Alumina bricks are usually divided into three categories:
Class I: Al2O3 content ≥75%;
Class II: Al2O3 content 60%~75%;
Class III: Al2O3 content is 48%~60%.
Alumina bricks can also be classified according to their mineral composition. Generally divided into five types: low mullite (sillimanite), mullite, mullite-corundum, corundum-mullite, and corundum. High alumina bricks, fireclay bricks, mullite bricks, corundum bricks, alumina bubble bricks, etc., are all alumina bricks. Their main original composition is alumina. Rongsheng is one refractory manufacturer with rich experience. Freely get the prices. Next, we will learn about several kinds of alumina bricks.
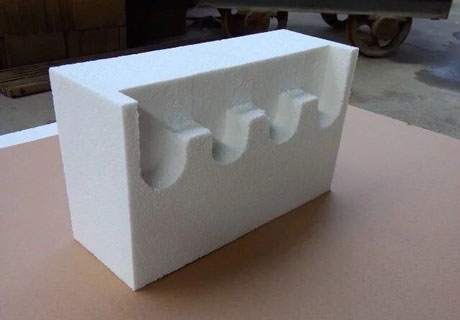
Alumina Bubble Bricks
Alumina bubble brick is a kind of high-temperature insulation material widely used. It has good high-temperature resistance and thermal insulation and plays a role in heat preservation and heat insulation in high-temperature kilns. Rongsheng alumina bubble brick is a heat-insulating refractory product made of alumina hollow ball as the main raw material. It is mainly used as the lining of high-temperature industrial kilns below 1800℃ and the thermal insulation layer of high-temperature thermal equipment.
The aluminum content of Alumina bubble bricks is not less than 98%, the content of SiO2 is not more than 0.5%, and the content of Fe2O3 is not more than 0.2%. The bulk density is 1.3~1.4g/cm3. The apparent porosity is 60~70%. The compressive strength is not less than 9.8MPa, and the load (0.2MPa) softening temperature is not less than 1700℃. The thermal conductivity is 0.7~0.8W/(m.k).
However, the main mineral phase composition of the alumina hollow sphere aggregate and matrix are both the corundum phase. The large thermal expansion coefficient makes the Alumina bubble bricks have poor thermal shock resistance. The high-temperature kiln cracked and peeled off, and the service life was greatly reduced. Especially the use of intermittent kilns greatly affects the life span.
The main advantage of Alumina bubble bricks is high-temperature energy saving (>30%). It is widely used in the inverted flame kiln, shuttle kiln, molybdenum wire furnace, tungsten rod furnace, induction furnace, nitriding furnace, etc. Obvious effects will be achieved for reducing the weight of the furnace body, transforming the structure, saving materials, and saving energy. Especially in the petrochemical industry gasifier, carbon black industrial reaction furnace, metallurgical industry induction furnace, and other high-temperature and ultra-high temperature furnaces are widely used. A very satisfactory energy-saving effect has been achieved.
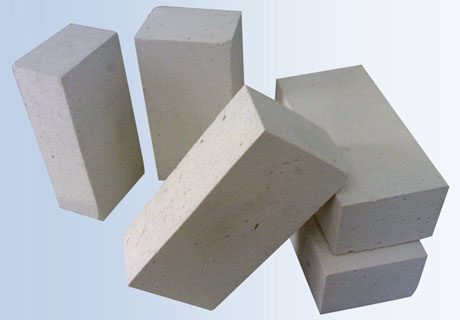
Mullite Bricks
Mullite bricks refer to high alumina refractory materials with mullite as the main crystal phase. Generally, the alumina content is between 65% and 75%. In addition to mullite, the mineral composition with lower alumina also contains a small amount of glass phase and cristobalite; the higher alumina content also contains a small amount of corundum. Mainly used for hot blast stovetop, blast furnace body and bottom, regenerator of glass melting furnace, ceramic sintering kiln, dead corner lining of petroleum cracking system, etc.
Mullite bricks have high refractoriness, which can reach above 1790℃. The starting temperature of load softening is 1600~1700℃. Compressive strength at room temperature is 70~260MPa. Good thermal shock resistance. There are two types of sintered mullite bricks and fused mullite bricks.
