Semi-Silica Refractories generally use silica as the main component and a glassy matrix as a binder. The silica content is about 75% to 93%. The raw materials are silicon-containing clay, sand and refractory mortar. According to the Kiln Refractories Blog, it can resist slag erosion and is used in open hearth furnaces.
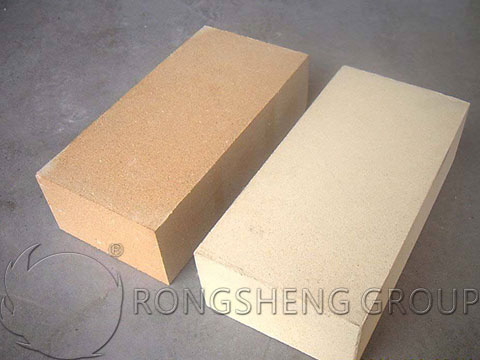
Brief Introduction of Semi-Silica Refractories
The Semi-Silica Refractories have an A12O3 mass fraction less than 30% and a SiO2 mass fraction greater than 65%. It is a kind of refractory material that is made of wax stone, siliceous clay or primary kaolin and its tailings, coal gangue and other main raw materials, combined with clay as a binder.
Whether in China or international standards, there is no definition of Semi-Silica Refractories. However, refractory materials with a SiO2 mass fraction greater than 85% and less than 93% are defined as silica refractory materials. It also defines Al2O3, aluminum-silica refractories with a mass fraction of 30% to 48% as clay refractories. Traditionally, aluminum-silicon refractory materials with Al2O3 mass fraction between 15% and 30% are called semi-silica refractory materials. The crystal phases are cristobalite, mullite, and a certain number of glass phases. Its typical representative is wax stone brick.
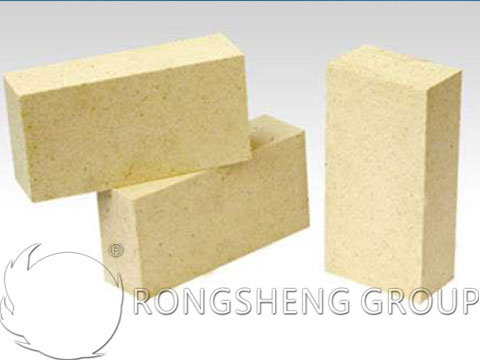
-
Raw Material of Wax Stone
The most commonly used raw material for producing semi-silica refractory materials is wax stone. The wax stone mine is composed of pyrophyllite, quartz, kaolinite, mica and so on. The ore is dense and massive, with a waxy luster. Different colors due to different impurities, such as gray, wax yellow, light brown, meat red, etc. It has a greasy feel, very similar to talc. China is rich in waxstone resources, mainly distributed in the volcanic rock development area on the southeast coast, of which there are many mining sites in Fujian and Zhejiang.
1.1 Chemical mineral composition of pyrophyllite
Pyrophyllite is a water-containing silicate mineral. In theory, A2O3 accounts for 28.3%, SiO2 accounts for 66.7%, and H2O accounts for 5%. A complex layered structure is formed by two layers of hexagonal silicon-oxygen tetrahedral mesh layer sandwiched by a layer of “aluminum hydroxide” octahedron (aluminum oxyhedron). Pyrophyllite is also known as Qingtian stone, Shoushan stone, seal stone, wax stone, etc. Can be divided into pyrophyllite wax stone, siliceous wax stone, kaolinite wax stone and diaspore wax stone. Often contains a certain amount of Fe2O3, CaO, R2O and other impurities.
1.2 Basic properties of wax stone
Due to the different mineral composition of wax stone, their differential heat curves are obviously different, and there are different endothermic and exothermic peaks. It can be seen that the sample will expand in a certain temperature range before being sintered. The reason is that the lattice expands and the aluminum oxide and silicon oxide layers are separated. Vigorous expansion began at about 700 ° C, dimensional changes at 900 ° C tended to be gentle, and 1100 ° C began to shrink. This expansion characteristic is the basis for the wax brick’s micro-expansion characteristic. Raw wax stone has very low hardness and is a commonly used engraving material, but its hardness and strength have been greatly improved after calcination. In addition, pyrophyllite has good chemical stability and can only be decomposed by sulfuric acid at high temperature.
-
Key points of production process of semi-silica brick
The manufacturing process of semi-silica brick is basically similar to that of clay bricks. The biggest difference is that semi-silica bricks can be made of raw materials. The main points of its production process are as follows.
(1) When using natural silica clay and wax stone, it is necessary to decide whether to add clinker according to the nature of the raw material and the use conditions of the finished product. Raw materials can be used to make bricks directly. It is also possible to add part of the wax stone raw materials to the mature materials after calcination, or add% to 20% of clay clinker to replace natural silica clay.
(2) If quartz sand or silica is added as barren material, the particle size should be determined according to the product performance requirements. In general, if there are many raw material impurities and fine quartz particles, the fire resistance of the resulting product is low, the thermal shock stability is reduced, but the strength is increased. If the quartz particles used are large, the strength of the product is low, but the thermal shock resistance is enhanced and the load softening temperature is increased.
(3) The water content of raw wax stone is small (less than 7%). When the whole wax stone or a small amount of combined clay ingredients are added, the mud water is low and the bonding performance is poor. At the same time, in the process of using wax stone bricks, it is generally subjected to repeated heating and cooling, the expansion amount gradually increases, and the bulk density further decreases. Therefore, high-pressure molding should be used, generally the molding pressure is above 50 MPa. Some molding pressure is 50 ~ 100 MPa, or use vacuum degassing brick machine to mold high-density wax stone brick with high volume stability. This wax stone brick has small air permeability and small pore diameter, which can improve durability.
(4) The maximum firing temperature varies with the characteristics of the raw materials used. Low temperature firing is usually used, and the temperature is 150 ℃ lower than that of clay bricks with lower firing temperature, and generally does not exceed 1200 ℃. Cool slowly after firing.
-
Performance characteristics and application of semi-silica brick
The semi-silica brick produced with pyrophyllite as the main raw material has a refractoriness greater than 1700 ° C. It does not shrink at high temperature but has a slight expansion. It has good thermal shock resistance, can withstand the impact of steel slag and metal, and has strong creep resistance. Its micro-expansion is conducive to improving the integrity of the masonry and weakening the erosion of slag on the masonry along the brick joints. At the same time, glaze-like substances with high viscosity can be formed on the surface of semi-silica bricks during high-temperature use to prevent the penetration of slag into the bricks, thereby improving the ability to resist erosion of the slag. In order to improve the performance of semi-siliceous bricks, it is sometimes necessary to add some other substances, such as adding mullite, high-alumina clinker, and zircon to increase the heat resistance of refractory bricks.
Semi-silica bricks are mainly used for ladle bottom lining, ladle lining, pouring steel bricks and kiln flue. With the increasing requirements for steel quality, the amount of semi-silicon bricks used in the steel industry has been very small. In addition to wax stone, other semi-silicon materials and minerals can also be used to make semi-silicon refractory materials.