RS refractory plastic manufacturer, how many types of refractory plastic are there? Refractory plastic is divided into different materials such as clay, high alumina, aluminum carbide silicon, silicon, magnesium, etc., and the binder includes different types of binders such as water glass and phosphoric acid. In the types actually used, phosphoric acid binder is relatively more used. However, the refractory plastic combined with phosphoric acid binder must be trapped, and the trapping time must not be less than 18-24 hours.
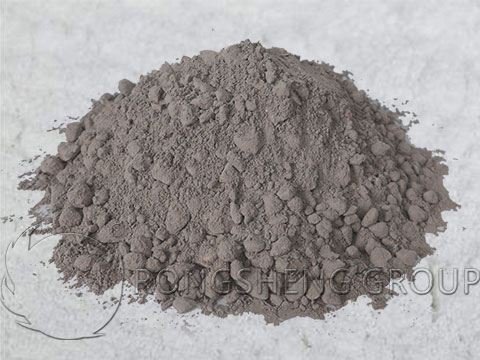
Reasons for Trapping Refractory Plastics
The reason why refractory plastics need to be trapped is that there are certain impurities in the raw materials of plastics, which react with phosphate binders. After the reaction, a large amount of gas will be formed, which will cause the internal expansion of the plastic, resulting in a loose structure of the material and a decrease in strength after hardening. The purpose of trapping is to allow the gas to be fully discharged after a period of time. After the gas is discharged or during construction, the remaining binder is added, so that the use function of the plastic can be fully utilized.
If it is a plastic combined with water glass, the binder can be added during on-site construction. At present, due to technological innovation, refractory plastics are squeezed into small cubes by an extruder before use, packaged in plastic bags for storage, and can be opened for use when used, so there is no problem of trapped materials. Because the materials have been trapped during the storage process. This type of production extrusion is generally only used for export products.
Refractory plastics are not extruded for domestic use. A part of the binder is added during the production process, and the material is trapped during the transportation process. When using, open it and add the remaining binder to mix it, and it can be used directly. But it should be noted that the time must be controlled within 18-24 hours. If it is a short-distance transportation, just control the time and use it. Trapping the material on site delays labor. If the material is trapped first, there is no need to trap the material on site, which saves time and meets the construction needs.
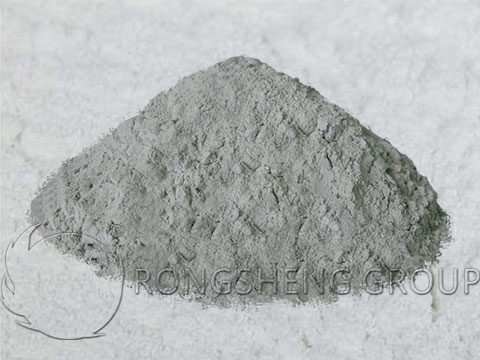
How Can Refractory Plastic be Constructed to Achieve Zero Expansion?
Refractory plastic is easy and quick to construct, and the use state is stable. If you want to achieve zero expansion of plastic, you need to adopt a zero expansion design to offset the expansion and contraction of plastic at high temperature.
Plastic has a certain plasticity at high temperature. Zero expansion of plastic means that it can withstand drastic changes in furnace temperature and resist frequent shutdowns and temperature increases. The mold can be removed immediately after the plastic is constructed. If it is for maintenance, it does not need to be baked and can be put into use directly as the furnace temperature rises.
However, during construction, attention should be paid to the mold drawing construction to ensure that the deformation of the steel structure and the lining furnace is synchronized. In addition, the anchor bricks must be evenly stressed to avoid breakage and collapse during use.
Zero expansion design of refractory plastic
Zero expansion design means that during construction, the mold is first set up to ensure that the construction site is clean, and then the refractory plastic blank is laid on the ramming site. Only a single layer of material can be laid each time, and the hammer head is downward, and the plastic is moved back and forth to make it flat and dense. If the construction reaches the anchor brick, the ramming surface of the refractory plastic should be 16 to 20 mm higher than the bottom surface of the anchor brick. Put the wooden mold on the anchor brick, straighten it and hammer it to make a tooth mark, and the plastic around the anchor brick should be rammed densely.
