Mullite brick is a high-quality refractory brick. Mullite brick is made of high-quality high-alumina bauxite clinker as the main raw material. Mix the appropriate amount of clay, ingredients, and water to create a malleable mud or mud. High-quality thermal insulation bricks that are extruded and fired at high temperatures.
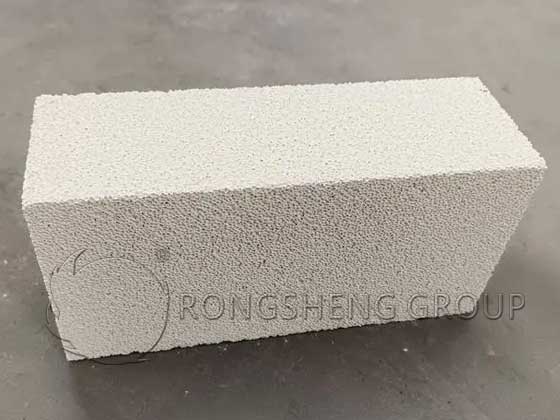
Mullite Insulation Brick Price
According to the brand name, mullite bricks are generally divided into JM23 mullite bricks, JM26 mullite bricks, JM28 mullite bricks, and JM30 mullite bricks. The price of mullite bricks is generally between 2,800 yuan/ton and 4,500 yuan/ton. So, how many mullite bricks are there? The common body densities of mullite bricks are 0.8g/cm³ and 1.0g/cm³. There are about 735 mullite bricks with a body density of 0.8g/cm³ per ton, and there are about 588 mullite bricks with a body density of 1.0g/cm³ per ton. Then you can calculate how much a mullite brick costs.
For example, a ton of 0.8 JM23 mullite bricks is 2,800 yuan, so the price of a piece of JM23 mullite bricks is 2,800 yuan ÷ 735 pieces = 3.8 yuan. 1.0 A ton of JM23 mullite bricks is 2,700 yuan, so the price of a piece of JM23 mullite bricks is 2,700 yuan ÷ 588 pieces = 4.59 yuan.
According to changes in market conditions, if a ton of 0.8 JM28 mullite bricks costs 3,500 yuan, then the price of a piece of JM23 mullite bricks is 4,500 yuan ÷ 735 pieces = 6.12 yuan. 1.0 A ton of JM28 mullite bricks is 4,200 yuan, so the price of a piece of JM23 mullite bricks is 4,200 yuan ÷ 588 pieces = 7.14 yuan.
Rongsheng Mullite Brick JM28 Factory
Zhengzhou Rongsheng Kiln Refractory Materials Factory is a professional manufacturer of refractory bricks and castables. The company produces refractory products of different specifications, sizes, and standards for different usage environments, and has a professional refractory construction team. The company’s refractory brick products mainly include mullite bricks, high alumina refractory bricks, clay refractory bricks, lightweight insulation bricks, castables, silica bricks, and magnesia bricks. Rongsheng Company has a complete and scientific quality management system and perfect customer service. If you need to purchase insulation material products for your high-temperature industrial furnace project, please contact us.
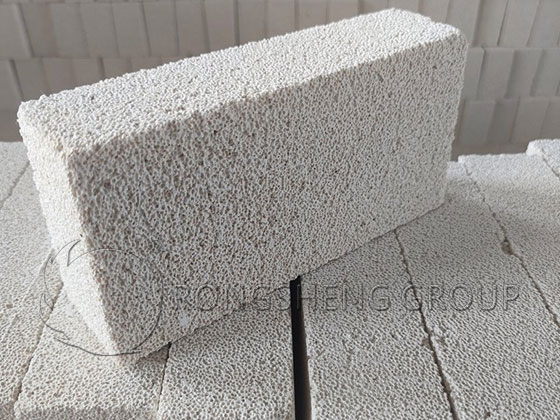
The Difference between Lightweight Mullite Insulation Bricks Jm23/Jm26/Jm28/Jm30
The lightweight mullite insulation bricks Jm23/Jm26/Jm28/Jm30 have different indicators such as alumina content, refractoriness, volume density, and normal temperature compressive strength, which affect the insulation performance and stability. When selecting, physical and chemical indicators need to be considered based on specific needs.
Jm23/Jm26/Jm28/Jm30 in lightweight mullite insulation bricks respectively represent different grades of brick numbers. Different grades of lightweight mullite insulation bricks will have differences in insulation performance, physical and chemical indicators, and scope of use. So what are their differences?
Al2O3 content is different
The alumina content of lightweight mullite insulation bricks Jm23/Jm26/Jm28/Jm30 is 38-44%, 50-58%, 65-70%, and 70-73% respectively. The higher the grade, the higher the alumina content, which affects the thermal insulation performance and fire resistance.
Different refractoriness
The four levels of lightweight mullite bricks have refractory resistances of 1350°C, 1430°C, 1540°C, and 1600°C respectively. The higher the grade, the higher the refractoriness. This is because as the alumina content increases, the refractory degree also increases. The better the stability of lightweight mullite insulation bricks in high-temperature environments.
Different volume density
Among them, the volume density of JM23 is 1.3g/cm3, the volume density of JM26 and JM28 is the same at 0.8g/cm3, and the volume density of JM30 is 1g/cm3.
Different normal temperature compressive strength
The compressive strengths of lightweight mullite insulation bricks Jm23/Jm26/Jm28/Jm30 are 1.3Mpa, 2Mpa, 3Mpa, and 3.5Mpa respectively. The higher the normal temperature compressive strength, the load-bearing capacity and service life of the brick will increase accordingly.
In addition to the above common differences, they have differences in thermal conductivity, reheat line change rate, etc. These indicators reflect the thermal conductivity and stability of the material, and we can choose based on detailed physical and chemical indicators when selecting.
Rongsheng Insulation Bricks Materials for Sales
Proper insulation of the kiln can also save production energy and production costs. Rongsheng manufacturer has many successful cases in kiln insulation. Help enterprises reduce the temperature of the outer wall of the kiln by 50~60℃. Moreover, our new insulation material products have also been tested and will soon be promoted to various industrial kilns. Contact us for free information and quotations on the latest insulation bricks.