Fireclay refractory bricks refer to fireclay products with Al2O3 content of 30%-40% alumina silicate. The refractory temperature is 1690~1730℃. It has good thermal stability, and the number of times of water quenching and heating is 10-25 times, and it increases with the increase of clinker and coarse particle content. Refractory clay bricks are weakly acidic refractory materials, which can resist the erosion of acidic slag, but their resistance to alkaline slag is slightly weaker. Among all refractory materials, refractory clay bricks have the widest application range. For example, the protective bodies of various heating furnaces, heat treatment furnaces, cupolas, and drying furnaces are mostly built with refractory clay bricks. In addition, fireclay refractory bricks can also be used to build steel drum linings.
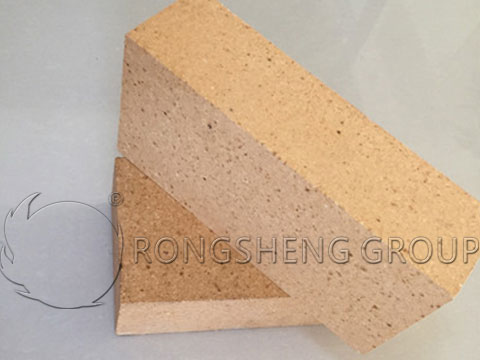
Refractoriness of Lightweight Fireclay Refractory Bricks
Lightweight fireclay bricks are lightweight refractory products with a porous structure with an AL2O3 content of 30%-46%, which are shaped refractories. Mainly use plastic mortar burnout additives or mortar foam method or chemically made porous products. The product has a wide range of uses and can be used for the thermal insulation layer of various high-temperature furnaces.
The specifications and sizes of lightweight fireclay bricks are divided into standard and special shapes. Standard specifications are available at Rongsheng refractory brick manufacturers, and special-shaped specifications and sizes can be customized according to drawings. Lightweight fireclay bricks are characterized by high porosity, uniform pore distribution, low volume density, good stability, and excellent thermal insulation properties.
Indicator of light fireclay bricks. The bulk density of commonly used lightweight fireclay bricks is 0.75-1.2g/cm3. The smaller the bulk density, the better the thermal insulation, and the lower the use temperature. The compressive strength is 0.98-5.88MPa, and the abrasion resistance is poor. It should be handled with care when handling or building. The thermal conductivity at 300°C is 0.795-2.93W/(m.k). The operating temperature is generally 900-1250°C, and the maximum operating temperature is 1200-1400°C.
The use temperature of light fireclay bricks of different bulk density has certain differences, and the price is also different. Therefore, the choice of light clay bricks depends on the operating temperature of the kiln and is based on the economy and practicality.
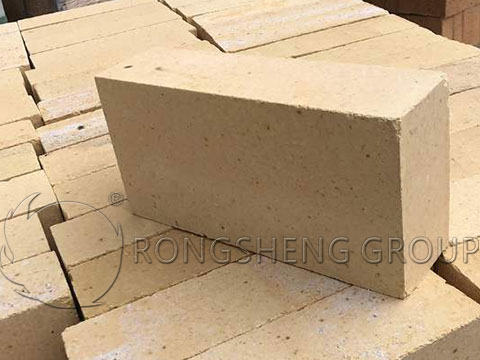
Masonry of Clay Refractory Bricks
Before choosing fireclay refractory bricks to build the furnace, the factory can calculate the approximate quantity needed to purchase in the furnace building plan. It can reduce unnecessary waste, and pay attention to the use of first-grade mortar joint masonry for masonry mortar joint.
When building clay bricks, it is feasible to prepare clay refractory mortar by yourself, clinker: raw material = 70%: 30%. Clinker is obtained by calcination of hard refractory clay at high temperatures. Waste bricks can also be used after being ground. The raw meal is light refractory clay.
If you want to calculate the various compositions of refractory mortar, just substitute the known weight of refractory mortar into formula (1) and formula (2).
(1) Clinker weight = refractory mortar weight x 70%
(2) Raw meal weight = refractory mortar weight x 30%
When using T-3 standard bricks (230x114x65mm) for masonry. The following figures should be memorized:
- Each refractory clay brick weighs 3.7kg.
- About 270 pieces of refractory clay bricks per ton.
- Each ton of clay bricks requires about 76kg of refractory mortar.
- It takes about 594 bricks per cubic meter of masonry.
- Approximately 2.2 tons of bricks are required for each cubic meter of masonry.
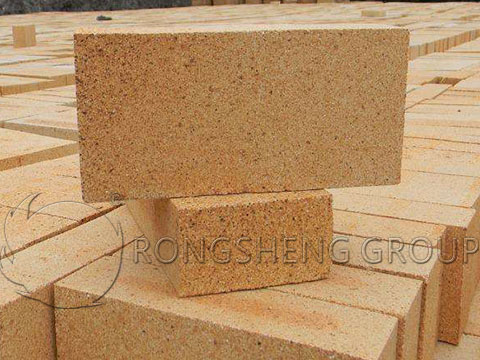
Rongsheng T-7 Fireclay Refractory Bricks Manufacturer
T-7 fireclay refractory brick, unit weight 4.1kg, alumina oxide is greater than or equal to 65. Zhengzhou Rongsheng Refractory Material Factory fire clay bricks for sale mainly produces various types of high alumina and fireclay refractory bricks, low creep high alumina bricks, high alumina balls, corundum bricks, light insulation bricks, and magnesia carbon bricks. Refractory mortar for all kinds of kiln masonry, unshaped refractories of various materials for smelting and steelmaking. Shaped refractory products and unshaped refractory materials can be produced in accordance with general standards and special requirements of users. Contribute to the longevity, high-quality, high-yield, energy-saving, and consumption reduction of high-temperature industrial furnaces!