The design principle of Al2O3-MgO refractory castable is a high-performance refractory castable obtained by introducing MgO into all-alumina refractory castable and corundum refractory castable. Al2O3-MgO refractory castable has the characteristics of large residual expansion, high corrosion resistance and permeability resistance, and good creep. And as the amount of fine MgO powder added increases, the corrosion resistance of refractory castables increases. When the MgO fine powder content is 5-10%, the slag penetration is the smallest.
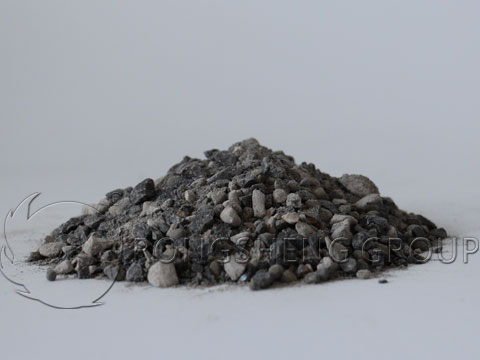
Ways of Introducing MgO into Corundum Refractory Castables
- ① Directly introduce pre-synthesized Al2O3·MgO.
- ②Introduce high-purity magnesia fine powder, and form Spinel through the reaction of f-Al2O3 and f-MgO in the matrix at high temperature.
- ③Introduce pre-synthesized Spinel+ high-purity magnesia fine powder.
Through the use of active fillers (α-Al2O3, SiO2, Cr2O3, etc.), the structure of the Al2O3-MgO refractory castable is more compact. As the internal particle contact rate is increased, the amount of cement can be reduced to zero as much as possible. Then use high-efficiency dispersant to fluidize the particles, so that the requirements of construction and pouring can be met even when the amount of water added is low.
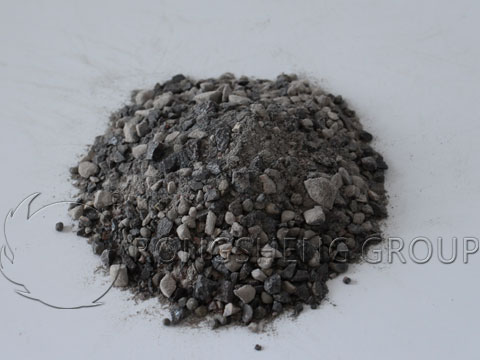
Application and Common Damage of Alumina-magnesia Refractory Castable
The steel industry mostly uses high-alumina and alumina-magnesia-carbon refractory bricks. Due to the need for multi-furnace continuous casting and clean steel, the capacity of the ladle continues to expand, and there are more and more types of molten steel. In order to adapt to the increasingly harsh smelting conditions, alumina-magnesia refractory castables have been developed. And now the scope of application is also expanded to RH refining furnaces, cement kilns, and other high-temperature equipment.
Common causes of damage to alumina-magnesia refractory castables during use are as follows. The linear expansion rate is large, and cracks occur during use, resulting in a decrease in strength and slag penetration. Poor thermal shock resistance, cracks will occur on the surface or inside of the cast material under the conditions of rapid cold and rapid heat, which will accelerate the erosion of slag and cause material damage.
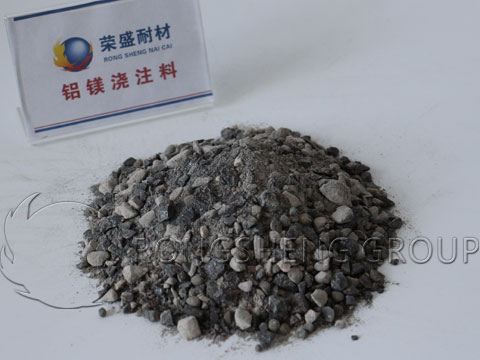
Influence of Adding Corundum Powder to Alumina-Magnesia Refractory Castable
The slag retaining wall of the tundish is eroded by molten slag during operation and is damaged by the intermittent thermal shock caused by molten steel soaking, molten steel scouring, and rapid cold and heat, which is prone to cracking, spalling, molten slag penetration, and collapse. Therefore, castables are required to have excellent slag resistance, thermal shock resistance, and good strength. The quality of the matrix in the main material determines the structure, strength, slag resistance, thermal shock resistance, and other properties of the material. White corundum powder has a high melting point, good chemical stability, and good thermal shock stability, so it is widely used in alumina-magnesia systems and alumina-based castables. However, in the actual production process, when white corundum powder is used in these two systems, abnormal conditions such as high water addition, poor fluidity, fast hardening time, and poor strength often occur. As a result, the castable cannot be constructed, the slag retaining wall breaks when it is demoulded, and the service life is drastically reduced. So what is the effect of adding white corundum powder to the alumina-magnesia refractory castable?
Through the experimental analysis of refractory manufacturers, the following conclusions are made on the effect of adding corundum powder to alumina-magnesia refractory castables.
- (1) The pH value and ignition loss content of white corundum powder have a great influence on the castable. When the pH value is between 6.5 and 7.5 neutral and the ignition loss content is less than 0.15% (w), the sample adds less water, has good fluidity, and the bulk density is higher, and the strength at room temperature and high temperature will increase accordingly. On the contrary, when the pH value is less than 6.5, and the ignition loss content is greater than 0.15% (w), the physical properties of the castable are very poor.
- (2) The higher the ignition loss content, the higher the C content. It also means that the higher the Al4C3 impurity content.
- (3) With the increase of the slurry expansion, it shows that the Al4C3 impurities in the white corundum powder increase, and the performance of the castable show an obvious downward trend. Experiments show that when the expansion of the sample is less than 20%, the castable has less water added, good fluidity, and all physical indicators are the best. When the expansion of the sample is greater than 20%, the amount of water added to the castable will increase, the flow value will decrease significantly, and the volume density and strength will drop sharply.
- (4) With the increase of Al4C3 impurities in the white corundum powder, the slag resistance and penetration resistance of the sample decreased significantly, the heat loss became worse, the residual compressive strength gradually decreased, and the thermal shock performance also gradually decreased.
Tips: A patented formula for alumina-magnesia castables
An alumina-magnesia refractory castable and preparation thereof. The composition raw materials of the alumina-magnesia refractory castable are proportioned by weight percentage: corundum particles and fine powder are 70-80%, and alumina fine powder is 5-15%. 2~10% of magnesia-containing materials, 3~8% of binder, 0.3~1.5% of silicon powder. Organic fiber (extra) 0.05~0.1%, water reducing agent (extra) 0.2~0.6%. The preparation of the material includes the steps of compounding, mixing, forming, curing, drying, and the like. It can be used for the wall, bottom, permanent layer, nozzle, and other parts of the large ladle. It can also be used for RH dip tube castable.
Leave Your Requirements on RS Kiln Refractory Bricks And Castable Materials! We Will Reply You In 12 Hours!: