Magnesia carbon bricks are produced from two raw materials, magnesium, and carbon, through a series of processes. It has high thermal conductivity and mechanical strength, so it is widely used in high-temperature occasions such as metallurgical smelting and steel smelting. During use, mgo c brick has good wear resistance and fire resistance and can exist stably at high temperatures. This is due to the strict selection of magnesia carbon bricks for paint refractory raw materials. Among them, the influence of graphite purity on the finished magnesia carbon brick cannot be ignored.
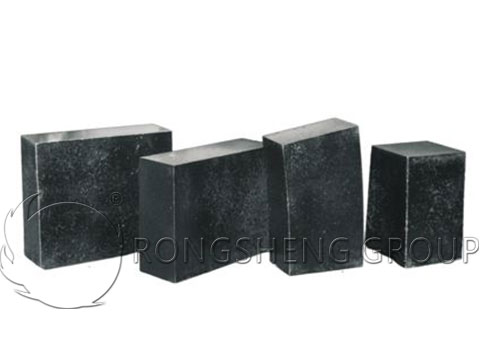
Magnesia Carbon Brick Production Process
Generally, magnesia carbon bricks are unburned bricks made of magnesia and flake graphite with thermosetting resin added as a binding agent, with or without antioxidants. The production process of magnesium carbon bricks is very complex, requiring high-temperature reactions and multiple processes. The most important link is the sintering of the bricks. Bricks form crystals at high temperatures and release a large amount of gases, which have a crucial impact on the quality of sintering. Therefore, strict monitoring and management are required during the production process to ensure product quality and stability.
Graphite has a layered structure, and the atoms in the layer are arranged in a hexagonal arrangement with strong covalent bonds. There are van der Waals forces between layers, which makes it have strong directionality, that is, obvious anisotropy. The layer and the entire surface contain low energy and hardly wet liquid high-temperature slag and molten steel. Graphite has high thermal stability without melting, and ion migration is very limited. It is impossible to recombine the ionic bonding between magnesium oxide in mgo c brick and the covalent bonding of graphite. Therefore, the second binder is needed to form a network structure and obtain greater strength. However, it has free valence bonds at the boundary and can adsorb various substances. Flake graphite has higher oxidation resistance than other carbon products, and this oxidation resistance also improves the wear resistance of magnesia carbon bricks.
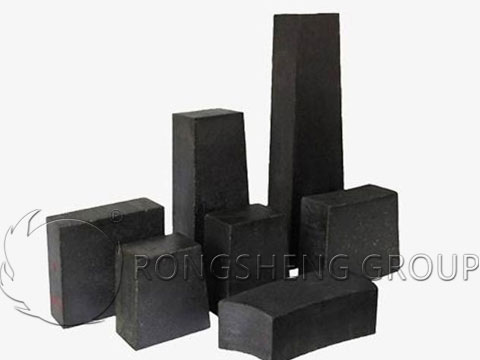
The Relationship between Graphite Purity and Magnesia Carbon Bricks
The purity and additional amount of flake graphite play an extremely important impact on the performance of magnesia carbon bricks. Its appropriate addition can effectively inhibit slag from intruding into the refractory structure.
Research shows that mag carbon bricks with a carbon content of 15% have better resistance to slag erosion. The main factors that directly affect the performance and use of magnesia carbon bricks include the fixed carbon content in graphite, graphite particle size, shape, and volatile content. The more added, the more ash will be brought in. The purity of graphite affects the anti-flaking performance and high-temperature flexural strength of magnesium carbon bricks. The main component of ash is silica, followed by alumina and iron oxide. At operating temperatures, silicon oxide and iron oxide are easily reduced and oxidized graphite during use, so they are particularly harmful to mgo c brick. As the carbon content increases, the volume density of magnesia-carbon bricks decreases, the strength at room temperature decreases, and the corrosion resistance index drops sharply. The effect on high-temperature flexural strength is not significant, but the peeling resistance is increased. In short, the appropriate amount of graphite added is related to the type of furnace, different parts used, and respective operating conditions. It is usually determined based on whether the magnesia carbon bricks uses conditions that emphasize corrosion resistance or thermal shock stability, or require high strength or oxidation resistance.
In addition, a large number of studies have shown that graphite purity is directly related to the high-temperature flexural strength of magnesia carbon bricks and the melting loss rate during use. The high-temperature flexural strength of mgo c brick increases with the increase of graphite purity. This is due to the difference in the microstructure of magnesium carbon bricks. Mag carbon bricks made of lower-purity graphite have a larger proportion of coarse pores (diameter 20 μm) after carbonization treatment at 1000°C, and their porosity is also higher than products made of high-purity graphite. This may be related to the high flexibility of high-purity graphite and its easy compression during brick-making. Another point is the local weakening of the structure of mag carbon bricks made with lower-purity graphite. After magnesia-carbon bricks are treated at a high enough temperature (such as 1600°C), the silicate minerals associated with graphite melt into the glass phase and react with magnesia or carbon. The original mineral is corroded, the volume is reduced, the contact area is reduced, and a pore zone is formed around the graphite. As a result, the high-temperature strength of magnesia-carbon bricks decreases with the decrease in graphite purity.
The melting loss rate of magnesia carbon bricks decreases with the increase of graphite purity, especially for graphite with a purity greater than 95%. Research on its mechanism shows that above 1300°C, impurities (SiO2, CaO, Al2O3, Fe2O3, etc.) in magnesia and graphite gather at the interface between the two. Low melting materials are generated, making the magnesia particles easily corroded by the slag and flowing into the slag, thus reducing the erosion resistance. Actual magnesia carbon bricks uses results show that the slag resistance of mag carbon bricks made of graphite containing more than 95% carbon electricity is 0.51 times higher than that of ordinary magnesia-carbon bricks.
The use of high-carbon flake graphite with a carbon content greater than 95% to 96% is an effective technical measure to not only improve the quality of mag carbon bricks but also reduce the cost of brickmaking. If the performance of bricks made from graphite and magnesia of the same grade is used as a benchmark, then switching to high-grade graphite will improve brick performance much more than increasing the grade of magnesia. Under the same process conditions, the performance of bricks made of high-grade graphite and low-grade magnesia raw materials is better than that of bricks made of high-grade magnesia and low-grade graphite raw materials. However, it must be noted that when graphite with higher purity is used, less liquid phase is generated in the brick, and oxygen is easily concentrated into the brick, causing oxidation and decarburization of the graphite. For this reason, antioxidants such as metal Al, Si, Al-Mg alloy, SiC, BN, etc. must be added.
RS Magnesia Carbon Brick Manufacturer
This allows it to be used in the manufacture of various high-temperature furnaces and vessels. For example, high-temperature occasions such as steel smelting furnaces, converters, and large ladles. Compared with traditional refractory materials, magnesia carbon bricks have better mechanical strength and thermal conductivity. Therefore, it has broad application prospects in steel smelting and other fields. Its production process is very complex and requires strict monitoring and management to ensure product quality and stability. RS magnesia carbon brick manufacturer can provide you with high-quality magnesia carbon refractory, as mgo c brick, contact us to get free samples and quotations.