In the production and sales of unshaped refractories, RS refractories manufacturer has concluded through the accumulated experience of more than ten years. When using silicon carbide castable refractory, not only the Advantages and disadvantages of silicon carbide castable refractory, the refractory castable price, but also the working environment of the refractory material need to be determined.
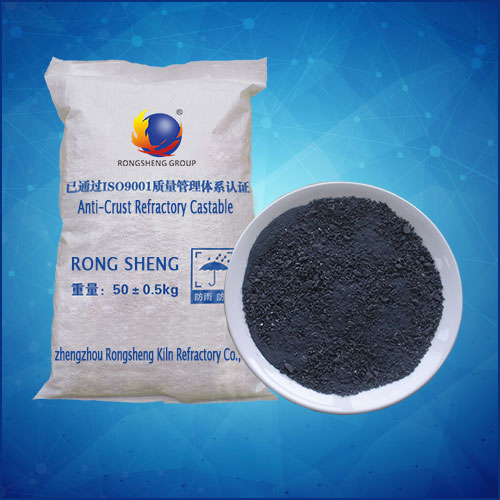
Silicon carbide (SiC) is an excellent wear-resistant and refractory raw material. In order to improve the wear resistance when configuring refractory castables, in addition to corundum, an appropriate amount of silicon carbide can be added to improve its wear resistance. Silicon carbide is made of natural silica and coke with SIO2 content greater than 97% as basic synthetic raw materials, and is synthesized at 2000-2500 ° C using an electric furnace. It has the advantages of small thermal expansion coefficient, Mohs hardness 9.0 ~ 9.5, and strong chemical stability.
Silicon Carbide Castable Refractory Advantages
The biggest advantage of silicon carbide refractory castables is that it has high thermal conductivity, low thermal expansion, and does not react with slag. It has been used as a slag reaction and high temperature spalling kiln parts very early.
Silicon Carbide Castable Refractory Disadvantages
- The biggest disadvantage is that, it is chemically unstable under certain atmospheres. Silicon carbide castable refractory is easy to be corroded in the atmosphere of oxidizing gas such as (oxygen, water vapor, carbon monoxide, carbon dioxide) and iron oxide. And it is easy to be oxidized and decomposed in the molten iron and vacuum.
- Another disadvantage, due to the poor water solubility of silicon carbide, in water-based monolithic refractories such as castables, the silicon carbide refractory castables may have poor fluidity, resulting in poor density of the silicon carbide refractory castables.
- The third disadvantage is the lack of sintering and difficulty in obtaining high strength. However, silicon carbide refractory castable are sometimes difficult to cause over-sintering and shrinkage, but they have advantages in unshaped refractories.
In the actual environment of the use of unshaped refractory castables, Advantages and disadvantages of silicon carbide castable refractory may have an impact on specific production. If we can carry out the production operations correctly and carry out the correct construction of refractory castables, we can avoid bad situations. Therefore, the construction party must follow the construction instructions for refractory castables. The production process also requires careful operation. If you want to know more about silicon carbide castable refractory, please contact us. Rongsheng refractory manufacturer is looking forward to cooperate with you.