When self-baking carbon bricks were first used, they were used in small and medium-sized submerged arc furnaces and calcium carbide furnaces. As the application technology matures, it is gradually used in large-scale submerged arc furnaces. The raw materials of self-baked carbon bricks are roughly the same as those of pre-baked carbon bricks. Add binders and additives such as coal tar pitch in a certain proportion, knead evenly at a certain temperature, and then extrude it. The formed carbon bricks can be used to build the furnace bottom and furnace lining without pre-firing. The gap between the carbon bricks is within 1mm, which is much smaller than the gap between the carbon bricks when the furnace is built by the pre-baked carbon brick process. The gaps between the carbon bricks and the carbon bricks and between the carbon bricks and the furnace wall are filled with low-temperature joint paste.
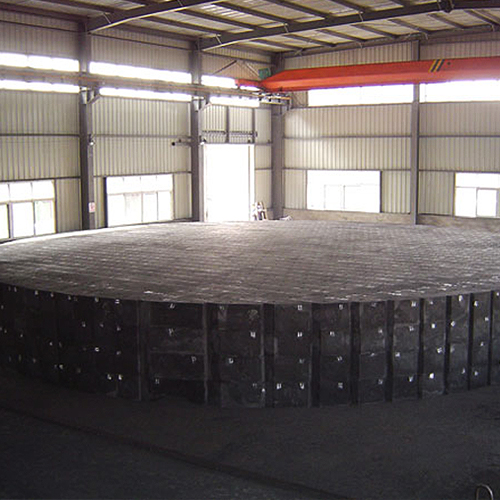
The roasting of self-baking carbon bricks is different from that of pre-baked carbon bricks. The materials of self-baking carbon bricks and seam paste are similar, and they start baking at the same time under the same conditions. Therefore, the plastic deformation of the carbon bricks during the firing process can make up for the gaps in the furnace body, and eventually graphitize gradually. A dense and integrated carbon lining is formed, and the transformation from carbon to graphite is completed with the increase in temperature.
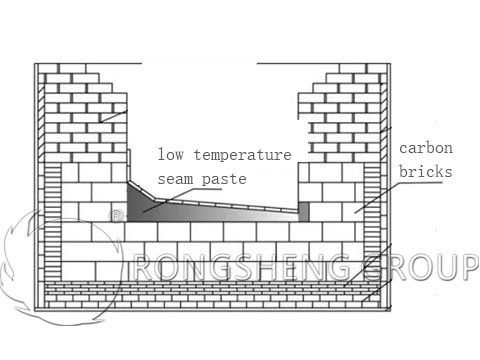
In view of the large gap between the carbon bricks when the pre-baked carbon bricks are built, it is easy to cause the seam paste to shrink and crack during baking, and the molten metal is poured into the furnace, which causes the furnace to break through. In order to improve the overall structure of the furnace lining and reduce the penetration of molten metal. When the self-baking carbon bricks are built, the gap between the carbon bricks is small, and the graphite furnace body formed after baking has better integrity and compact structure. The molten metal is difficult to penetrate, and the corrosion resistance is improved, which can significantly improve the service life of the submerged arc furnace. Moreover, after the self-baking carbon brick is graphitized, the electrical conductivity is improved, the current of the main circuit is increased, the harmful branch circuit is reduced, the utilization rate of electric energy is improved, and economic benefits are brought about.
Advantages of the masonry process of self-baking carbon bricks on submerged arc furnaces
The self-baking carbon brick masonry process can significantly improve the service life and economic benefits of the furnace body. Because the pre-baked carbon bricks have shrunk during pre-baking. If the whole baking process of self-baking carbon bricks is carried out in the furnace body, the shrinkage rate will be larger than that of pre-baked carbon bricks. If the quality of self-baking carbon bricks is poor, the residual shrinkage rate after baking is too large, the furnace lining will crack, and the molten metal will easily penetrate from there during the production process, resulting in furnace wear accidents. The varieties of self-baking carbon bricks are few and low-grade, and the smelting products in the triangular area are easy to penetrate into the pores of the self-baking carbon bricks, and the furnace lining is easily eroded. After the furnace lining is graphitized, the thermal conductivity is increased, which is easy to cause the furnace bottom temperature to be too high, the refractory bricks are burned out, and it is easy to cause the furnace to wear accidents.

The masonry of self-baking carbon bricks on the submerged arc furnace is different from the traditional furnace building method, which avoids the shortcomings of using baked carbon bricks for wide-slot masonry. When building self-baking carbon bricks, use anhydrous press-in mud carbon cement and fine seam paste, and apply pressure to the press. Carbon brick ring joints are tamped with low-temperature rough joint paste with matching properties. All charcoal bricks are fully machined and pre-laid. The tap hole is made of semi-graphite carbon-silicon carbide bricks with good slag resistance. The carbon bottom and furnace lining must be combined with the integrated processing and construction accuracy standards.
The furnace bottom and furnace lining of self-baking carbon bricks are gradually graphitized by using the heat in the oven and the production process and the reducing conditions in the furnace. Finally, it is calcined into a solid, dense, and integrated carbon lining, and the quality changes with the increase in temperature, that is, the carbon is converted into graphite. The self-baking carbon brick forms a dense and almost seamless whole at high temperature, which makes it difficult for the alloy to penetrate the bottom of the furnace, which greatly improves the corrosion resistance of the furnace lining and achieves the purpose of prolonging the life of the furnace lining. The production can be continuously carried out for as long as possible, which improves the utilization rate of the electric furnace, increases the thermal conductivity and electrical conductivity, improves the temperature of the molten pool, facilitates the deep insertion of electrodes, and saves various consumptions caused by furnace shutdown.
Masonry of self-cultivation carbon bricks
- ① The specifications, varieties, and quality of furnace building materials must meet the standard requirements. In particular, the semi-graphite carbon-silicon carbide bricks at the tap hole must be finished with special-shaped finishing, and the lining structure diagram should be given.
- ② Strictly follow the requirements of the furnace lining structure drawing. A 10-20mm thick asbestos felt is laid on the steel plate of the furnace bottom and furnace wall, and a layer of light clay bricks is used on the side of the furnace wall. The bottom side of the furnace is built with two layers, and all of them are built with clay refractory slurry.
- ③ Lay high-alumina refractory bricks on the upper part of the light clay bricks at the bottom of the furnace, and close to the light clay bricks of the furnace wall. The height of the furnace lining refractory bricks varies according to the specific size of the furnace shell and process requirements.
- ④ In the process of building the furnace, phosphate plus refractory particles and high alumina refractory mud are used in the transition zone between self-baking carbon bricks and refractory bricks. And according to a certain proportion with the extrusion method masonry. Then put firewood to bake to consolidate the phosphate slurry and increase the overall structural strength of the refractory masonry.
- ⑤ The inside and outside of the tap hole are built with prefabricated semi-graphite carbon-silicon carbide bricks, both sides are fixed with high-alumina refractory bricks, and the transition part is rammed with phosphate refractory concrete.
- ⑥ Finally, build a layer of refractory bricks with a thickness of 30mm on the surface of the self-cultivation carbon bricks to protect them from high-temperature oxidation during the oven process.
The life of the submerged arc furnace lining mainly depends on the degree of corrosion of the tap hole, and the semi-graphite carbon-silicon carbide brick can better solve this problem. However, the material is prone to gasification reaction with the water in the plugging under high-temperature conditions, and the exposed parts are also easily oxidized. The use of anhydrous mud blocking completely solves this problem. After using self-baking carbon bricks and using anhydrous mud plugging, the overhaul period will be extended for more than two years. The cost of self-baking carbon bricks and masonry is about 10% higher than the cost of using baked carbon bricks, and the direct and indirect costs brought about by the overhaul of the iron mouth are greatly reduced, and the relative economic value is reflected.
Leave Your Requirements on RS Kiln Refractory Bricks And Castable Materials! We Will Reply You In 12 Hours!: