The low cement castable in the unshaped refractory is a castable with a CaO content of less than 2.5% in the refractory castable combined with calcium aluminate cement. That is to say, the amount of calcium aluminate cement added is about 1/2 to 1/3 of the castable of ordinary calcium aluminate cement. Rongsheng refractory material manufacturer has advanced and fully automatic monolithic refractories material production line. Next, let’s understand the use and advantages of low cement castables, as well as the performance improvement of low cement castables.
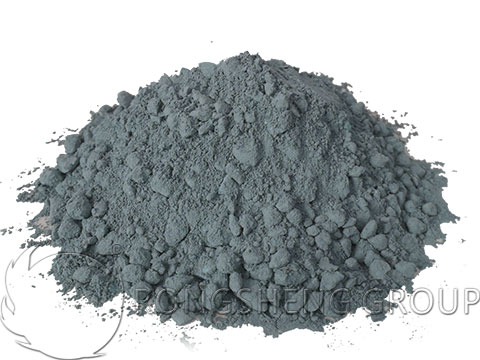
Application of Low Cement Castables
Low cement castables are mainly used in metallurgy, electric power, nonferrous metals, petrochemical, building materials, and other industries. Such as the bottom of the glass kiln, the front end of the front and rear kiln door cover coolers of the cement kiln, and other high-temperature resistant parts, the front, and rear kiln mouths, coal injection pipes, etc. Various heat treatment furnaces such as heating furnace and soaking furnace. Intermediate frequency induction furnace lining, the high-temperature wear-resistant lining of the petrochemical catalytic cracking reactor, lining of other industrial furnaces, etc. The construction methods of on-site pouring, smearing, and ramming can be used.
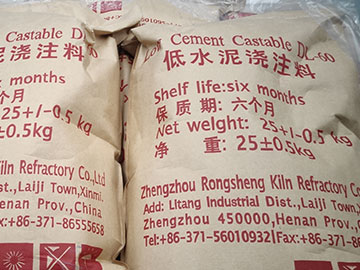
Advantages of Low Cement Castables
Different from traditional refractory castables, the matrix of low-cement castables replaces part or most of the calcium aluminate cement with superfine powder with the same or similar chemical composition as the main material of the castable with a cohesive bonding effect. Therefore, low cement castables are castables that coexist with hydration and cohesion. Due to the use of ultrafine powder (micro powder) to replace part of calcium aluminate cement, low cement castables have the following advantages.
- The low content of CaO in the castable can reduce the formation of the eutectic phase in the material. Thereby improving the refractoriness, high-temperature strength, and slag erosion resistance.
- The mixing water consumption of the castable during construction is only 1/3~1/2 of the ordinary castable, so the porosity is low and the bulk density is high.
- After pouring and molding, less cement is generated during curing. Therefore, there is no damage to a large number of hydration bonds during heating and baking, resulting in a decrease in the medium temperature strength. But as the heat treatment temperature increases, the strength gradually increases.
- With proper adjustment of the strength and composition of the castable, it can be formulated into self-flowing castable and pump castable.
Improve the Performance of Low Cement Castables
Low-cement castables have the advantages of less water addition, high density, good volume stability, and high strength, so they are widely used. However, due to its poor air permeability, it is prone to bursting, peeling, and peeling during baking and ignition. Severely, it even leads to the overall destruction of the construction body, causing serious losses to users. Therefore, how to improve and increase the explosion-proof performance of low-cement castables is of great significance to the practical application and development of low-cement castables. At present, the main method to improve the explosion-proof performance of castables is to add explosion-proof fibers to the castables to increase the permeability of the castables.
Studies have shown that the increase in the amount of explosion-proof fiber has a significant effect on increasing the apparent porosity of low cement castables and improving the explosion-proof performance of low cement castables. The reduction of the content of silicon carbide has an effect on improving the burst resistance of low-cement castables, but the effect is not significant. The increase of the content of silicon carbide has a significant effect on improving the thermal shock stability of the low cement castable heat-treated samples at 1400℃.
To learn more about refractory products, please visit our website: https://kilnrefractory.com/.