I recently read an article about the refractory lining structure of the “refractory castable + magnesia brick” structure. It feels very interesting and I want to share it with everyone. The suspension cylinder of the Maerz lime kiln has a “refractory castable + magnesia brick” structure, which plays an important role in the normal production of the lime kiln. In the construction process, the method of pre-baking after the completion of the refractory castable construction, and then the magnesia brick masonry method can effectively avoid the hydration damage of the free water in the castable to the magnesia brick.
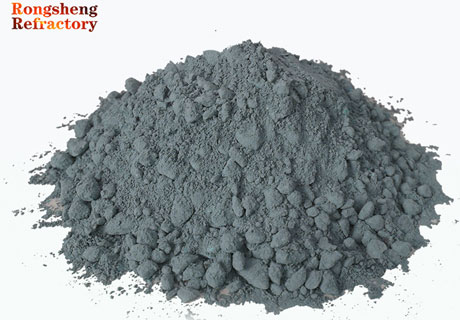
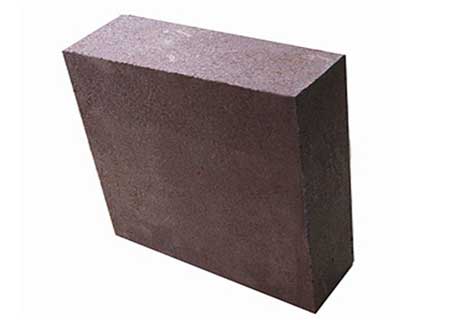
In the structure of Maerz kiln lime kiln, the most important part is the suspension cylinder. The amount of refractory material occupied by the suspension cylinder is not large, but it is the top priority of control in the entire Maerz lime kiln construction. It directly restricts the production process of the lime kiln and also determines the production life cycle of the lime kiln.
Structural Characteristics of Suspension Cylinder
The suspension cylinder structure is a castable + magnesia brick structure. During the production process of the lime kiln, the suspension cylinder is subject to frequent impacts of limestone and is easily damaged. The construction process of this part: first carry out the construction of the refractory castable, and then build the magnesia brick on the upper surface of the castable. The structure of the suspension cylinder is shown in Figure 2 and Figure 3.
Water is used for stirring during the construction of the castable, and the structure contains a large amount of free water. In the later drying process, the free water evaporates and combines with the magnesia bricks to hydrate the magnesia bricks. The magnesia bricks are cracked and the strength is reduced, making this part the most vulnerable part of the lime kiln. Frequent maintenance is required to ensure the normal production of the lime kiln. In order to avoid such a situation, the free water in the castable must be evaporated before the magnesia brick is built. Only in this way can it be ensured that the hydration damage of the magnesia bricks caused by moisture can be reduced in the later drying process, so as to better meet the production requirements.
Construction Technology of Refractory Lining of Suspension Cylinder
According to the structural characteristics of the suspension cylinder, the overall idea of the construction process is to consider making a set of devices to pre-bak the castable. The purpose is to evaporate the free water in the castable before the magnesia brick construction, so as to ensure that the magnesia brick does not produce hydration during the later drying process.
Implementation steps
The pre-baking is carried out after the construction of the castable is completed and after a certain period of curing. The main implementation steps include the production of the baking furnace, the setting of the sensors, the access to the PLC control system, and the baking.
Production of baking furnace
- 1) Use 30mm×3mm flat steel to make the frame of the baking furnace. The production of the frame should also consider the support of the insulation brick at the bottom. The space formed after the frame is made is 500mm×372mm, and the materials used in the production are given priority to on-site materials.
- 2) Put 6 diatomite insulation bricks of 230mm×114mm×64mm in each flat steel frame. After the insulation bricks are put in, slot them as required, and reserve wiring holes. The above materials should also be considered on-site.
- 3) Place the purchased resistance wire in the diatomite insulation brick tank. The power of each resistance wire is generally 2.5~3kW, and 2 resistance wires are placed in each oven.
The production of the baking furnace is shown in Figure 5.
Sensor settings
Make and set up the mold according to the design size of the design drawing. Carry out the construction of the castable according to the specification. And according to the 90° division, 4 internal temperature sensors are set on each suspension cylinder, as shown in Figure 7, to detect the temperature inside the suspension cylinder pouring material during baking. After removing the mold, place the baking furnace under the castable. The surface of the baking furnace is about 250mm away from the surface of the castable. After it is placed steadily and the circuit is connected, the castable is sealed with heat insulation material. And set a temperature sensor at the middle channel from the outside of each suspension cylinder to measure the external temperature, as shown in Figure 7. By detecting the temperature inside and outside the castable, the temperature difference between inside and outside can be controlled.
The heat insulation measures during baking are shown in Figure 6, and the sensor layout is shown in Figure 7.
Connect to PLC automatic control system and bake
After the circuit is connected, it is connected to the PLC automatic control system, and the temperature control program is input. The two resistance wires can be energized alternately or simultaneously to complete the entire baking process as required. After baking, remove the heat insulation material used for sealing, dismantle the circuit, remove the baking oven, clean the upper magnesia bricks.
The oven curve can be determined according to the thickness and type of refractory material. Figure 8 is the oven curve of LCC low cement castable.
Conclusion
The pre-baked construction method can effectively remove a large amount of free water in the castable during the construction process. It avoids the hydration of the magnesia bricks in the later drying process, improves the structural strength, and prolongs the service life of the lime kiln lining.
The construction process of the construction method is simple, and the overall construction quality of the suspension cylinder is greatly improved. Improve the efficiency of the entire production process and reduce the frequency of maintenance. From the perspective of long-term effects, large long-term benefits can be obtained at a relatively small cost, which creates benefits for the entire production process and wins competitiveness.
For more information about refractory materials for kiln refractory linings, please contact us. We will provide you with services according to your specific needs.
Leave Your Requirements on RS Kiln Refractory Bricks And Castable Materials! We Will Reply You In 12 Hours!: