Zirconium silicate refers to ultra-fine powder produced by zircon sand through an ultra-fine grinding process. It was initially called “zircon sand ultrafine powder”, and “Ultrafine Zirconium Silicate Powder”, and later gradually became standardized as “zirconium silicate”. This name has become widely accepted and used.
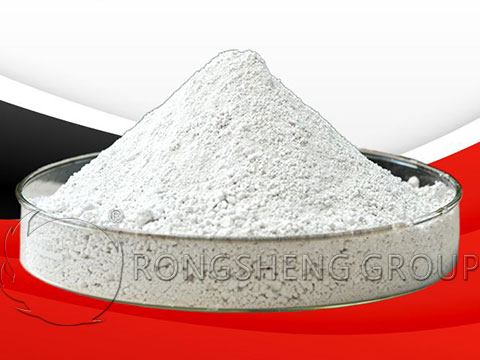
Application and Production of Ultrafine Zirconium Silicate Powder
The initial application of zirconium silicate Powder was mainly used on the glaze of daily ceramics and building sanitary ceramics. It is an opacifying agent for making ceramic milky white glaze and the main additive for the raw milky white glaze. Prior to this, the opacifying agents used in ceramic opalescent glazes were mainly tin oxide, zirconium dioxide, and opalescent frit made of zircon powder. Since the first two were very expensive at the time, using zircon powder to make high-temperature frit consumed a lot of fuel and the cost was also high. Zircon is refractory to high temperatures and difficult to decompose. It is difficult to melt and then crystallize in the glaze. Therefore, in order to take advantage of the high refractive index of zircon and produce a good opacification (milky white) effect, zircon sand must be processed into an ultra-fine particle state. Theoretically, it is below 1μm. However, zircon sand has a very high hardness (Mohs hardness 7.6), second only to silicon carbide. Therefore, in order to process zircon sand to about 1μm, ultra-fine processing technology has become a topic of research. The gradual solution and development of this issue is the development history and development trend of zirconium silicate production technology.
With the improvement of materials and rapid expansion of the scale of China’s architectural ceramic tiles, zirconium silicate began to be used in the body of building bricks. The application scope of zirconium silicate has been further expanded, resulting in a rapid increase in the demand for zirconium silicate, driving the rapid development of the zirconium silicate Powder industry. Zirconium silicate has played a decisive role in the zirconium series products and has formed a zirconium silicate industry circle.
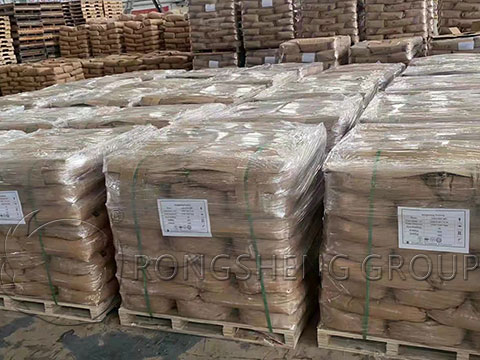
High Purity and Ultrafine is the Future Trend of Zirconium Silicate
Zirconium silicate Powder is mainly developed in two aspects. First, further ultra-fine development in the direction of high-purity zirconium silicate. The second is to develop and apply composite zirconium silicate.
There are two main reasons. First, zircon sand raw materials are becoming increasingly scarce, and all countries are paying attention to the protection and utilization of resources. In 2010, my country listed zirconium as one of the rare metal elements as strategic reserves and control. More rational and full use of this resource has become a trend. Second, the increase in price has increased the acceptance of the downstream application market. Take Australian zircon sand as an example. In 1993, the price of Australian zircon sand was US$200/ton, and now it is US$2,600/ton. In 18 years, the price of Australian zircon sand has increased 13 times.
Therefore, how to make zirconium silicate Powder better and more refined, and improve the use effect and added value of zirconium silicate. This has become an issue that zirconium silicate production enterprises must consider, and it is also one of the next development trends of zirconium silicate. On the other hand, how to combine zirconium silicate with other low-value materials and maintain the effectiveness of zirconium silicate. It is also a problem that the zirconium silicate industry needs to study and solve, and it is another development trend of the zirconium silicate industry.
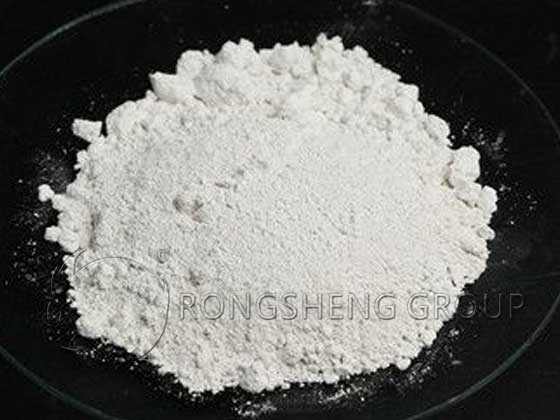
Ultrafine Zirconium Silicate
Ultra-fine zirconium silicate is an extra-fine zirconium silicate Powder produced under strict process and laboratory quality control conditions and is recommended for use in high-quality enamelware.
Ultra-fine zirconium silicate Powder strictly controls the quality from the source of production and is produced from zircon sand imported from Australia. Used as an opacifying agent in various types of ceramic glazes. It can also be used in the plastics industry and the refractory materials industry.
The company currently produces more than 50,000 tons of zircon sand and zircon powder, more than 20,000 tons of zirconium silicate powder, and more than 1,000 tons of zirconium oxide powder annually. The business scope covers the production, processing, and sales of more than 40 specifications of products in 6 categories, including zircon sand, zircon powder, zirconium silicate powder, zirconium oxide powder, zirconium oxide beads, and zirconium silicate beads.
Application of Ultrafine Zirconium Silicate
Zirconium silicate powder (molecular formula: ZrSiO4), ultra-fine zirconium silicate powder is a high-quality and low-cost opacifying agent for ceramic glazes. Mainly used in building ceramics, sanitary ceramics, daily ceramics, etc. As a ceramic glaze, zirconium silicate can improve the opacification effect and hardness of the glaze during production, and can also be used as a ceramic body to increase the whiteness. Theoretically, the highest refractive index of zirconium silicate is 1.93-2.01. The finer the fineness, the better the opacification effect and the more delicate the glaze.
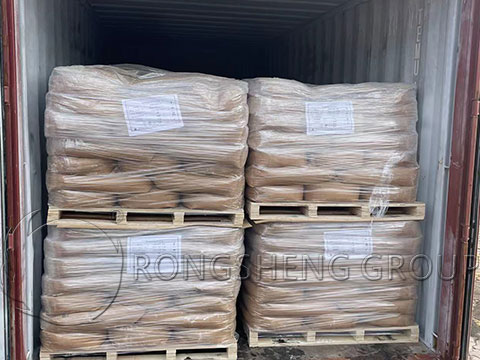
Zirconium Silicate Powder Uses
(1) Used as an opacifying agent for various types of ceramic glazes.
Export coffee cups; sanitary ceramics; wall and floor tiles; ceramic tiles and building tiles; stoneware vessels; tableware; special porcelain.
(2) Plastic
Used in epoxy resin formulations, sealing resins, fillers for silicones, vinyls, and resins to increase heat resistance and improve resistance insulation value. For fillers that require inert, fine, white color and resistance to chemical effects.
Cast zirconium refractories are used in glass-melting furnaces. Heat-resistant porcelain; sandblasting for refractory castings. Sandblasting of refractory boards; special refractory porcelain; and refractory cement.
Recommended concentration for use
For white enamel with high opacification and brightness, 12%-20% is generally used. In glaze processing, 4%-8% is generally used.
Leave Your Requirements on RS Kiln Refractory Bricks And Castable Materials! We Will Reply You In 12 Hours!: