What kinds of refractory castable should be used when the refractory castable is used at a temperature of 1300°C? This is determined according to the different working conditions of different furnace types. But no matter what castable you choose, the ultimate goal is to save energy, reduce production costs, and prolong the service life of the refractory lining.
When choosing castables for high-temperature industrial furnaces, whether it is to choose castable manufacturers or distributors of monolithic refractory materials. First of all, the fuel used in the high-temperature industrial furnace and the material of the raw materials required in the production process must be considered. And whether there are highly corrosive substances in the raw material composition, it is also necessary to determine whether the corrosive substances are acidic or alkaline. In addition, there are external factors of the furnace type to be considered, whether there is wind speed, erosion and wear caused by mechanical stress, etc.
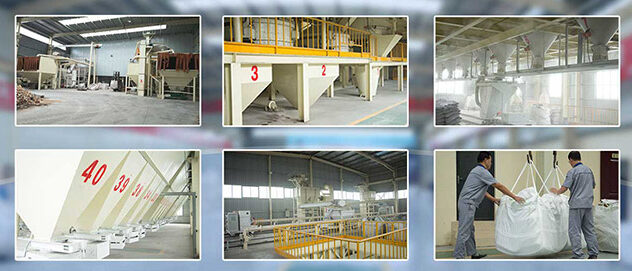
The furnace temperature of 1300°C is the direct contact temperature of the flame, not the refractoriness. This temperature definition is very important. High alumina castables are also divided into different grades and different substrates. If the castable solidifies too quickly in the early stage, it proves that the amount of cement added is too large, or there is a problem with the control ratio of the binder and the micro-powder, which will affect the strength of the castable later.
If the setting time is too slow, the construction temperature should be considered, and the amount added should be well controlled when adding water. When the temperature is low, the drinking water should be heated to 30°C, and then added to the material and mixed for use. If congealed within 40 minutes. Then bake according to a reasonable baking system to ensure the service life of the refractory castable.
Generally, high-alumina castables can be used for the furnace temperature of 1300°C, but if the corrosion is severe, it is necessary to choose acidic or alkaline corrosion-resistant castables according to the nature of the corrosion. If it is acidic corrosion, you can choose water glass bonded castable or phosphoric acid bonded refractory castable, if it is alkaline corrosion, you can choose high wear-resistant castable. Because the high wear-resistant castable is added with silicon carbide, it can resist erosion and play a role in wear resistance.
Application Advantages of Low Cement Castables
The prominent feature of low-cement castables is their dense and high strength, which brings benefits to use but brings troubles to baking, that is, improper baking, prone to peeling or bursting. Therefore, it is very important to formulate a reasonable oven curve and use an excellent explosion-proof admixture, so that the moisture in the molded refractory castable can be removed smoothly without causing any side effects.
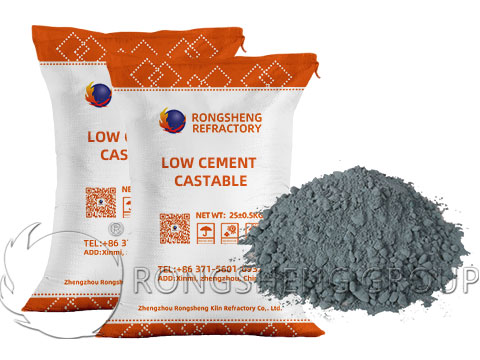
The thermal expansion coefficient of low cement refractory castables shows the characteristics of expansion during the whole heating process. It can be seen that as the heating temperature increases, the thermal expansion rate increases, reaching a value of about 0.68% at 1250 °C. Then it began to shrink slowly, and the thermal expansion rate at 1400°C was 0.43%. When the temperature is 1500°C, the thermal expansion rate returns to 0.5%.
Low-cement refractory castables have a wide range of applications. In industrial kilns such as metallurgy, petrochemicals, machinery manufacturing, electric power, and building materials, such castables have been widely used to replace traditional fired refractory products as linings. Low-cement and ultra-low-cement refractory castables are mainly used as linings of thick dimensions, such as linings for heating furnaces, various heat treatments, electric furnace covers, shaft kilns, rotary kilns, blast furnace tapping hooks, ladles, ladles, etc. The self-flowing low and ultra-low cement refractory castables are mainly used as thin linings and linings of high-temperature refractory components with metal anchors, such as outer linings of water-cooled pipes for heating furnaces, and integral spray gun linings for spray metallurgy.
As the heating temperature rises, the cement stone is gradually sintered, and the crystal form of the castable body begins to transform into mullite crystals. As the temperature continues to rise, the mullite crystals continue to grow, and the matrix glass phase in the castable is in a liquid state, forming a high-temperature ceramic sintered shape, and the strength is significantly improved.
Low-calcium high-alumina cement is a hydraulic material like ordinary cement, and it undergoes hydration reaction and hardening after contact with water. Low cement castable, its main feature is high early strength, 3-7 days room temperature compressive strength can reach more than 30MPa. The disadvantage is that the medium temperature volume stability is poor, and the strength is reduced, and the decline can reach about 40%. Therefore, it is required that the compressive strength at room temperature must meet the requirements of design and national standards. The main factor for the decrease in medium temperature strength is. When the low-calcium and high-alumina cement of the castable body reaches a certain temperature (about 350°C) during the heating process of the heating furnace, the hydrates begin to dehydrate and transform to reduce the cement stone structure, compactness, and strength of the hydrates. The volume of the castable changes and the strength of the castable body drops to a low point at this time and then tends to be stable.
For high-quality refractory manufacturers, please choose RS Kiln Refractory Factory, at sales@kilnrefractory.com to purchase refractory materials with high-temperature resistance of 1300℃.