Sintered mullite bricks use high alumina bauxite clinker as the main raw material. It is made by adding a small amount of clay or raw bauxite as a binder, forming and firing.
Fused mullite bricks use high alumina bauxite, industrial alumina, and refractory clay as raw materials. Charcoal or coke fine particles are added as a reducing agent, and it is manufactured by reducing electric melting after molding. The crystallization of fused mullite is larger than that of sintered mullite, and its thermal shock resistance is better than that of sintered products. Their high-temperature performance mainly depends on the content of alumina and the uniformity of the mullite phase and glass distribution.

Corundum Mullite Bricks
Corundum mullite bricks are mainly made of corundum and mullite. It is made by adding an appropriate amount of alumina, silica ultrafine powder and additives, and firing at high temperature in an oxidizing atmosphere. The content of AL2O3 is 72%~90%. Corundum mullite bricks can be directly exposed to flame, peel off, and high temperature. It can be used as the thermal insulation lining of high-temperature industrial furnaces and the working layer of other industrial high-temperature furnaces. Mainly used in the petrochemical industry, large and medium-sized synthetic ammonia gasifier and magnetic material gas furnace materials, high-temperature industrial furnace supporting facilities materials.
Advantages of corundum mullite bricks.
-
- (1) High-temperature resistance. High refractory temperature and high load softening temperature.
- (2) Chemical resistance. Strong resistance to acidic solutions or molten slag.
- (3) Anti-oxidation. It is not easy to react with O2, H2, CO, and other gases.
- (4) Good thermal stability, stable volume at high temperature, not easy to expand or shrink.
- (5) Good thermal shock resistance, resistance to rapid cold and heat, and not easy to peel off.
- (6) High compressive strength at room temperature and it is not easy to wear when handling or unloading.
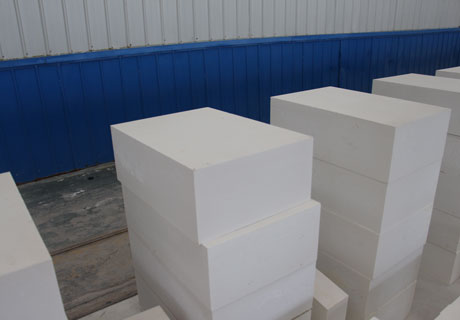
Corundum Brick
Corundum brick refers to a refractory product with alumina content greater than 90% and α-Al2O3 (corundum) as the main crystal phase. High compressive strength at room temperature, up to 340MPa. The high load softening start temperature is greater than 1700°C. Very good chemical stability, strong resistance to acidic or alkaline slag, metal, and glass liquid.
Use of corundum bricks
-
- Corundum porous vent plugs are used for refining outside the furnace, such as VAD/VOD furnaces. Argon can be blown continuously for 60 to 90 minutes, the temperature of molten steel is 1700 to 1800 ℃, the service life is 1 to 4 times, and the average corrosion rate is 8 to 13 mm/heat.
- The second-stage reformer of petrochemical synthetic ammonia adopts low-silicon corundum bricks. It can be used all year round under high temperature, high pressure and strong reducing atmosphere above 1700℃.
- The use of large corundum bricks in the discharge chute of the high-temperature kiln in the glass industry can extend the life.
- Firing zone in high-temperature tunnel kiln or in an inverted flame kiln. Shuttle kilns can use corundum bricks with Al2O3>95% or more as lining or combustion chamber lining.
Rongsheng Alumina Brick Manufacturer
Rongsheng is an experienced refractory brick manufacturer. Rongsheng’s refractory products have been sold to more than 60 countries and regions all over the world. Our refractory brick products have been well received by customers in the following countries. Buy a variety of refractory brick products for your thermal furnace equipment. Or go to the latest alumina brick quotation, please contact us, or leave your specific needs on our website page. Our products and services will satisfy you.
Leave Your Requirements on RS Kiln Refractory Bricks And Castable Materials! We Will Reply You In 12 Hours!: