Silicon Carbide Ceramic Description
Silicon carbide ceramic not only has excellent mechanical properties at room temperatures, such as high flexural strength, excellent oxidation resistance, good corrosion resistance, high wear resistance, and low friction coefficient. And high-temperature mechanical properties, such as strength, creep resistance, etc., are also the best-known refractory ceramic materials.
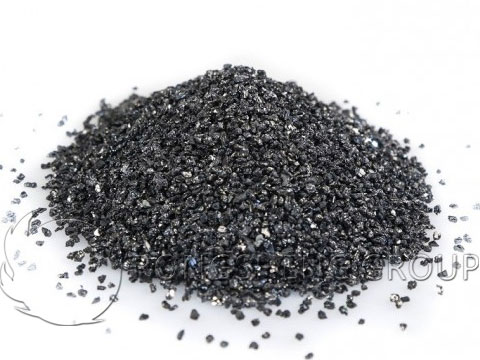
The initial application of SiC is that due to its superhard properties, it can be prepared into various grinding wheels, abrasive cloths, sandpapers, and various abrasives, so it is widely used in the machining industry. In World War II, it was found that it can also be used as a reducing agent and heating element in steelmaking, thus promoting the rapid development of SiC. Silicon carbide ceramic has been widely used in petroleum, chemical, microelectronics, automobile, aerospace, aviation, papermaking, laser, mining, atomic energy, and other industrial fields. At present, silicon carbide has been widely used in high-temperature bearings, bulletproof plates, nozzles, high-temperature corrosion-resistant parts, and electronic equipment parts in the high-temperature and high-frequency range.
Wide Application of Silicon Carbide Ceramic
Silicon carbide ceramic has four main application areas. Namely, functional ceramics, advanced refractories, abrasives, and metallurgical raw materials.
- (1) As an abrasive, it can be used as an abrasive tool. Such as grinding wheels, whetstones, grinding heads, sand tiles, etc.
- (2) as metallurgical deoxidizer and high-temperature resistant material.
- (3) High-purity single crystals can be used to manufacture semiconductors and silicon carbide fibers.
Specifically, silicon carbide ceramics are used in chemical, refractory, metallurgy, steel, ceramics, and other fields.
In the chemical industry. Silicon carbide can be used as a deoxidizer for steelmaking and a modifier for cast-iron structure. It can also be used as a raw material for the manufacture of silicon tetrachloride and is the main raw material for the silicone resin industry. Silicon carbide deoxidizer is a new type of strong composite deoxidizer, which replaces the traditional silicon powder carbon powder for deoxidation. Compared with the original process, the physical and chemical properties are more stable and the deoxidation effect is good. The deoxidation time is shortened, energy is saved, steelmaking efficiency is improved, and steel quality is improved. Reduce the consumption of raw and auxiliary materials, reduce environmental pollution, improve working conditions, and improve the comprehensive economic benefits of the electric furnace.
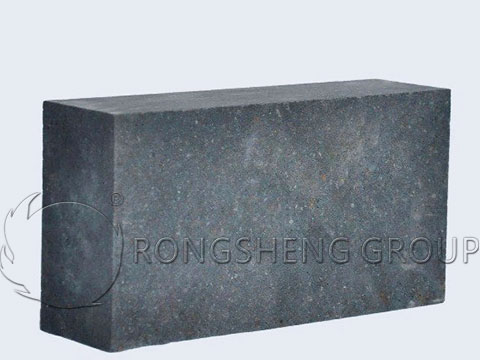
In the refractory industry, the use of silicon carbide has the characteristics of corrosion resistance, high-temperature resistance, high strength, good thermal conductivity, and impact resistance. On the one hand, silicon carbide can be used in various smelting furnace linings, high-temperature furnace components, silicon carbide plates, silicon carbide lining plates, supports, saggars, silicon carbide crucible, silicon carbide tiles, etc. In the iron and steel industry, the use of silicon carbide’s characteristics of corrosion resistance, thermal shock resistance, wear resistance, and good thermal conductivity is used for the lining of large blast furnaces to improve the service life.
On the other hand, it can be used for high-temperature indirect heating materials in the non-ferrous metal smelting industry. Such as vertical tank distillation furnace, rectification furnace tray, aluminum electrolytic cell, copper melting furnace lining, arc plate for zinc powder furnace, thermocouple protection tube, etc. It is used to make high-grade silicon carbide ceramic materials such as wear resistance, corrosion resistance, and high-temperature resistance. It can also be used to make rocket nozzles, gas turbine blades, etc.
