In the process of building refractory bricks lining, for those who do not know much about refractory materials, the difference between refractory mortar and refractory cement is difficult to distinguish. When should I choose refractory cement and refractory mortar? The technical staff of Rongsheng refractory manufacturer gave the following explanation.
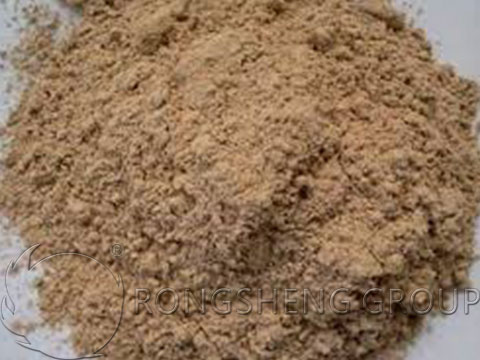
The furnace lining material can be made of refractory bricks or directly cast by refractory castables.
When building refractory brick lining, the special joint material or bonding material needed is refractory mortar.
Because the refractory bricks are piece by piece, the complete refractory lining material requires that the refractory bricks are to be tightly linked together and not fall off. Therefore, a kind of binder is used when refractory bricks are used for kiln linings building. This kind of binder is called refractory mortar or seam material. They are refractory slurries reconciled with refractory mortar and water. It is the main auxiliary material for refractory brick masonry and the seam filler for the bonding of refractory bricks.
The choice of refractory mortar material needs to be selected strictly in accordance with the material of the refractory brick used in the construction of the refractory lining. Do not mix! There are as many types of refractory bricks as there are refractory mortar materials. Commonly, high alumina refractory mortar is used for masonry high alumina bricks, magnesium refractory mortar is sampled for masonry magnesiate bricks, and silica refractory mortar is used for masonry silicon bricks.
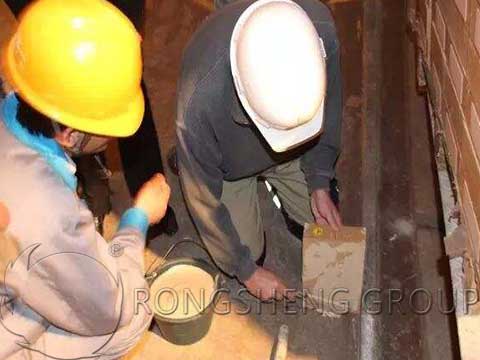
How to use refractory mortar
The supply method of refractory mortar is supplied as dry powder. When used, it is mixed with liquid gelling agent to form a viscous slurry. This kind of mortar is collectively called high temperature refractory mortar, high temperature refractory mud or high temperature binder. According to the combination method of liquid gelling agent, it is divided into: water glass combined refractory mortar, phosphoric acid combined refractory mortar, aluminum phosphate combined refractory mortar, etc. In addition to being used as a bonding material, refractory mortar can also be used as a protective coating for furnace linings by smearing or spraying.
The refractory lining material can also be completed by painting, spraying and pouring.
When the refractory castable is casting, a binder is needed to bond the refractory feedstock together. So that the refractory lining material can be firmly fixed on the lining of thermal equipment. The binder used here is generally refractory cement.
Refractory cement, also called aluminate cement or high alumina cement. Aluminate cement is often yellow or brown, and sometimes gray. The main mineral composition of aluminate cement is calcium aluminate (CaO · Al2O3, CA), other aluminates, and a small amount of dicalcium silicate (2CaO · SiO2). Refractory cement forms eutectics under the action of high temperature. When configuring refractory castables, excessive addition will reduce the high-temperature performance of the castables, usually using silica powder to replace part of the refractory cement.
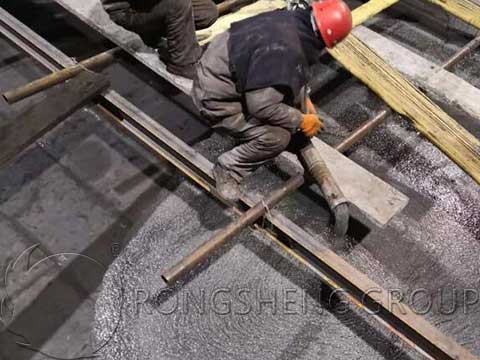
In Conclusion
The biggest difference between refractory mortar and refractory cement is that refractory mortar is used for refractory bricks (mixed with water or other liquids). The refractory cement is used as a binder material for various refractory aggregates, and the refractory castables made of it are used as lining materials for kilns.