Cement kiln burning system consumes a lot of energy. Do this: The thermal insulation performance is 4-6 times that of ordinary products, reducing heat loss! RS Kiln Refractory Company has rich experience in energy conservation and thermal insulation of cement rotary kilns, saving production costs for enterprises.
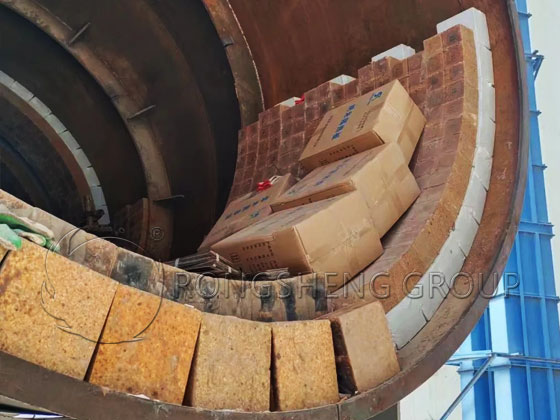
Insulation of Cement Kiln Firing System
The energy consumption of cement kiln firing system is relatively large, and traditional insulation materials can no longer meet the needs of thermal insulation and energy saving of firing system. In order to reduce heat loss and increase thermal efficiency, high-performance insulation materials must be set in the lining design to reduce the temperature of the cylinder and reduce heat loss.
Nano insulation board is a new type of thermal insulation material made of silica particles with a diameter of tens of nanometers, infrared reflective materials and fibers, etc., through a series of processes. It contains a large number of nano-scale micropores, which makes it have excellent thermal insulation effect. Nano insulation board is also called nano insulation board, nano insulation board, low-dimensional nano insulation board, nano composite insulation board, nano microporous insulation board, etc. It is suitable for preheater, decomposition furnace, flue gas chamber, grate cooler, tertiary air duct, kiln head cover and other parts.
Product Features of Nano Thermal Insulation Board
- Low thermal conductivity and good stability, the thermal conductivity changes very little with the increase of temperature.
- Dust-free construction, convenient for on-site processing and cutting.
- The strength increases with the increase of temperature, and it will not powder after long-term use.
- Non-toxic and environmentally friendly.
Working principle of nano thermal insulation board
- Prevent the thermal motion of gas molecules and reduce heat conduction
According to the theory of molecular thermal motion, the transfer of gas heat is mainly through the collision of molecules with higher speed on the high temperature side and molecules with lower speed on the low temperature side, and heat is transported step by step. Nano thermal insulation board uses nano-scale particle structure to increase the heat propagation path and establish a series of barriers in the direction of temperature gradient, and make the barrier distance less than the mean free path of gas molecules. Moreover, the barrier is a pore that is closed and close to vacuum state, which will effectively prevent the thermal motion of gas molecules.
- Reflection of thermal radiation
Nano thermal insulation board adds nanomaterials that can reflect thermal radiation, which can more effectively reduce the thermal conductivity of the product and is an excellent thermal insulation material.
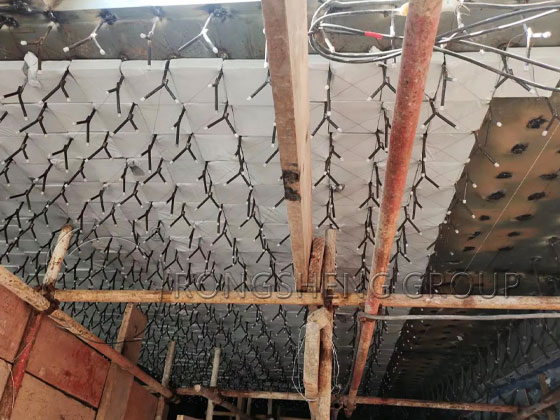
Importance of Cement Kiln Insulation
- Reduce energy consumption: Cement kilns generate a lot of heat during operation. If the insulation effect is not good, a lot of heat will be lost to the outside, resulting in energy waste. Good insulation can reduce heat loss, improve energy efficiency, and reduce production costs.
- Protect equipment: Cement kiln cylinders and other equipment are easily affected by thermal stress in high temperature environments, leading to deformation, cracking and other problems. Insulation materials can reduce the surface temperature of equipment, reduce thermal stress, and extend the service life of equipment.
- Improve the working environment: Effective insulation can reduce the temperature of the surrounding environment of the cement kiln, provide operators with a more comfortable working environment, and reduce the impact of high temperature on personnel health.
The company’s manufacturers have introduced and absorbed advanced technologies from home and abroad, independently developed production equipment suitable for domestic use, and truly realized the practical application of nano-microporous thermal insulation materials. The production equipment and process draw on mature foreign technologies, with high production efficiency and stable product quality. It can produce a full range of standard products of nano-thermal insulation materials with an annual output of 10,000 cubic meters. The thermal insulation performance of the product is 4 to 6 times that of ordinary thermal insulation materials. It is the best-performing new nano-material that can be used on a large scale for thermal insulation of high-temperature kilns.
According to successful application cases, micro-nano thermal insulation boards are used on stationary equipment at the end of cement kilns due to their excellent thermal insulation performance. Under the same thermal insulation thickness, the effect of significantly reducing the shell temperature by 20 to 30°C can be achieved, which can save more than 30% of heat dissipation losses.
When the firing system needs to expand its volume, a 25 mm micro-nano thermal insulation board can replace a 100 to 115 mm calcium silicate board to achieve the effect of expanding the net space of the equipment by 75 to 90 mm. Keep the surface temperature of the high-temperature equipment unchanged, the original energy consumption does not increase, and the output of the equipment is greatly increased.
The use of 15 mm micro-nano insulation board in the transition zone and preheating zone of the rotary kiln can reduce the shell temperature of the rotary kiln by 70-100°C, reduce the heat dissipation loss by more than 42%, and achieve significant energy-saving effects. If the entire rotary kiln is insulated with nano-insulation materials, in addition to significantly reducing the shell temperature of the rotary kiln, the ellipticity deformation of the rotary kiln shell can also be greatly reduced, which is beneficial to extend the service life of the refractory materials. At the same time, it can significantly reduce the amount of coal used at the kiln head, reduce the amount of nitrogen oxides generated at high temperatures in the rotary kiln, and thus reduce the amount of ammonia water used for denitrification, which has a positive environmental protection effect.
In summary, the excellent thermal insulation performance of micro-nano insulation materials provides a new thermal insulation material for energy saving and consumption reduction, capacity expansion and production increase, and green environmental protection transformation in the cement industry, and makes a beneficial contribution to the technological progress of the cement industry.