Zircon-based and ZrO2-based refractories made from zirconium-based refractory raw materials have excellent resistance to chemical attack and high-temperature performance. For example, zircon bricks are used for the slag part of the steel drum, ZrO2 brick linings are used for the nozzle holes of the sliding nozzles, and ZrO2 quality sizing nozzles are used for horizontal continuous casting. At the same time, zirconium-based raw materials are introduced into other refractory materials, and the performance of the original materials, especially the thermal shock stability, is greatly improved by using the phase transition of ZrO2.
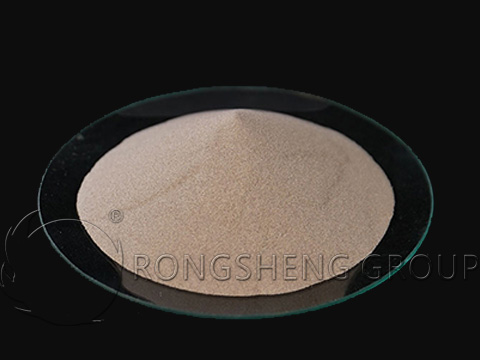
The Effect of Adding Zirconium-Based Raw Material to the the Slag Part Refractories of the Steel Drum
Adding ZrO2 substances to refractory materials has the following two functions:
①The main crystalline phase or the secondary crystalline phase is generated so that the material has special properties.
For example, the most well-known fused corundum bricks. It is a mass-produced 33# fused cast zirconium corundum brick. Its composition is near the eutectic point of the Al2O3-SiO2-ZrO2 ternary system, and its molecular formula is equivalent to 2Al2O3-SiO2-ZrO2, abbreviated as AZS fused cast brick. Its main crystal phase is the eutectoid of baddeleyite and corundum (Z+C), or baddeleyite, corundum and mullite (Z+C+M). The presence of (Z+C) eutectoid makes AZS bricks 15 times more resistant to chemical attack by glass solution than high alumina materials made by sintering. The (Z+C) eutectoid of independent components is an important structural unit to maintain the structural stability of the AZS brick body in the middle and later stages of the erosion of the glass molten pool.
In the iron and steel industry, the use of stable ZrO2 has the ability of oxygen ions to move between two phases with an oxygen potential difference, that is, the deoxidation ability and the use of stable ZrO2 bushings suppresses the precipitation of oxides. The clogging degree caused by Al2O3 deposition in the immersion nozzle for continuous casting is reduced by half.
② Modification of the original material.
High alumina and basic refractory products have good chemical stability and high-temperature performance, but poor thermal shock stability. Adding ZrO2 to corundum bricks, high alumina bricks, and magnesia bricks can significantly improve the thermal shock stability of these refractory products by using the toughening effect of ZrO2. Anti-spalling high-alumina bricks for cement kilns are made by adding zircon powder to the ingredients of high-alumina bricks. After firing, many microcracks are formed around the ZrO2 particles, so that the thermal shock stability (1100℃-water cooling) of this brick can reach more than 40 times. Good results have been achieved in the upper transition zone of the cement rotary kiln and the side wall of the grate cooler. As early as the early 1930s, some people developed magnesium-zirconium products, whose thermal shock stability and resistance to iron furnace slag and open-hearth slag are better than those of magnesia bricks. After adding ZrO2, the strength of magnesia zirconium brick is also higher than that of ordinary magnesia brick. This product is expected to be used in cement rotary kilns, which can partially replace magnesia-chrome bricks to reduce chromium pollution and protect the environment.
For free samples and quotations of refractory zircon bricks for ladle slag, please contact us.