The regenerators chamber is a waste heat recovery device that exchanges heat through medium heat storage and heat release. The main structure includes wall, lattice, bottom flue, grate arch-supporting lattice, etc. Therefore, it is also called the regenerator checker chamber. Its internal structure, lattice structure and material are the key factors that affect heat recovery efficiency and process characteristics. Refractories for Regenerators, as it is listed in the following text, will help you understand more.
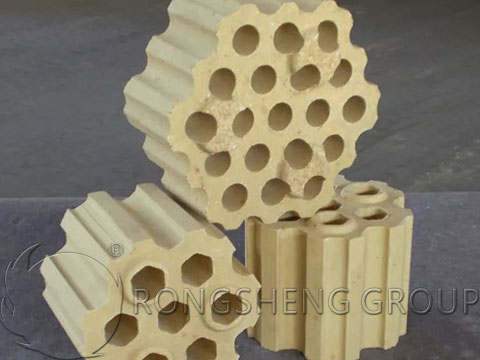
Selection of Checker Bricks for Regenerators of Hot Blast Stoves
The regenerator of the hot blast stove is a space filled with checkered bricks. Its main function is to use the internal checker bricks to participate in the heat exchange between high-temperature smoke and combustion air.
Therefore, the checker brick as heat storage and heat transfer medium should have a larger heat receiving area, higher thermal conductivity and quality to facilitate heat exchange and heat storage. The method of increasing the heating area is to increase the number of holes in the checker brick per unit area. Therefore, the number of holes in the lattice brick of the regenerator tends to increase. Refractories for regenerators.
In order to improve the thermal conductivity of the material, black silicon bricks are commonly used in lattice bricks inside regenerators in Europe. Because the content of iron oxide in the black silica brick is high, the density is large, the thermal conductivity is large, the heat storage capacity is strong, and the heat exchange efficiency is high.
Therefore, the upper part of the regenerator is made of silicon lattice brick. Low creep high alumina brick, mullite brick, sillimanite brick, andalusite brick, etc. are used in the middle of the regenerator. Clay bricks are generally used in the lower part of the regenerator.
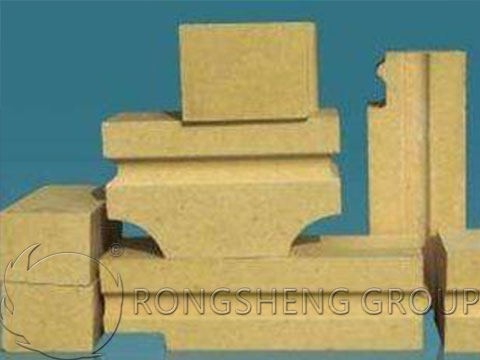
Coke Oven Regenerator
The single vertical wall, partition wall, bottom, and lattice bricks of the small coke oven regenerator can be built with clay bricks. Refractories for regenerators. The large and medium-sized coke oven regenerators are all made of silicon bricks in the upper and middle masonry, so that the whole coke oven can be evenly expanded.
The small flue is located at the bottom of the regenerator and communicates with the flue. The small flue is made of clay bricks.
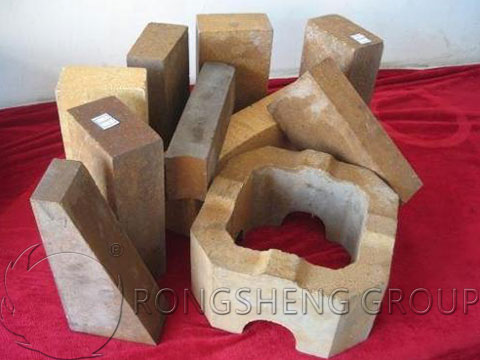
Refractory Material for Glass Kiln Regenerator
At present, there are two main options for the selection of checker bricks used in the regenerators of glass kilns:
(1) Alkaline brick scheme
The lattice bricks on the top layer of the regenerator of this scheme use directly combined high-purity magnesium bricks. The upper layer is made of ordinary fired magnesium brick. The middle layer is made of magnesia chrome brick or forsterite brick which is resistant to sulfate attack. The lower layer uses low porosity clay bricks. The transition material between magnesia brick and clay brick is made of anti-stripping high-alumina brick.
(2) Scheme of fused zirconium brick
The entire lattice body of the regenerator is made of the same cross-shaped fused zirconium corundum lattice brick (ER-1681). According to reports, recently, fused β-alumina material has been selected as the top checker brick.
The top of the regenerator is often made of fused AZS brick, directly combined with magnesium brick or silicon brick. The upper layer of the sidewall and the partition wall is made of magnesia brick, the middle layer is made of magnesia brick or low porosity clay brick, and the lower layer is made of low porosity clay brick. Grate bricks with low porosity are used for the grate.
After choosing a scheme suitable for the kiln regenerator, the quality of its refractory materials, the construction quality of the refractory bricks, and the subsequent oven, maintenance, and daily operations are also the key factors that affect the safe operation of the kiln. Therefore, these steps must be completed in accordance with the design requirements. Avoid economic losses caused by kiln problems.
Rongsheng Refractories for Regenerators Manufacturer
Rongsheng is an experienced manufacturer, who is a professional at refractories. The refractory products of Rongsheng refractory manufacturers have been sold to more than 60 countries and regions around the world. Such as Malaysia, South Africa, India, Indonesia, Pakistan, Netherlands, Kuwait, Kenya, Russia, United States, etc. Rongsheng’s experienced refractory brick production line, as well as the fully automated production line of unshaped refractory castables, are the symbol of Rongsheng’s strength. Rongsheng’s unshaped refractory materials production line, with an annual output of 80,000 tons. If you need to purchase refractories for regenerators, Please contact us or by mail with your specific needs. We will reply to you in the shortest time.