In recent years, due to the vigorous development of out-of-furnace refining technology and continuous casting technology, the ladle is also used as a vessel for holding molten steel and molten steel refining equipment, which greatly extends the residence time of molten steel in the ladle. This is accompanied by an increase in the tapping temperature and more severe smelting conditions. As a result, the service life of the inner lining of the ladle is greatly reduced. The ladle uses alumina-magnesia castables, including spinel-containing castables, and it has always been a development trend for integral casting.
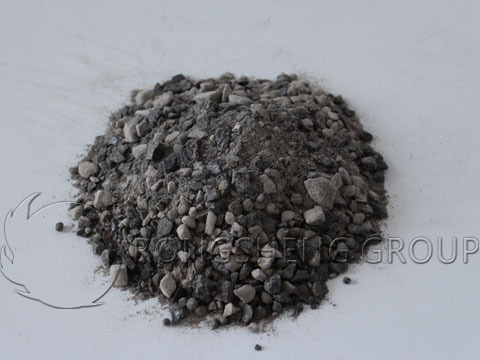
The Combination Method of Alumina-Magnesia Castable
Binder is an important part of alumina-magnesia castables. The bonding methods used for alumina-magnesia castables are generally calcium aluminate cement bonding, silica micro-powder bonding, hydrated alumina bonding, sol bonding, magnesium silicon water bonding, and so on.
Cement bonding
At the initial stage of development of alumina-magnesia castables, pure calcium aluminate cement is used. This is because the cement calcium aluminate will react with the Al2O3 in the matrix to form CA6, which is a highly refractory phase. However, as the number of cement increases, the fluidity of the castable decreases. At the same time, due to the excessive content of CaO at high temperatures, it will react with SiO2, Al2O3, and MgO in the matrix to generate a low-melting phase, which will reduce the high-temperature performance of the castable. Some refractory researchers have studied the effect of the amount of water added in cement on the thermal expansion behavior of alumina-magnesia castables after high-temperature firing. The results show that with the increase of cement addition, the phases of CA2 and CA6 in the sample increase, and the linear change rate of the sample after high-temperature heat treatment increases. In addition, some people have studied the influence of silica powder, magnesia, and cement on the properties of high-purity alumina-magnesia castables. The study pointed out that the pure calcium aluminate cement and the Al2O3 fine powder in the matrix start to react at about 1000°C to form CA2 and CA6, and the reaction is accompanied by volume expansion. It can reduce the intensity ratio after high- and medium-temperature firing, and also contribute to the improvement of the high-temperature performance of the sample.
MgO-SiO2-H2O combination
There are many kinds of researches on the combination of MgO-SiO2-H2O. The combination of MgO-SiO2-H2O is used in the alumina-magnesia castable. On the one hand, due to the polymerization of SiO2 gel formed by the interaction of SiO2 powder and water, the amount of water added is reduced, and the fluidity of the castable is greatly improved. On the other hand, the combination of MgO-SiO2-H2O can inhibit the hydration of magnesia, but too much silica powder will form a low-melting phase with impurities in the matrix. At the same time, the forsterite phase formed by the reaction of magnesia and silica powder in the matrix has poor thermal shock stability at high temperatures.
Composition Materials and Properties of Low Cement Alumina-Magnesia Refractory Castables
The slag resistance of low-cement alumina-magnesia refractories is similar to that of alumina-magnesia spinel castables but superior to alumina-spinel castables. Therefore, it is selected by users at home and abroad, especially in the Japanese steel ladle. In addition, the material is used in the desalinization pouring channel of the large-scale blast furnace tapping channel, and its life is longer than that of the Al2O3-SiC-C iron channel material.
The high-tech basis of low-cement alumina-magnesia refractory castables is high-grade raw materials and scientific formulas. Construction, baking, and careful process operation and maintenance are the guarantees of its long life. This material is used on a ladle of about 100 tons, and the ladle age is 60 ~ 120 times.
The performance of low cement alumina-magnesia refractory castables is excellent. The content of MgO is not more than 8%, and the content of Al2O3 is 89% ~ 97.6%, indicating that the material is excellent. The linear changes after firing are all positive values, the pores are low, and the strength is high, which is beneficial to the use of castables.
Low-cement alumina-magnesia refractory castables are developed on the basis of sodium silicate alumina-magnesia refractory castables and have been used on medium and small ladles with good results. When higher-grade refractory raw materials are used and the material formula is designed with scientific methods, high-tech low-cement alumina-magnesia refractory castables can be successfully formulated. It can be used on large and medium-sized ladle to improve the age of the ladle.
For more detailed information about refractory castables for kiln furnaces, please visit the website of Rongsheng Kiln Refractories Website: https://kilnrefractory.com/.