Metallurgical beneficiation. The hardness of silicon carbide is second only to diamond, and it has strong wear resistance. It is an ideal material for wear-resistant pipes, impellers, pump chambers, cyclones, and hopper linings. Its wear resistance is 5-20 times the service life of cast iron and rubber.
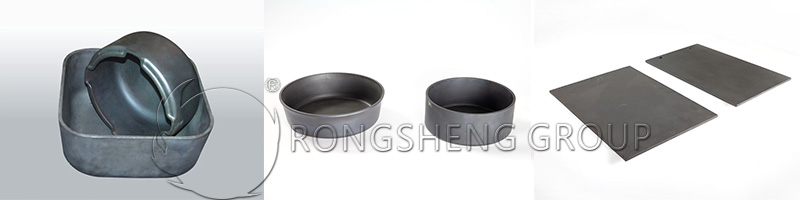
In the ceramic industry, thin-plate kiln furniture is manufactured by utilizing its characteristics of thermal conductivity, thermal radiation, and high thermal strength. Not only can the capacity of kiln furniture be reduced, but also the capacity and product quality of the kiln can be improved. It shortens the production cycle and is an ideal indirect material for ceramic glaze baking and sintering.
In addition, silicon carbide is also one of the ideal materials for solar water heaters for highways and aviation runways.
Sintering Process for Preparing Silicon Carbide Ceramic
At present, the methods for preparing high-density SiC ceramics mainly include pressureless sintering, hot pressing sintering, hot isostatic pressing sintering, and reaction sintering.
- Through the pressureless sintering process, SiC parts with complex shapes and large dimensions can be fabricated. Therefore, it is considered to be the most promising sintering method for the preparation of SiC ceramics.
- With the hot-pressing sintering process, only simple-shaped SiC parts can be produced, and the number of products produced in one hot-sintering process is small. Therefore, it is not conducive to commercial production.
- Although the hot isostatic pressing process can obtain complex-shaped SiC products, the green body must be encapsulated. Therefore, it is difficult to achieve industrial production.
- SiC parts with complex shapes can be prepared by the reaction sintering process, and the sintering temperature is relatively low. However, the high-temperature performance of reaction sintered SiC ceramics is poor.
Table 1 presents some properties of SiC ceramics in pressureless sintering, hot pressing sintering, hot isostatic pressing sintering, and reaction sintering.
Table 1 Performance Comparison of Silicon Carbide Ceramics Prepared by Different Sintering Methods
Performance Index Sintering process |
Pressureless Sintering | Hot Pressing Sintering | Hot Isostatic Pressing Process | Reaction Sintering Process | |
Flexural Strength (MPa) | 20℃ | 410 | 640 | 640 | 380 |
1400℃ | 410 | 650 | 610 | 300 | |
Thermal Conductivity Rate (W/ m*K) | 20℃ | 110 | 130 | 220 | 140 |
1400℃ | 45 | 45 | 50 | 50 | |
Weibull Modulus | 7 ~ 10 | 0 ~ 10 | 11 ~ 14 | 10 ~ 12 | |
Elastic Modulus (GPa) | 410 | 450 | 450 | 350 | |
Bulk Density (g/cm3) | 3.12 | 3.21 | 3.21 | 3.05 |
Obviously, the properties of SiC ceramics vary depending on the sintering method. Generally speaking, the comprehensive properties of pressureless sintered silicon carbide are better than those of reaction sintered SiC, but inferior to those of hot pressing sintered and hot isostatic pressing sintered silicon carbide.
To Buy Silicon Carbide Ceramic Products, Please Contact Us
The company’s silicon carbide ceramic products include silicon carbide tubes (coal injection tubes for power plants), silicon carbide saggers, silicon carbide shed plates, silicon carbide bricks, wear-resistant, and corrosion-resistant impellers, wear-resistant seals, etc. Widely used in electric power, electric porcelain, direct reduced iron, vanadium and titanium, mineral processing, metallurgical industries, etc. The products are sold well in China and exported to Germany, the United States, South Korea, Japan, Turkey, Thailand, Indonesia, Vietnam, India, Spain, Australia, the Middle East, and other countries and regions. To buy beryllium oxide ceramic, silicon carbide ceramic, silicon carbide crucible, silicon carbide tube, sintered silicon carbide, and silicon carbide refractory, please contact us.
Leave Your Requirements on RS Kiln Refractory Bricks And Castable Materials! We Will Reply You In 12 Hours!: