are directly bonded magnesia chromium bricks, semi-rebonded magnesia chromium bricks and electrofused rebonded magnesia chromium bricks.
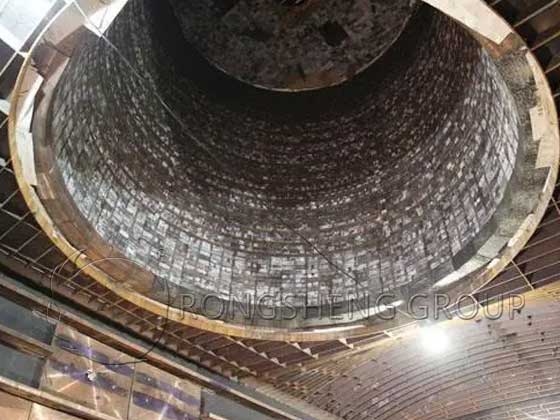
Directly bonded magnesia chrome bricks
Directly bonded magnesia-chromium bricks have high-temperature strength, slag resistance, erosion resistance, erosion resistance, corrosion resistance, excellent thermal shock stability and volume stability at 1800°C. Directly combined with the main application parts of magnesia-chromium bricks, the bottom of the top-blown converter, the non-working layer of the furnace wall, and around the horizontal converter barrel. Around the cylinder of the anode furnace, there are the walls of the Kifset furnace, the walls of the Ausmet furnace, the top and walls of the reverberatory furnace, and the upper part of the oxygen-rich bottom-blown slag line.
Electrofusion rebonded magnesia chromium brick
Electric fused rebonded magnesia chromium bricks are made by melting the raw materials using the electric fusion method to make fused magnesia chromium materials, crushing them into a certain particle size, and then mixing, shaping, and sintering them. Combined with the magnesia-chromium brick, it is a fine-grained matrix with evenly distributed pores and micro cracks, and is more sensitive to sudden temperature changes than melting and casting. The high-temperature performance of electrofusion rebonded magnesia chromium bricks is between that of fused cast bricks and directly bonded bricks. The main application part of electrofusion rebonded magnesia-chromium bricks is the working layer of the top-blown converter furnace, which is in direct contact with the copper liquid. Horizontal converter furnace mouth. The mouth of the anode furnace. Flash furnace reaction tower. Electric stove mouth. Kifset furnace bottom working layer. Ausmet furnace furnace wall and furnace bottom. The lower part of the oxygen-rich bottom-blown slag line and the wind eye area.
Semi-rebonded magnesia chrome bricks
Semi-rebonded magnesia-chromium brick refers to a kiln refractory product fired from part of the fused magnesia-chromium sand as raw material. The main mineral composition of semi-rebonded magnesia-chromium bricks is periclase, spinel, and a small amount of silicate. Its thermal shock resistance is better than that of directly bonded magnesia-chromium bricks. The main application parts of semi-rebonded magnesia-chromium bricks are the walls of flash furnace sedimentation tanks. Electric furnace hearth. Ausmet stove. The working layer is at the bottom of the reverberatory furnace and the copper outlet.
In actual applications, reasonable magnesia-chromium brick configuration should be carried out according to the kiln structure and working environment. In addition to the above-mentioned magnesia-chromium bricks, magnesia-chromium unshaped refractory materials such as magnesia-chromium ramming materials, magnesia fillers, and magnesia-chromium castables are also used in copper metallurgical thermal kilns.
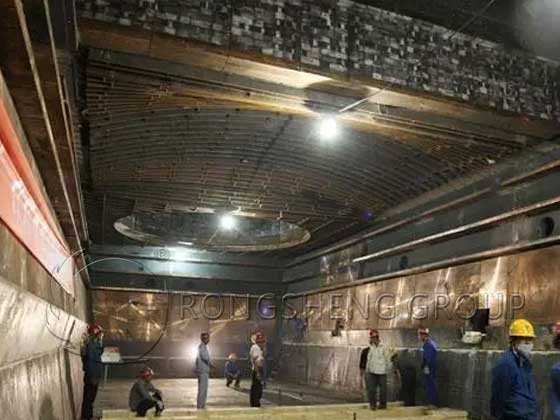
Application advantages of magnesia chrome bricks in copper smelting furnaces
In the development history of magnesia-chromium refractory materials used in the copper smelting industry, silica bricks were first used to build furnace linings. However, since the slag composition contains FeO and SiO2, and the smelting atmosphere contains a lot of SO2 acidic gas, the erosion damage of the silica bricks is very serious. From the 1950s to the 1960s, alkaline bricks have been used in the copper smelting industry. Today, after several generations of continuous improvement, the production process of magnesia-chromium refractory materials and its application in the copper smelting industry is becoming more and more mature.
Currently, direct-bonded magnesia-chromium bricks are widely used in converters. The technology of directly bonding magnesia-chromium bricks to build the furnace body, and using electric fusion and then bonding magnesia-chromium bricks to build the tuyere, furnace mouth, and other positions to build the converter lining has been applied.
Taking the lining construction of a 150t copper converter in a certain factory as an example, ordinary silicate-bonded magnesia-chromium bricks are used to build the cylinder and end wall linings. Directly bonded magnesia-chromium bricks with high chromium content have been used in locations such as tuyere slag lines that are severely corroded, and good results have been achieved.
A copper factory also achieved good results by using improved electric fusion combined with magnesia-chromium bricks to build tuyere, extending the furnace life and reducing the period of minor repairs.
Generally speaking, ordinary magnesia-chromium bricks are currently used to build furnace linings. The general method of constructing the copper converter lining is to use directly bonded bricks or electro-fused rebonded magnesia-chromium bricks to build the tuyere, slag line, furnace mouth, and other locations.