The construction of refractory plastic should be laid and rammed layer by layer, and each layer should be scraped to keep the same height as the construction surface. If there is a break in the ramming of plastic, the rammed surface should be covered with plastic cloth. If it snows, the surface of the material should be shaved. When the construction is interrupted for a long time, the joint should be left between the two rows of anchor bricks.
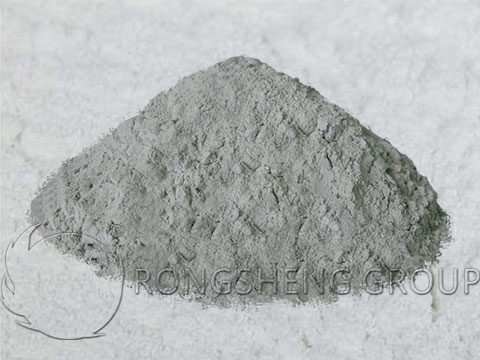
Description of the Plastic Refractory Used on Furnace Roof
If plastic refractory is used on furnace roof, the force direction of hammer head should be horizontal when ramming, and the material surface joint and furnace roof working surface should be vertical. The peeling layer and material surface joint should not overlap during production. Plastic should be rammed from the material joint on furnace roof. During construction intervals, cut the material vertically into right angles to the furnace shell and cover it with plastic cloth to prevent water loss. Before anchoring bricks or hanging bricks, wooden mold bricks with the same tooth shape should be used to tighten and drive into plastic. After the tooth mark is formed, the anchor brick is embedded and tightened.
After plastic construction, the mold should be removed as soon as possible to dissipate the moisture. When trimming, the plastic around the end of the anchor brick is gently tapped with a wooden hammer or a ramming hammer to make it fit tightly. Trimming includes scraping, piercing air holes or cutting expansion joints.
During construction, refractory plastic cannot come into contact with water; when constructing castables in contact with plastic, waterproofing of plastic is also required; the formwork should be removed as soon as possible before baking to allow the masonry to dry naturally.
Due to the “zero expansion” design of refractory plastic, cracks and expansion areas of the masonry after drying and baking are filled with refractory fibers. To prevent the furnace lining from catching fire and smoking at low temperatures, the cracks and expansion joints will close at around 1350℃.
What is the Effect of the Size of Refractory Plastic Particles when Used?
The particle size of refractory plastic has an effect on construction, but has no effect on use. On the contrary, plastic with large particles will have a longer service life. However, it should be noted that there are still requirements for particles in special parts, especially those that are difficult to construct. The main reason is that if the particles are large, it is not easy to ram and construct, and the construction efficiency is low when the particles are too large. However, if the particles do not exceed 10mm, as long as the construction can go smoothly, there will be no problem in use. And the service life is longer than that of plastics below 3mm.
Plasticity index of refractory plastic. The plasticity index of refractory plastic is 15-40%. If the plasticity index is lower than 15%, the plastic will be too hard and cannot be constructed. However, if the plasticity exceeds 40%, the material will be too soft. Neither too hard nor too soft are not easy to construct, and they are not dense when rammed. The most suitable state of the refractory plastic index is that it can be kneaded into a ball by hand, without water seepage or stickiness.
Refractory plastic has its own characteristics. Generally, the strength at room temperature is low, the strength at medium temperature does not decrease, the strength at high temperature is high, and the thermal shock and peeling resistance are good. However, the rammed lining during construction must be welded with anchors or supports to improve the performance of refractory plastic and extend its service life.
In short, whether the refractory plastic is trapped on site during construction or the manufacturer adds binders to trap the material, the particle size does not affect the use. On the contrary, the production process ratio of larger particles will have a longer service life than the refractory plastic with smaller particles.