Self-flowing castable is a breakthrough in refractory materials, it has good fluidity. Its physical and chemical indexes and performance are better than other low cement castables. It has promotion and use value and can be used as a replacement product for vibrating materials.
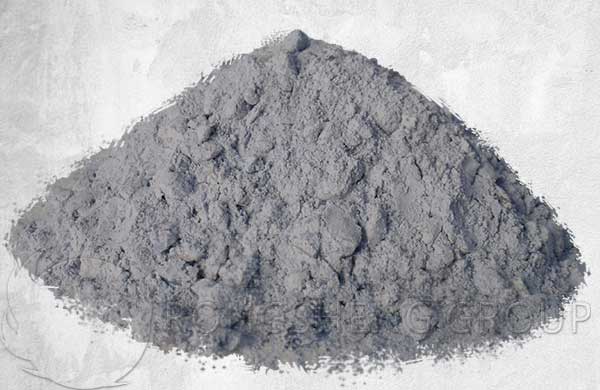
The fluidity of self-flowing castables is one of its most important properties. The factors that determine its liquidity are mainly as follows:
- The amount of water added.
Self-flowing castables are particularly sensitive to the amount of water added. The amount of water added is insufficient, the self-flow value is too small, the material cannot flow and fill normally, and the bubbles cannot be discharged. Adding too much water will cause the aggregate to sink and cause the aggregate to separate from the matrix. And too much moisture will damage the density and strength of the material, as well as corrosion resistance and wear resistance, etc.
- Gradation of particles.
The raw material configuration of the self-flowing refractory castables is generally:
(1) Aggregate, special grade bauxite. (2) Powder, special grade bauxite powder, uf-SiO2, pure calcium aluminate cement, α-Al2O3 fine powder.
The fluidity of the self-flowing material comes from the cement slurry. If the part is less than 1mm, there will be more mud and good fluidity. Too much powder will require a large amount of water, so it is advantageous to increase the particle component by 1 to 0mm. It can be seen from the experimental conclusion that it is difficult to obtain better fluidity when the particle composition of> 1mm is greater than 50%. Therefore, experimental research results show that the range of particle size composition with good fluidity is: >1mm, 35-50%; 1-0mm, 15-30%; <0.088mm, 35-50%.
- Coarse particle gradation and critical particle size.
When the raw material gradation is >1mm, 40%; 1~0mm, 20%; <0.088mm, 40%, if the amount of coarse aggregate is large, the fluidity is good. Some people say that the critical particle size should be controlled below 5mm, and the final experiment shows that its fluidity is not so good. Theoretically, the larger the particles in the >1mm component, the smaller the specific surface, the smaller the contact area with the mud, the smaller the flow resistance, and the better the fluidity.
- The impact of cement.
As the amount of cement increases, the water demand increases, the fluidity becomes worse, and it is unfavorable to the high-temperature strength. On the other hand, the amount of cement is too small, and the medium temperature strength is low. Therefore, the appropriate amount of cement is about 5%. The mineral composition of cement will also have a certain impact on the fluidity of self-flowing materials. For example, when pure calcium aluminate cement and bauxite cement are used as binding agents, the ratio of water reducing agent and dispersing agent should be adjusted.
- The influence of white clay.
The addition of white mud to replace part of the special grade bauxite barrel mill is beneficial to fluidity, the material of the milling earth will not be too sticky, and the fluidity will be improved quickly. The white mud is used as the auxiliary binding agent, and the dry strength and the strength after firing at 1000 ℃ are significantly improved. At high temperatures, the white mud helps the formation of mullite and improves thermal shock stability.
- The influence of superfine powder.
In low cement castables, silica powder plays an important role. It is good for reducing the amount of water added and increasing the strength of hydration bonding, and the compressive strength can be improved by increasing the amount of silicon micro powder added. However, the agglomeration of SiO2 fine powder will make the flow value worse. In addition, too much SiO2 powder is added, and SiO2 changes from an amorphous state to a crystalline state at a high temperature, resulting in expansion. Therefore, the proper amount of SiO2 powder is very important. In addition, the quality of SiO2 powder has a great influence on fluidity, and the average particle size should be controlled below 0.12um. Similarly, Al2O3 micro powder also has a water-reducing effect, and with the increase in the amount of addition, the decrease in fluidity is smaller. At the same time, the average particle size of Al2O3 powder should be controlled below 3um, otherwise, it will affect the fluidity of the self-flowing material. And there should be an optimal mixing ratio between Al2O3 powder and silicon powder.
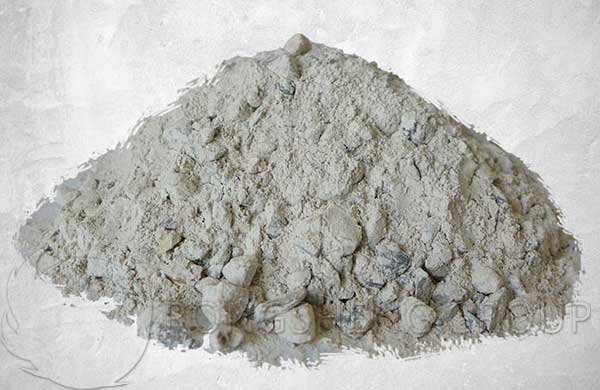
In addition, after testing, 0.8-1.2‰ of sodium hexametaphosphate is added to the self-flowing material, and the flow value of the self-flowing material reaches the best. It can not only act as a dispersant, but also play a role in reducing water, and these two properties are significantly better than sodium tripolyphosphate.
Rongsheng refractory material manufacturers provide free technical consultation for the refractory lining materials of various industrial furnaces. If you have a furnace refractory lining that needs to be replaced or repaired, or you want to find a new refractory lining solution. Please leave a message on our website page or contact us in time. We will provide you with services according to your specific needs.
Leave Your Requirements on RS Kiln Refractory Bricks And Castable Materials! We Will Reply You In 12 Hours!: