For the application characteristics of any product, it is necessary to analyze and explain the structural characteristics of the product itself. Therefore, in order to distinguish the application of Monolithic Refractories and Shaped Refractories, it is also necessary to understand the structural performance characteristics of the materials. Rongsheng kiln refractory material manufacturer is an experienced refractory material manufacturer. Rongsheng’s advanced automatic unshaped refractory production line has an annual output of 80,000 tons. To purchase high-quality unshaped refractory products, please send us an email. We will provide you with services according to your specific needs.
The Difference in Refractory Materials’ Structure
By choosing the best production and construction technology, it is possible to obtain similar densities regardless of whether it is monolithic refractories or fired refractory products. However, the difference between the two lies in their structure. For refractory castables, the focus is on controlling the rheology of the mixture, which is why the particle size distribution must be finely controlled, and ultrafine powders or even nanoparticles are used. The microporous structure of amorphous refractories is the most typical. In dense fired bricks, the typical pore size is 20-25μm, and some special products can reach 5μm. In castables, even after firing, the median diameter of the pores usually does not exceed 1~2μm. The comparison of the pore size distribution of two typical refractory castables and refractory bricks (clay and high alumina) is shown in Figure 1.
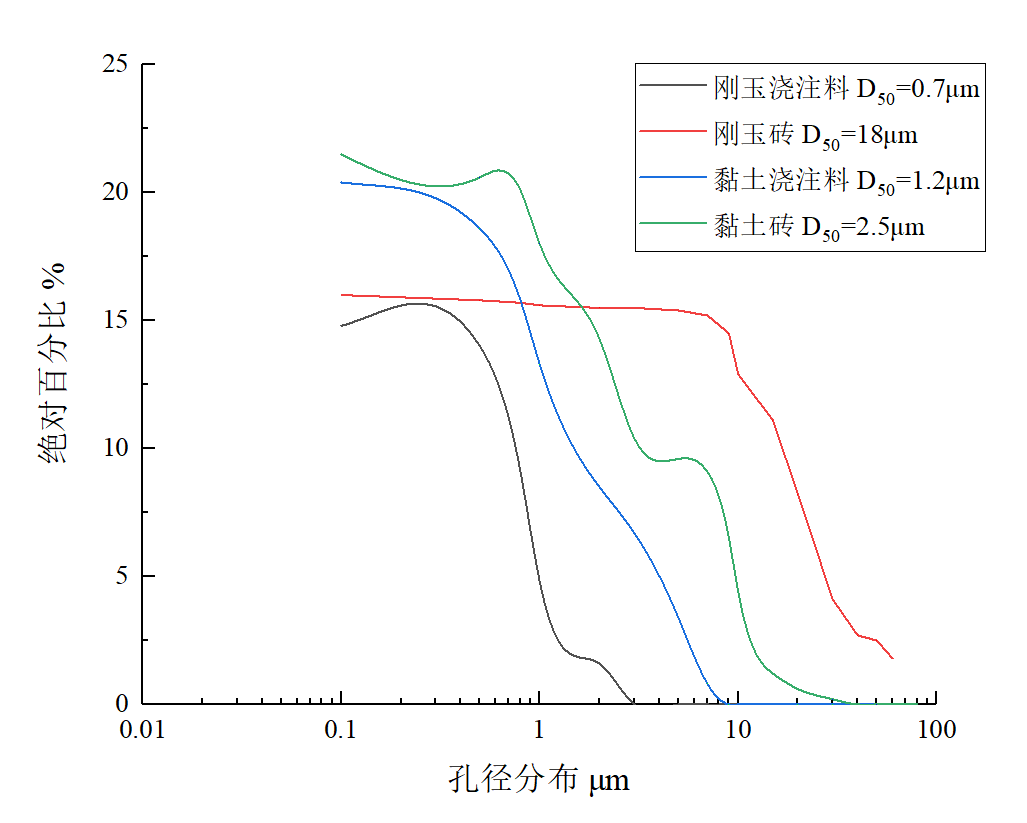
These structural differences are reflected in other properties. The microporous structure can significantly increase the strength of the material and improve thermal shock stability. This has been demonstrated by the increased resistance of the material to cracks that form and propagate during sudden temperature changes.
The microporous structure also leads to a decrease in the heat radiation of the material at high temperatures. Compared with fired refractory products with similar composition and pores, the thermal conductivity of the castable is reduced by 20% to 30%. as shown in picture 2.
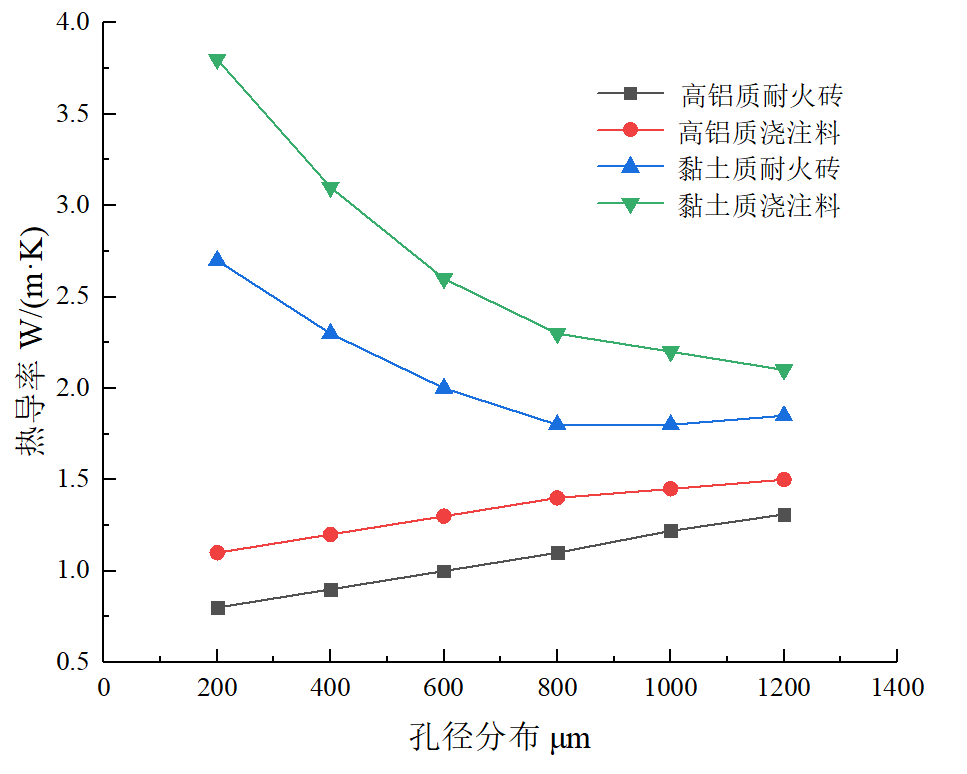
The microporous structure of the castable helps hinder the penetration of the slag into the material in the corrosive environment. Improve the corrosion resistance of the material against molten materials, especially slag and metals.
Unlike fired products, castables have good plasticity, that is, the refractory lining can release stress through its own deformation without being damaged. In this regard, phosphate-bound castables are particularly prominent (Figure 3).
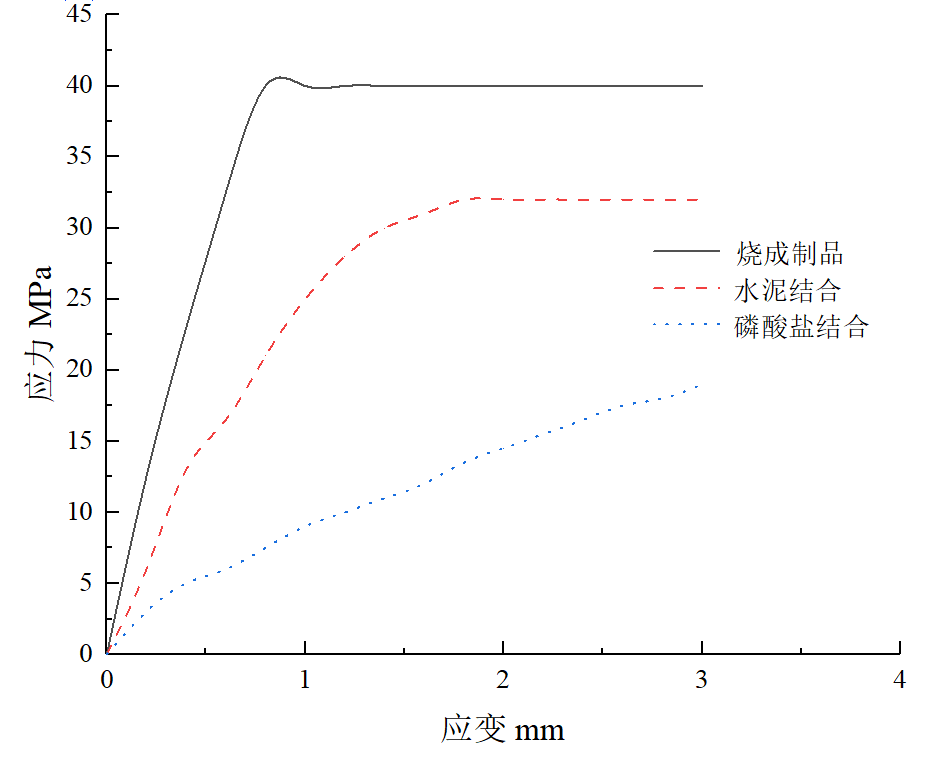
There are some problems when using monolithic refractory linings, and these problems may not occur if shaped products are used.
Application comparison of unshaped refractory materials and shaped products
Recently, monolithic refractory materials are not only used to manufacture new monolithic refractory linings but are also widely used for repairing and maintaining refractory linings in service. There are many construction methods for monolithic refractories, and some construction methods have become and will continue to be the main construction methods for monolithic refractories. According to traditional methods, monolithic refractories are used as the bottom of the traditional electric arc furnace (alkaline refractory), gun mud, blast furnace tapping channel, and some repair and maintenance materials. In some cases, products with complex shapes have been replaced by unshaped refractory materials, resulting in composite linings. A garbage incinerator is an example.
In shaped products, for some negative properties of magnesia bricks, such as high thermal expansion rate and poor slag corrosion resistance, carbon is added to the composition. The effective addition of carbon in magnesia castables has not been reasonably determined, which is a factor restricting the wide and successful use of MgO-C castables.
However, with the development of high-performance low-cement and ultra-low-cement castables, amorphous linings have gained an increasingly important position in the ladle. High-aluminum castables and lining replacement technology have become a widely used technology. After the newly built ladle has been in service once, the inner surface of the lining can be removed by mechanization, and a new layer of castable can be poured on the damaged surface. This procedure can be repeated many times. Compared with the original new masonry lining technology, the consumption of ladle materials for the implementation of the lining replacement technology is 40%-50%, which means that this technology can save 50%-60% of the furnace lining material.
Compared with brick lining, the advantages of monolithic refractories as the lining can be summarized as follows: reduce the labor and time of masonry, and increase the utilization rate of the ladle. As the number of ladles in service is reduced, the consumption and cost of refractory materials are reduced.
Unshaped refractories play an important role in the maintenance of kilns. This is because large-scale repairs can be achieved in the shortest downtime, and in some cases even during operation. System repair to the lining can extend the life of the kiln. The repair of the alkaline lining (MgO-C brick) of the oxygen blowing converter is an example. Using alkaline mixtures for regular injection, while accurately controlling the generation of slag, slag splashing can increase the life of the lining to more than 20,000 heats, and the consumption of refractory materials per ton of steel can be reduced to less than 1kg.
In summary,
When choosing to use a monolithic refractory lining or traditional brick lining, the advantages brought by the rapid construction of monolithic refractories (using new binders) and the shortened drying and heating time will play an important role. In many cases, because raw materials have a huge impact on product performance, raw materials account for the largest part of the final product price (up to 60%). From this point of view, because raw materials occupy a major position in monolithic refractories, the use of monolithic refractories will bring undisputed economic benefits. Therefore, the continuous improvement of the quality of monolithic refractories and the rapid and simplification of construction will ultimately make the use more economical.
Matters needing attention in the use of unshaped refractory castables
- It must be considered that the manufacturer supplies monolithic refractories (such as dry materials) in the form of semi-finished products, and must be processed at the construction site to form monolithic refractory linings. If the manufacturer’s instructions are not strictly followed during the mixing process, such as wetting the material or using the correct construction procedures, certain problems will occur.
- In the construction process of monolithic refractories, it is important to consider longer heating and drying times and to use a high enough temperature to fully dehydrate the binder.
- When using traditional castables combined with hydration, it must be taken into account that the strength decreases at moderate temperatures. In the middle-temperature range (250~600℃), the hydration bond will gradually decompose because the ceramic bond has not yet formed. Similarly, since the matrix shrinks at high temperatures, it is expected that the castable has good volume stability.