Use refractory plastics or low cement castables in different areas of the heating furnace roof? The temperature of the heating furnace varies greatly from the preheating section, heating section, and soaking section, and each part has different functions. When choosing plastic refractory or low-cement castables, the use performance and price factors must be considered, as well as the convenience of construction and the storage of products.
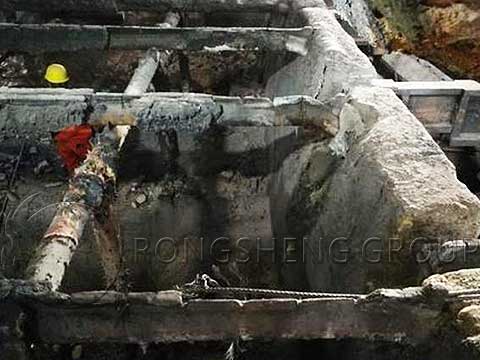
Refractory plastic can not damage its packaging before construction. If the packaging material is damaged, the plastic can lose its plasticity. When storing and keeping the plastic, pay attention to the integrity of the plastic packaging.
If low cement castables are used, anchors must be welded. If the plastic material is fixed on the furnace roof by anchoring bricks, the tightness of the plastic material and the anchoring brick affect the quality of the plastic furnace roof.
Ramming around the anchor is very important when the fire-resistant plastic is constructed. Make wooden molds based on the shape of anchor bricks. When the plastic is rammed, a wooden mold is used to mold the plastic around the anchor bricks, and then the anchor bricks are inlaid in the mold. Pram around the anchor brick with the wind to make it come in close contact with the plastic. But be careful not to smash the anchor brick.
But plastic is more shrinking. After removing the mold, use an expansion joint knife to cut a 30-50mm expansion suture on the surface with an interval of about 1.5m, which means that the plastic surface is cut into 1.5m square blocks. But if the plastic shrinks, it will only crack in the opened expansion joint, and no cracks or cracks will appear.
If low cement castables are used, 20 anchors per square must be welded. Support the mold first, then pour the low-cement castable, take off the film after 24 hours, and then grill according to the barbecue system.
In short, whether fire-resistant plastic or low-cement castable is used, depends on the situation. If there is no condition to store plastics, low cement castables can be used. If the construction of low cement castables is inconvenient, refractory plastics can also be used.
How Long is the Setting Time of the Refractory Plastic?
Refractory plastic is an amorphous material that can maintain good plasticity for a long time. Next, we come to understand some characteristics of the refractory plastic from the setting time of the refractory plastic.
The refractory plastic can be in the form of a mud paste, or it can be separated from the powder and the binder. If you are in a hurry for construction or repair, it can be made into a mud paste. If the construction time is long, the powder and the binder can be packaged separately, so that they can be mixed and used during pre-construction.
The plasticity of the plastic has a great influence on the bonding strength and volume stability of its hardened body. It is the properties of clay that control the properties of refractory plastics. The plasticity is related to the properties and dosage of the clay, which increases with the increase of the binding dosage. If the binding dosage is too high, the fire resistance and plasticity are not strong, and it is best to control it at 5%-10% so that the plasticity of the plastics will not decrease during the shelf life. The binding agent is a special glue preparation.
The refractory plastic can be taken out from a sealed container during construction, or a special bonding agent can be added on-site to trap the material. The trapping time cannot be less than 10 hours. Then lay it between the hanging bricks or anchoring bricks and tamping with a hammer. In particular, the plastic can be processed into any shape before being hardened.
Refractory plastic In order to facilitate the drainage of water, holes should be punched at regular intervals. Expansion joints should also be set according to the design. If the part to be constructed is integral, first construct on the bottom form and then hoist it after drying.
The setting time of refractory plastic is 1-3 hours for the initial setting and 6-8 hours for the middle setting. It can reach 60-80% strength after one day of curing, 85%-95% of the strength is reached after 3 days of curing, and it can be used after 7 days of final strength.
Unshaped Refractory Material Sales
Rongsheng refractories production and sales factory have advanced and fully automatic monolithic refractory production lines. The annual output is 80,000 tons. Our unshaped refractory products mainly include various refractory castables, ramming mass materials, refractory plastics, low cement castables, wear-resistant refractory castables, etc. We can customize the formula of unshaped refractory materials according to the specific needs of customers. Our monolithic refractory products have a high rate of return orders from our monolithic refractory customers. Customers’ trust in us stems from our strict control of product quality. And we are committed to providing customers with high-quality customer service. To purchase high-quality unshaped refractory products, please contact us. We will provide you with the most suitable products for your project production needs according to your specific construction needs.