Strictly speaking, the concept of thermal insulation refers to the change of thermal energy of the object of concern (such as equipment, buildings, etc.), while the concept of thermal insulation, heat insulation, or thermal insulation refers to the heat flow or heat transfer of the heat source. Thermal insulation materials refer to materials that can block the transfer of heat flow, also known as thermal insulation materials (but not the same as thermal insulation materials). Thermal insulation materials can be divided into three categories: void heat insulation materials, heat reflective materials, and materials with both void heat insulation and heat reflective properties.
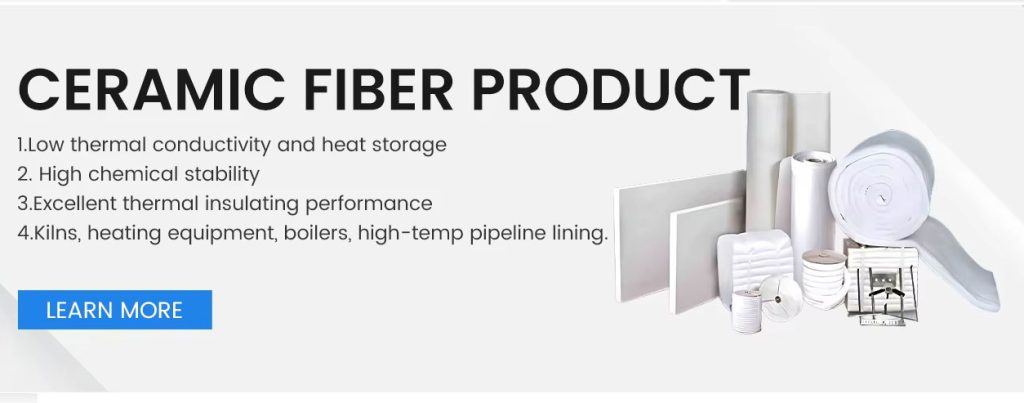
Insulation Materials
Insulation materials are materials or material complexes that are not easy to conduct heat and have significant resistance to heat flow. Their characteristics are: light weight, looseness, porosity, heat preservation, cold preservation, heat insulation, sound absorption, and sound elimination. Generally speaking, insulation materials include the first and third categories of materials mentioned above. Insulation materials can be divided into organic insulation materials (or organic thermal insulation materials) and inorganic insulation materials (or inorganic thermal insulation materials).
In industry idioms, insulation materials often refer to insulation materials suitable for temperatures below 600-700℃. In addition, the industry also refers to insulation materials suitable for low-temperature environments as “cold insulation materials”. Insulation materials suitable for high-temperature environments above 600-800℃ are called “refractory insulation materials“. Insulation materials have lower requirements for thermal conductivity values.
Insulation materials are often referred to as “thermal insulation materials” by people. Here, people do not strictly distinguish the subtle differences between different concepts.
The refractory industry and other industries often use the words “insulation” and “thermal insulation” to refer to lightweight and poorly conductive materials. However, the two are not used consistently and deserve to be reconsidered and unified. In the refractory industry, before the mid-1980s, “insulation materials” and “thermal insulation materials” were used interchangeably. Since then, the term “thermal insulation materials” has been gradually unified, so RS Kiln Refractory Factory will focus on the difference between thermal insulation and heat preservation below.
What is the Difference between Thermal Insulation and Heat Insulation?
-
The concept of thermal insulation board and heat preservation board
Thermal insulation board refers to a board used to isolate heat transfer, generally referring to a board with a thermal conductivity of less than or equal to 0.065W/m•k, such as foam glass, polystyrene board, etc.
Thermal insulation board refers to a reasonable engineering material used to maintain the temperature inside and outside the building. It is usually made of materials with a thermal conductivity of less than or equal to 0.12W/m•k, such as extruded board, mineral wool board, etc.
-
Differences between insulation board and heat preservation board
(1) Material properties
The thermal conductivity of insulation board is lower than that of heat preservation board, and the density of heat preservation board is higher than that of heat preservation board. Heat preservation board is generally a porous material with good air tightness, which can block water vapor penetration to a certain extent, but its bearing capacity for gravity load and wind pressure load is poor. The material used for heat preservation board is relatively hard, with high strength, and can withstand greater pressure.
(2) Application
Thermal insulation board is mainly used for moisture-proof, mildew-proof, anti-corrosion, fire-proof and sound-proof, and is also suitable for roof and wall insulation of industrial buildings and high-end residential buildings. The role of heat preservation board is more to improve the living environment of residential buildings, and is mainly used in the fields of exterior wall insulation, roof insulation, cold storage insulation, etc.
(3) Construction method
Thermal insulation board is mostly constructed by pasting, such as binding with polyurethane foam adhesive. It is generally more convenient to directly paste it with brick wall to achieve insulation. The insulation board needs to be installed by hanging, which is more troublesome, especially in high-rise buildings where construction safety issues need to be considered.
-
Applicable situations
If the building needs to be moisture-proof, mildew-proof, anti-corrosion, fire-proof, sound-proof, etc., it is suitable to use insulation boards. Such as industrial buildings and high-end residences such as pharmaceutical factories, chemical plants, and food factories. If you need to improve the residential living environment, insulation boards are the first choice. It can effectively increase the temperature of the room and keep the indoor temperature stable, thereby reducing energy consumption.