Alumina-magnesia-carbon bricks are refractory products made of super-grade high-alumina bauxite or corundum sand, magnesia, and flake graphite as the main raw materials. Its characteristic is that at high temperatures, in addition to the advantages of high corrosion resistance and not easy to peel off due to carbon content, it also has the advantage of showing a high residual linear expansion rate due to the formation of spinel when heated during use. Therefore, it has become a newly developed high-quality lining brick. Rongsheng kiln refractory lining material manufacturers can provide high-quality refractory lining material products, contact us for a free quotation and samples.
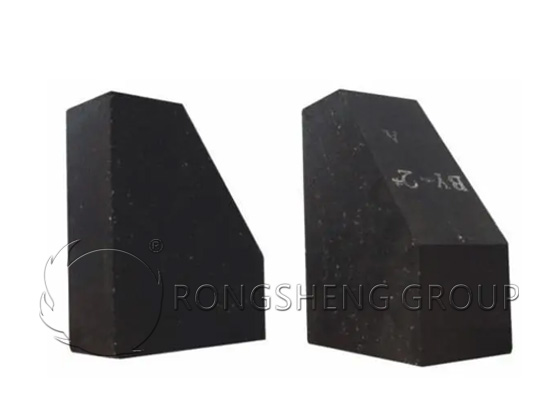
Properties of Alumina-Magnesia-Carbon Bricks
Aluminum magnesium carbon brick has good fire resistance, slag resistance, and high-temperature resistance. Alumina-magnesia-carbon bricks have the advantages of anti-corrosion, anti-stripping, balanced erosion, safe use, less slag from steel, and easy unpacking. It is mainly used for the inner lining of steel barrels with severe service conditions. Alumina-magnesia-carbon bricks are increasingly used as linings in the molten pool and bottom of large tundishes and refining ladles in continuous casting.
The use of unfired alumina-magnesia-carbon bricks on ladles. The use of unfired alumina-magnesia-carbon bricks on the ladle lining in steelmaking plants is analyzed from the aspects of repairing, baking, and maintenance. Unfired alumina-magnesia-carbon bricks have high thermal shock stability, good slag erosion resistance, and erosion resistance.
Alumina-magnesia-carbon bricks are widely used in refining ladles because of their good slag erosion resistance and thermal shock resistance. As an important parameter of alumina-magnesia-carbon bricks, slag resistance plays a guiding role in the application of bricks. However, most slag corrosion tests are carried out statically in an oxidizing atmosphere in an electric furnace. For carbon-containing refractories that are easily oxidized at high temperatures, because the carbon in the sample is partially oxidized at high temperatures, it cannot fully and truly reflect the corrosion resistance of carbon-containing refractories against slag and molten steel. The dynamic slag resistance test is adopted. Because the eroded part of the test brick sample has been under the liquid level of molten steel and slag, it is completely isolated from the air, effectively avoiding the oxidation of carbon in the brick, and more realistically simulating the use of alumina-magnesia-carbon bricks.
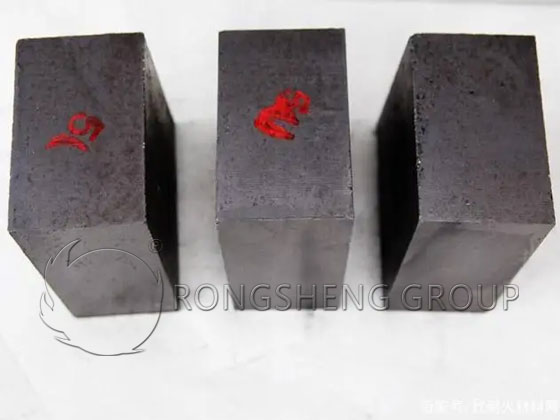
Application of Aluminum Magnesium Carbon Brick in the Ladle
Alumina-magnesia-carbon bricks are mostly used as working linings for domestic large and medium-sized refining ladles. Due to the high carbon content of aluminum-magnesium-carbon bricks, may increase the carbon content of molten steel and affect the smelting of low-carbon steel, ultra-low-carbon steel, and other types of steel. At the same time, its thermal conductivity is very large, which will increase the temperature drop of molten steel, which is not conducive to the temperature control of casting technology.
Al-Mg-C ladle bricks produce Al-Mg spinel due to the chemical reaction between Al2O3 and MgO in the matrix. The volume expansion of the product is caused, which causes stress in the working lining of the ladle during use. It will cause the brick structure to peel off and affect the safety of use.
In order to meet the very harsh working environment of the ladle lining of the LF refining system of the steel plant and meet the working conditions of the ladle, refractory manufacturers have developed long-life aluminum-magnesium-carbon lining bricks for ladles. Al2O3-MgO-C series ladle bricks for ladle lining have the characteristics of good high-temperature performance, slag resistance, and thermal shock stability.
What is the difference between magnesia carbon brick and aluminum magnesia carbon brick?
What is the difference between magnesia carbon brick and aluminum magnesia carbon brick? The difference between magnesia carbon bricks and aluminum magnesia carbon bricks is that the raw materials used are different. Alumina-magnesia-carbon bricks are fire-lined products made of super-grade high-alumina bauxite or corundum sand, magnesia, and flake graphite as the main raw materials. Its characteristic is that at high temperatures, in addition to the advantages of high corrosion resistance and not easy to peel off due to carbon content, it also has the advantage of showing a high residual linear expansion rate due to the formation of spinel when heated during use. Therefore, it has become a newly developed high-quality lining brick. Magnesia carbon brick is a resin-bonded brick made of fused magnesia and graphite. Magnesia carbon brick manufacturers, if necessary, can also add antioxidants, magnesia carbon bricks perform well in heat resistance, corrosion resistance, corrosion resistance, and peeling resistance. Magnesia carbon bricks are mainly used in the lining of converters, electric arc furnaces, DC electric arc furnaces, ladle slag lines, and other parts. Magnesia-alumina-carbon bricks are made of high-quality bauxite, corundum, fused magnesia, and graphite. Alumina-magnesia-carbon bricks have proper residual expansion, low thermal conductivity, and better insulation properties. Alumina-magnesia-carbon bricks are used for the slag line of the ladle, the lower part of the ladle wall, the bottom of the ladle, and the free area of the ladle. Ladle brick aluminum magnesium carbon brick.
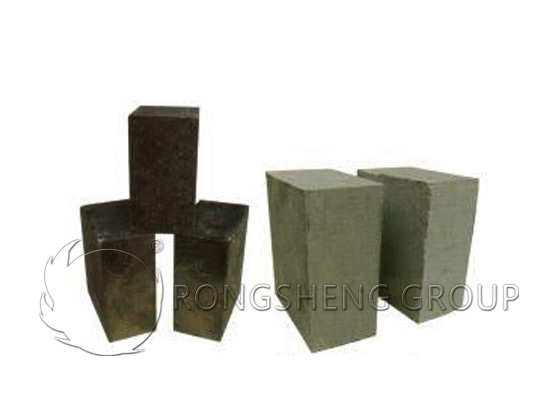
Low Carbon Bricks and Carbon-Free Bricks
Low-carbon bricks and carbon-free bricks have low carbon content, which mainly solves the problems of heat conduction of ladle and carbon increase of molten steel. It is beneficial to improve the quality of steel and is suitable for smelting low-carbon steel, ultra-low-carbon steel, and stainless steel. It is mainly used for refining ladles and other metallurgical equipment.
The low-carbon bricks used for the working lining of the ladle are made of high-quality raw materials such as high-purity and high-density fused magnesia and high-purity carbon refractory materials. Adding special composite antioxidants, binders, and additives through high-pressure compression molding, suitable for ladle slag line parts.
The carbon-free bricks used for the working lining of the ladle are made of high-quality raw materials such as high-purity corundum and spinel and are formed by high-pressure pressing with special binders. It is suitable for ladle molten pool and bottom, impact zone, and other parts. It has the characteristics of high strength, strong slag resistance, strong corrosion resistance, and good thermal shock stability. This product is specially developed for smelting ultra-low carbon steel, clean steel, etc., to meet the needs of low carbon and no carbonization in the refining ladle.
Rongsheng Kiln Refractory Material Manufacturer
Rongsheng kiln refractory material manufacturer is a refractory material manufacturer with rich production and sales experience. Rongsheng’s refractory products have been sold to more than 70 countries and regions around the world. And I believe that as our products are recognized by customers, our products will be sold to more countries and regions. Through the accumulation of many customer cases, our experience in high-temperature kiln refractory lining can help you solve the problem of refractory lining materials. Contact us for free prices, samples, and solutions.
Leave Your Requirements on RS Kiln Refractory Bricks And Castable Materials! We Will Reply You In 12 Hours!: