Application of alumina-magnesia carbon bricks in ladles. In order to improve the service life of continuous casting ladles and meet the needs of the development of efficient continuous casting technology, alumina-magnesia carbon bricks for ladles were developed. It can be used in various types of continuous casting ladles to greatly increase the service life of the ladles. Aluminum-magnesium carbon ladle bricks are used in a 300t continuous casting ladle in a steel plant. The ladle age has increased from more than 20 times when first-class high alumina bricks were used to more than 80 times, and the highest is 126 times. There is also a 200t fully continuous casting ladle in a steelmaking plant with out-of-furnace refining, which uses alumina-magnesia carbon bricks and has an average lifespan of 64 times and a maximum of 73 times. The promotion of high-quality aluminum-magnesia-carbon refractory bricks for ladles and the use of aluminum-magnesia-carbon ladle lining bricks have significantly increased the life of the ladle. For example, after using alumina-magnesia carbon lining bricks for a 160t ladle, the average service life is increased to 90 times, and the maximum is 115 times.
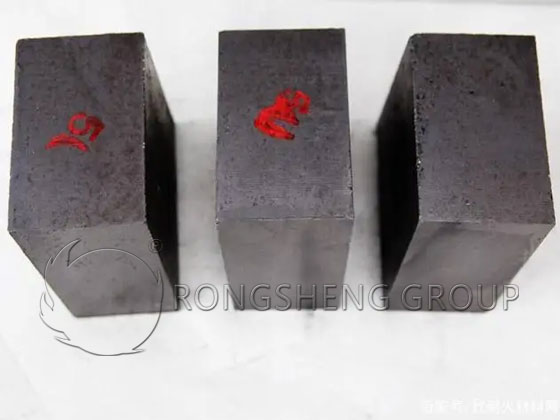
Alumina-magnesia carbon bricks are unfired products made of special-grade high-alumina bauxite clinker, fused magnesia or sintered magnesia and graphite as raw materials, and liquid phenolic resin as a binder. This product has good slag erosion resistance, strong corrosion resistance, good thermal shock resistance, and low price, and is mainly used in the non-slag line parts of the ladle.
Construction Technology and Requirements of Alumina-Magnesia Carbon Bricks as Ladle Lining
Construction sequence of alumina-magnesia carbon bricks as ladle lining. Pouring of the permanent layer of the cladding → Pouring of the permanent layer of the bottom of the cladding → Placement of nozzle seat bricks → Construction of breathable bricks and bottom alumina-magnesia carbon bricks → Filling the gaps with corundum cement → Construction of wall-clad alumina-magnesia carbon refractory bricks and slag-clad magnesia carbon bricks Brick masonry → Aluminum-magnesium castable masonry → Curing → Baking.
Wall-clad alumina-magnesia carbon brick masonry construction
- 1) Use aluminum-magnesium fire mud for wet masonry, and the masonry mud should not be too thin. The mud between the brick joints needs to be full, and the brick joints should be less than 1mm.
- 2) Each layer of bricks is laid flat, and the brick joints between layers must be staggered. During masonry construction, the principles of “solid backing, tight seams, and arc closing” should be followed, and the joints between the upper and lower layers must be staggered.
- 3) The size of the cutting door closing brick should be no less than 50mm, and the door closing part should avoid the trunnion position. The door closing positions between layers should be staggered by more than 200mm.
Bottom masonry construction technology
- 1) The breathable bricks and nozzle seat bricks must be placed flat and in the correct position.
- 2) After the nozzle seat bricks and breathable bricks are in place, the gaps between them and the surrounding bottom bricks are filled with corundum cement.
Pouring construction requirements
- 1) Check construction equipment, mixers, water supply, vibrators, etc.
- 2) Turn on the mixer, add the mixture, dry mix for 1 minute, then add 2/3 of the water. Then slowly add the remaining water and mix wetly for 3 to 5 minutes before discharging.
- 3) Use a vibrating rod to vibrate after each pouring of the rolling material, and the pouring material is required to be fully exhausted.
- 4) The pouring construction must be consistent before and after, and the stop time during the process shall not exceed 20 minutes.
Construction requirements for bottom excavation and repair
- 1) Remove the seat bricks and their surrounding cementing material and clean them.
- 2) Lift the new breathable bricks and seat bricks into their placement locations.
- 3) Use corundum cement to fill the gaps between the breathable bricks, the nozzle bricks and the bottom alumina-magnesia carbon bricks.
Good construction technology, coupled with the correct construction by skilled construction workers, can not only ensure the high performance of the refractory lining material but also very likely increase the service life of the refractory lining. To purchase high-quality ladle lining refractory materials, please choose RS Kiln Refractory Factory. We not only provide high-quality refractory lining materials, but we also provide comprehensive customer service to ensure the efficient operation of refractory materials.