Product performance of anti-stripping high alumina bricks. It has the characteristics of strong high-temperature volume stability, excellent thermal shock resistance, wear resistance, and chemical corrosion resistance. It is mainly used in the transition zone of cement rotary kilns, calciner, tertiary air ducts, and thermal equipment requiring thermal shock resistance. Rongsheng kiln refractory brick manufacturer, as a powerful manufacturer of anti-stripping high-alumina bricks for cement kilns, can provide high-quality high-alumina refractory brick products and technical support for cement kilns.
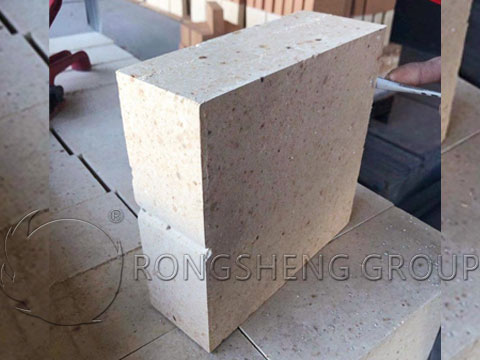
Why do cement kilns use anti-stripping high alumina bricks?
As the basic material in the refractory industry, high alumina bricks have the characteristics of high refractoriness, relatively high softening temperature under load (about 1500°C), and good erosion resistance. It has been widely used in industrial kilns in various industries. However, due to the high corundum phase content of ordinary high alumina bricks. The corundum phase crystallization in the sintered product is relatively large, and it is prone to cracking and peeling when it encounters rapid cooling and rapid heating. The number of thermal shock stability under 1100°C water cooling condition can only reach 2-4 times at most. In the cement production system, high alumina bricks can only be used in the transition zone of the rotary kiln, the kiln tail and the calciner preheater due to the limitation of the sintering temperature and the performance requirements for the refractory material to stick to the kiln skin.
In the cement rotary kiln, the gas containing sulfur, chlorine and alkali components is discharged to the kiln tail along with the flue gas. After the sulfur, chloride and alkali components in the flue gas are condensed at the kiln tail, they are brought into the firing zone along with the materials. The sulfur-chlor-alkali components just circulate and precipitate in the transition zone area, forming an alkali cycle, causing the chlor-alkali components in the transition zone to exceed the standard. These chlor-alkali components will cause very serious erosion of refractory materials. The chlor-alkali components with low melting point penetrate into the refractory bricks, condense and deposit in the lower temperature part of the refractory bricks, and fill the pores of the refractory bricks, causing the refractory bricks to be dense and deteriorated. Since the thermal expansion coefficient of the metamorphic layer of refractory bricks is inconsistent with that of normal refractory bricks, structural spalling and damage will occur when encountering rapid cooling and rapid heating. Therefore, the erosion of chlor-alkali components and poor thermal shock stability are the main reasons for the damage of refractory bricks in the transition zone area. The high-alumina brick has a high porosity. When it is used at the kiln tail, the alkali salt in the flue gas will penetrate into the interior of the high-alumina brick after condensation at the kiln tail, making the internal structure of the hot end of the high-alumina brick dense. In the event of rapid cooling and rapid heating, layered peeling will occur, and the thickness of the peeling can reach 40-100mm, resulting in final damage to the refractory brick. Under these conditions, anti-stripping high alumina bricks came into being.
Anti-stripping high-alumina bricks are high-alumina bricks with anti-stripping properties produced based on high-alumina clinker and added with ZrO2 or other materials. Can be divided into two categories. One is the anti-stripping high-alumina brick containing ZrO2, represented by GKBL-70, and the other is the anti-stripping high-alumina brick without ZrO2, represented by KBL-70.
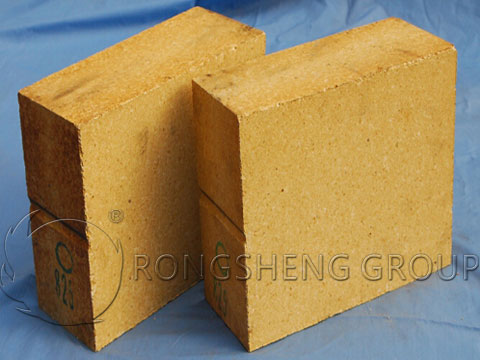
Product features of anti-stripping high alumina bricks of Rongsheng refractory brick manufacturers
Anti-flaking high-alumina bricks can resist the high-temperature thermal load. The volume does not shrink and has a uniform expansion, no creep, and collapse, and has a relatively high normal temperature strength and high-temperature thermal strength. High load softening temperature. It has good thermal shock resistance and can resist the influence of rapid temperature changes or uneven heating. No cracking, no peeling. The difference between the anti-stripping high-alumina bricks containing ZrO2 and the anti-stripping high-alumina bricks without ZrO2 lies in their different anti-stripping mechanisms. ZrO2-containing anti-stripping high-alumina bricks use ZrO2 with excellent corrosion resistance to resist the erosion of sulfur, chloride, and alkali by adding zircon materials. At the same time, at high temperatures, SiO2 contained in zircon will undergo crystal phase transformation, from cristobalite to α-quartz phase, resulting in a certain volume expansion effect. Thereby, while reducing the erosion effect of preventing sulfochlor-alkali, it can prevent spalling in the process of cold and heat. Anti-stripping high alumina bricks without ZrO2 are produced by adding andalusite on the basis of high alumina bricks. The irreversible micro-expansion effect produced by the andalusite in the product during the secondary mullitization in the cement kiln prevents the product from shrinking when it is cooled, offsets the shrinkage stress, and does not cause structural spalling.
Compared with the anti-stripping high-alumina bricks without ZrO2, the anti-stripping high-alumina bricks containing ZrO2 have better penetration and erosion resistance of sulfur, chlorine, and alkali components, so the anti-stripping performance is better. However, since ZrO2 is a rare material, the zircon used in my country’s refractory industry mainly relies on imports from Australia and South Africa, which is expensive, so the cost and price are relatively high. The anti-stripping high-alumina bricks containing ZrO2 are only used in the transition zone of the cement rotary kiln, and the anti-stripping high-alumina bricks without ZrO2 are mostly used in the calciner of the cement production line.
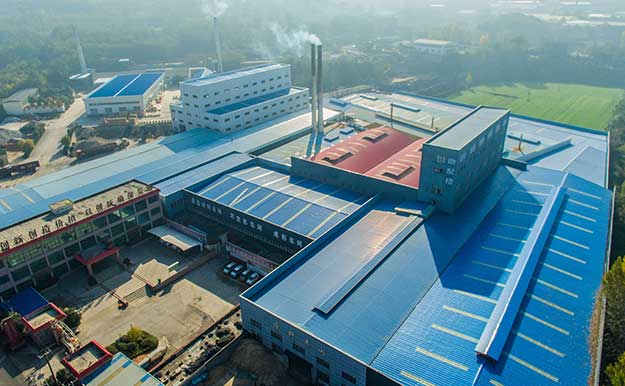
Rongsheng refractory brick manufacturer
Rongsheng refractory brick manufacturer is a powerful refractory brick manufacturer. Our refractory brick products are widely used in metallurgy, nonferrous metals, building materials, electric power, petrochemical, and other industries. For example, high-alumina bricks for blast furnaces and hot blast stoves, phosphate-bonded high-alumina bricks for cement kilns, and anti-stripping high-alumina bricks. Silica bricks for glass kiln and coke oven. Clay-based refractory bricks, alkali-resistant bricks for cement kilns, and low-porosity clay bricks. Magnesia brick, magnesia chrome brick, magnesia alumina brick. Silicon carbide mullite bricks for cement kiln. High-alumina, silicon-based heat-insulating refractory bricks, etc. Contact us for free pricing information and technical support.
Leave Your Requirements on RS Kiln Refractory Bricks And Castable Materials! We Will Reply You In 12 Hours!: