Aluminate cement and aluminate refractory castables. aluminate cement (Al2O3 65~70%, CaO 21~24% low iron type). RS Kiln Refractory Manufacturer is a refractory material manufacturer with rich production and sales experience. RS manufacturer is committed to providing high-quality and long-life refractory lining materials for high-temperature industrial furnaces. Contact Rongsheng for a free quote.
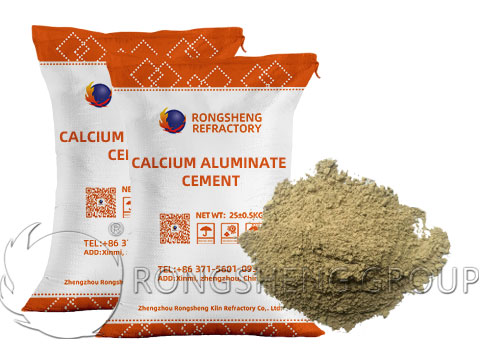
Aluminate Cement
Aluminate cement is a refractory cement, which has many names: refractory cement, 625 cement, high alumina cement, CA-50 cement, etc. It has a wide range of applications. In many refractory concretes, aluminate cement is an indispensable refractory binder.
Aluminate cement is a special cement with weak alkaline calcium aluminate as the main component. It is a hydraulic cementitious material made of bauxite and limestone as raw materials, calcined and made of clinker with calcium aluminate as the main component and about 50% alumina content.
The use temperature of aluminate cement can reach 1350℃. If it is mixed with high-alumina aggregate and other refractory materials in proportion to form a refractory castable, the refractory temperature can reach 1700℃.
Aluminate cement can be divided into CA-50 and CA-70 (also called calcium aluminate cement, white) according to the aluminum content. It is a hydraulic cementitious material with fast hardening, early strength, corrosion resistance and high temperature resistance. Aluminate cement is yellow-brown or gray and is widely used in metallurgy, machinery, building materials, petrochemicals, electricity, food and other industries.
Introduction to the uses of aluminate cement
- Used to prepare refractory castables and kiln linings.
- Suitable for projects that resist sulfate erosion.
- Suitable for concrete projects that require rapid hardening and emergency repair projects.
- Suitable for winter construction and special projects that require early strength.
- Used as raw material for making water purifiers (calcium aluminate powder).
- Used as the best raw material for making decorative materials (such as artificial marble, colored road tiles, colored corrugated tiles, etc.).
- It is an important component for preparing expansive cement, self-stressed cement and other special cements.
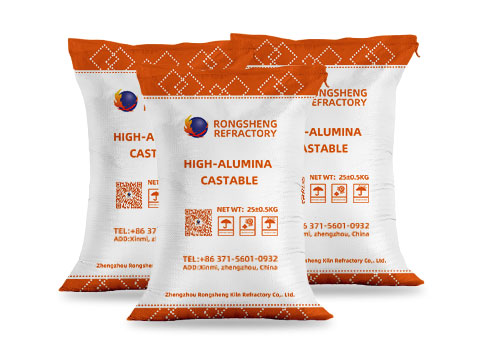
Aluminate Refractory Castables
Aluminate Refractory Castables are an important amorphous refractory material, widely used in industrial kilns such as metallurgy, building materials, petrochemicals, and electric power. It consists of refractory aggregate, powder and binder (such as aluminate cement), which is mixed by adding water or other liquids and has good construction performance and high temperature performance.
Aluminate Refractory Castables Aluminate cement is the key binder in aluminate refractory castables. The type and amount of aluminate cement have a significant effect on the performance of the castable. For example, an increase in the amount of CA-50 cement will increase the compressive strength at room temperature, but the compressive strength will decrease after burning at 1200℃, the refractoriness and load softening temperature will also decrease, and the linear shrinkage after burning will also increase. When preparing aluminate refractory castables, in addition to the amount of cement, the amount of water is also a key factor. An increase in the amount of water will lead to a decrease in performance, so the amount of water in the mixture should be minimized to ensure construction and workability. The selection of refractory powder and aggregate will also have an important impact on the performance of castables. Refractory powder can improve the refractory performance of castables, while the type, grade, maximum particle size and particle grading of aggregates are the main factors affecting the performance.
The use of aluminate castable admixtures is also an important means to improve the performance of aluminate refractory castables. Water reducers can improve the fluidity of castables and reduce water consumption, and coagulants and retarders can adjust the setting time of castables. Sintering agents and expansion agents can improve the medium-temperature strength of castables and compensate for shrinkage at high temperatures.