What is the material of sintered corundum brick? Sintered corundum bricks are refractory products made of sintered dense alumina clinker. The brick has the characteristics of a high melting point, stable performance at high temperatures, good mechanical strength, and wear resistance. Sintered corundum bricks have excellent resistance to metal corrosion, oxidation, and reduction. 99 high aluminum content sintered corundum bricks, zirconium corundum bricks, high refractoriness, used in chemical solid waste incinerators. The raw material for making sintered corundum bricks is calcined and finely ground high-purity industrial alumina, and sometimes a small amount of MgO additive is added to improve the crystal structure. Sintered corundum brick for glass furnaces – RS kiln refractory brick manufacturer.

90 Alumina High-Strength Sintered Corundum Refractory Brick
Corundum brick 90 alumina, high-strength sintered corundum refractory brick, stable performance at high temperatures. Re-sintering fused corundum bricks, the manufacturing process includes pressing the raw materials into green bodies, and then calcination at a high temperature above 1850 °C. Calcination reduces the porosity in the green body structure, increases the crystal grains by about 25-40 times, and forms a dense plate-like structure. When making bricks, the sintered corundum with a porosity of less than 3% and a bulk density greater than 3.60g/cm3 is crushed to the required particle size. The main chemical components of sintered corundum bricks include Al2O3, SiO2, Fe2O3, CaO, MgO, Na2O, etc. The physical and chemical properties of sintered corundum bricks include purity, refractoriness, apparent porosity, bulk density, compressive strength, creep rate, load softening temperature, etc. The production process involves crushing sintered corundum into coarse particles and fine powder. A small amount of clay or other binders are added for kneading, shaped by a high-pressure friction brick press or hydraulic press, and then dried and fired. Sintered corundum bricks are widely used in blast furnaces and refining furnaces in the metallurgical industry, as well as in chemical, electronic, and other industrial fields.
Corundum Sintered Refractory Bricks, High-Purity Low-Silicon Corundum Bricks, Source Manufacturers
Sintered corundum brick has stable performance at high temperatures, and high melting points, and the normal temperature compressive strength of corundum brick can reach 340MPa. The load softening start temperature is greater than 1700°C. It has strong resistance to acidic or alkaline slag, metal, and glass liquid. Corundum sintered refractory bricks, high-purity low-silicon corundum bricks, Rongsheng manufacturers, direct delivery.
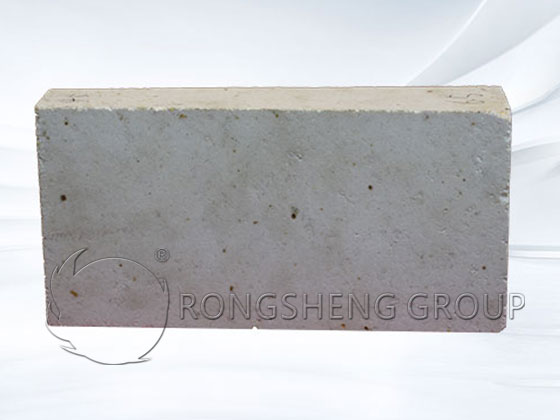
Sintered corundum bricks are fired at high temperatures in a shuttle kiln. It has the characteristics of high refractoriness, good thermal shock stability, high-temperature strength, strong slag resistance, small expansion coefficient, low creep, and spalling resistance. The thermal shock stability of corundum bricks is related to their structure, good corrosion resistance, but poor thermal shock stability. The bulk density is greater than 3.60g/cm3, and the porosity is less than 3%.
Sintered corundum bricks are high-grade refractory materials, suitable for use in high-temperature kilns under various atmospheric conditions. High-quality high-purity corundum bricks are widely used in high-temperature sintering of zirconia ceramics, fluorescent materials, electronic ceramics, magnetic materials, ceramic powders, and gasifiers in the petrochemical industry. Synthetic ammonia secondary conversion furnace, carbon black reaction furnace and glass industry high-temperature kiln, and other equipment. The dimensions, physical and chemical indicators, and service life of the products have met the requirements of high-temperature furnaces.
The production process of sintered corundum bricks is to crush sintered corundum to 3mm coarse particles and some fine powders less than 0.074mm in height. Some add a small amount of clay and other binders for mixing and shape them with a high-pressure friction brick press or hydraulic press. The adobe is fired in a high-temperature chamber after being dried. Generally, the sintered corundum brick with higher purity has a firing temperature of 1750-1800°C.
Sintered corundum bricks have good high-temperature resistance, good corrosion resistance, and thermal shock stability. Rongsheng sintered corundum bricks are mainly used in blast furnaces and refining furnaces outside the metallurgical industry. It is also used in ironmaking blast furnaces and blast furnace hot blast stoves, refining furnaces outside steelmaking furnaces, sliding nozzles, glass melting furnaces, and petrochemical industrial furnaces. Now on the market, the proportion used in glass melting furnaces is more.
Sintered Corundum Bricks Have High Compressive Strength and Corrosion Resistance
Sintered corundum bricks refer to corundum refractory products with an alumina content greater than 90% and made from sintered alumina clinker. Refractory bricks, sintered corundum bricks, corundum bricks, high compressive strength, and corrosion resistance. Gas-bonded corundum brick has a high melting point and stable performance at high temperatures. It has good mechanical strength and wear resistance at room temperature and high temperature, and has excellent resistance to metal corrosion and redox.
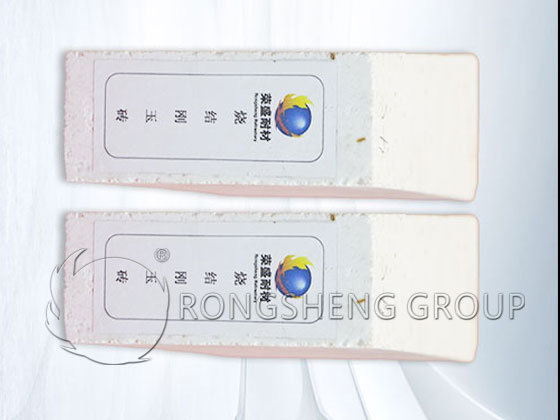
The production process of sintered corundum bricks is to crush sintered corundum to 3mm coarse particles and some fine powders smaller than 0.074mm. Some add a small amount of clay and other binders for mixing. It is shaped by a high-pressure friction brick press or hydraulic press, and the adobe is fired in a high-temperature chamber after drying. Generally, the sintered corundum brick with higher purity has a firing temperature of 1750-1800°C. If a small amount of clay or additives is added, the firing temperature can be 1600~1700°C.
Sintered corundum bricks have been widely used as lining materials in petrochemical thermal equipment with high temperatures, high pressure, severe chemical erosion, and mechanical wear. With the advancement of production technology in the petrochemical industry, many new processes and technologies have been adopted in production, in order to make the equipment achieve the purpose of large load, long cycle, low energy consumption, and low cost. In addition to the transformation of various thermal equipment, higher requirements are also put forward for the lining materials of various thermal equipment.
However, the raw materials of corundum bricks are all high-end products, and the price of sintered corundum bricks is also a high-end product among refractory products. Therefore, the price will naturally be much higher than ordinary refractory materials.