In the realm of advanced manufacturing, high-performance ceramics have become indispensable due to their unique properties, including hardness, thermal stability, and resistance to wear and corrosion. Among the various materials used to produce these ceramics, zirconium silicate, particularly in the 63-65% purity range, stands out as a crucial component. This blog post delves into the importance of zirconium silicate in high-performance ceramics, exploring its properties, applications, and why it is favored by manufacturers.
Zirconium Silicate (ZrSiO₄) 63-65%
Zirconium silicate (ZrSiO₄) is a naturally occurring mineral derived from zircon. It is processed into a fine powder, which is then used in various industrial applications, most notably in ceramics. The 63-65% purity range of zirconium silicate refers to the concentration of zirconium in the material, which is essential for achieving the desired performance characteristics in high-performance ceramics.
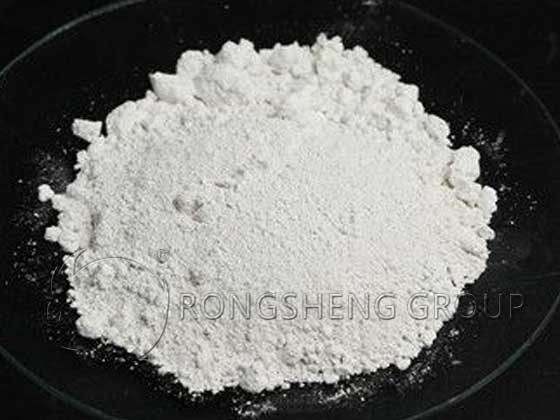
Key Properties of Zirconium Silicate
Zirconium silicate possesses several properties that make it ideal for use in high-performance ceramics:
- High Melting Point: With a melting point of approximately 2550°C, zirconium silicate exhibits excellent thermal stability. This property is vital in ceramic manufacturing, where materials are subjected to extreme temperatures during processing and in their final applications.
- Chemical Inertness: Zirconium silicate is chemically stable and does not react with most substances. This chemical inertness is crucial in preventing degradation or unwanted reactions during the production and use of ceramics, ensuring that the material retains its integrity over time.
- Hardness: The hardness of zirconium silicate contributes to the strength and durability of ceramic products. It enhances the resistance of ceramics to mechanical wear and tear, making them suitable for demanding applications.
- Low Thermal Expansion: Zirconium silicate has a low coefficient of thermal expansion, meaning it does not expand or contract significantly with temperature changes. This property helps to prevent cracking and warping in ceramics, particularly during rapid heating or cooling.
- Opacity: In ceramic glazes, zirconium silicate is often used as an opacifier, giving the ceramics a bright, white appearance. This opacity is important for achieving consistent color and finish in ceramic products.
The Role of Zirconium Silicate in High-Performance Ceramics
Zirconium silicate 63-65% plays a vital role at various stages of ceramic manufacturing, contributing to both the aesthetic and functional properties of the final products.
Structural Ceramics:
High-performance structural ceramics are used in applications where strength, durability, and resistance to extreme conditions are paramount. Zirconium silicate is often incorporated into these ceramics to enhance their mechanical properties. The material’s hardness and low thermal expansion make it ideal for components that must withstand heavy loads, high temperatures, and thermal cycling without losing their structural integrity.
For example, zirconium silicate is used in the production of ceramic engine components, cutting tools, and protective coatings. These applications demand materials that can perform reliably under stress, and zirconium silicate’s properties make it a preferred choice for such uses.
Refractories:
In the production of refractory ceramics, which are used to line furnaces, kilns, and other high-temperature environments, zirconium silicate 63-65% is invaluable. Its high melting point and chemical inertness ensure that refractory ceramics can endure extreme heat and exposure to aggressive chemicals without degrading.
The inclusion of zirconium silicate in refractory ceramics improves their thermal shock resistance, allowing them to withstand rapid temperature changes without cracking. This makes these ceramics ideal for use in industries such as metallurgy, glass manufacturing, and petrochemicals, where reliable performance in harsh conditions is essential.
Ceramic Glazes:
Zirconium silicate is widely used in the production of ceramic glazes. It acts as an opacifier, providing the glaze with a bright white color and enhancing its opacity. This is particularly important in the production of decorative ceramics, such as tiles, dinnerware, and pottery, where consistent color and finish are key to the product’s aesthetic appeal.
Additionally, zirconium silicate improves the hardness and durability of ceramic glazes, making them more resistant to scratching, chipping, and wear. This ensures that the finished ceramics not only look good but also have a long lifespan, even in demanding environments.
Advanced Ceramics:
Zirconium silicate 63-65% is also used in the production of advanced ceramics, which are engineered for specific industrial applications requiring exceptional performance. These advanced ceramics are used in fields such as electronics, aerospace, and biomedical engineering, where materials must meet stringent standards for strength, durability, and resistance to extreme conditions.
In the electronics industry, for instance, zirconium silicate is used in the production of ceramic substrates and insulators that must operate reliably at high temperatures and in the presence of electrical stress. In the biomedical field, zirconium silicate ceramics are used in the production of implants and prosthetics, where biocompatibility and wear resistance are critical.
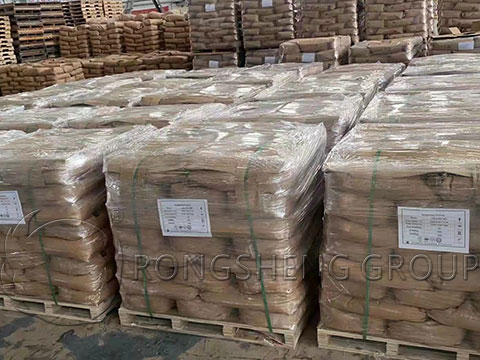
Advantages of Using Zirconium Silicate in High-Performance Ceramics
The use of zirconium silicate 63-65% in high-performance ceramics offers several significant advantages:
- Enhanced Durability: The hardness and thermal stability of zirconium silicate contribute to the durability of ceramic products, ensuring that they can withstand wear, heat, and chemical exposure without degrading.
- Improved Aesthetics: Zirconium silicate’s ability to enhance the opacity and whiteness of ceramic glazes leads to visually appealing products with consistent finishes, which is important in both decorative and functional ceramics.
- Consistency and Quality: The fine particle size and chemical stability of zirconium silicate powder ensure uniform distribution within the ceramic body and glaze, resulting in high-quality, defect-free products that meet industry standards.
- Versatility: Zirconium silicate can be used across a wide range of ceramic applications, from structural components and refractories to decorative glazes and advanced ceramics. Its versatility makes it a valuable material for manufacturers seeking to produce high-performance products.
- Cost-Effective: While zirconium silicate is a high-performance material, it is also cost-effective, offering manufacturers a reliable and affordable solution for enhancing the quality and performance of their ceramic products.
Zirconium Silicate 63-65% is an Essential Material
Zirconium silicate 63-65% is an essential material in the production of high-performance ceramics, offering unique properties that enhance the strength, durability, and aesthetic appeal of the final products. Its high melting point, chemical stability, hardness, low thermal expansion, and opacity make it a preferred choice for a wide range of ceramic applications, from structural and refractory ceramics to glazes and advanced industrial components.
As the demand for high-performance ceramics continues to grow, zirconium silicate will remain a cornerstone of ceramic manufacturing, enabling manufacturers to produce reliable, high-quality products that meet the stringent demands of modern industry. Whether in traditional applications or cutting-edge technologies, zirconium silicate 63-65% will continue to play a crucial role in shaping the future of ceramics. Free quote at Sales@kilnrefractory.com.