The insulation layer of the furnace lining protects the furnace shell and saves energy. Lightweight heat-insulating refractory bricks, light-weight heat-insulating castable fiberboard and other materials are mostly used as heat insulation layers.
Since the pores of lightweight heat-insulating refractory bricks or castables are larger than those of heavy materials, they are prone to shrinkage and deformation when heated during use. Therefore, under different temperature conditions, different materials of heat-insulating refractory bricks or castables should be selected to keep the inner insulation layer of the furnace lining stable. If shrinkage occurs, it is likely to cause deformation or cracks in the insulation layer in the furnace body, increasing heat loss.
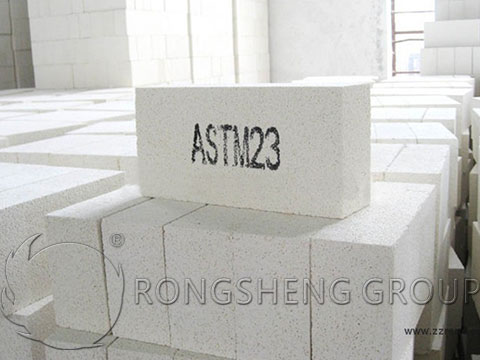
Therefore, when choosing lightweight heat-insulating refractory bricks or heat-insulating materials, it mainly depends on the ability to resist shrinkage and deformation under heating. The use temperature of heat-insulating refractory bricks generally increases with the increase of volume density. When the volume density is too high, the thermal insulation effect is not good, and the thermal insulation effect is good if the volume density is small, but the strength is too low, and it is extremely easy to peel off.
What is the Heat-Resistant Temperature of Lightweight Insulation Refractory Bricks?
That is to say, at different temperatures, it is necessary to choose insulation bricks or castables suitable for the use of temperature, or fiber materials as insulation layers. The following are different suitable temperatures for thermal insulation refractory bricks or castables for reference.
- The use temperature of slag wool is 600°C, and the use temperature range of perlite insulation material is 50-1000°C.
- The temperature range of calcium silicate insulation board is 650-1000℃.
- Vermiculite thermal insulation material can be used for thermal insulation at 1000-1150°C.
- The applicable temperature of diatomite heat-insulating refractory brick is 1000-1200℃.
- Refractory ceramic fiber 1000-1300℃.
- Anorthite lightweight insulation bricks are suitable for temperatures of 1100-1300°C.
- The applicable temperature of lightweight clay insulation brick is 1000-1350℃.
- The applicable temperature of lightweight high alumina heat insulation brick is 1350-1500℃.
- The applicable temperature of lightweight silicon insulation brick is 1500-1550℃.
- The use temperature of polycrystalline alumina fiber is 1400-1600℃.
- The use temperature of mullite lightweight heat-insulating refractory brick is 1350-1650 ℃.
- The use temperature of lightweight corundum insulation brick is 1650-1800℃.
- Alumina hollow ball insulation brick 1650-1800 ℃.
- The applicable temperature of zirconia fiber and hollow ball insulation brick is 1800-2000℃.
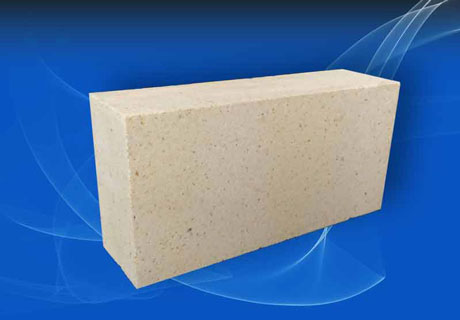
What is the Bulk Density of Lightweight Refractory Bricks?
Lightweight refractory bricks are a kind of heat-insulating refractory bricks. The volume density is referred to as body density, which means the compactness of refractory bricks. This is one of the basic indicators in all lightweight refractory brick quality standards. It is the ratio of the dry mass of lightweight refractory bricks to their total volume. That is the mass per unit volume of lightweight refractory bricks, expressed in g/cm3 or kg/m3.
Lightweight refractory bricks are characterized by light bulk density, low thermal conductivity, and low bulk density. The lower the bulk density of lightweight refractory bricks, the more pores, and the better the heat insulation effect. The refractory materials used in the production of lightweight bricks are different, and the volume density of the produced lightweight bricks is also different. For different industrial kiln environments, it is necessary to choose insulating refractory bricks with different volume densities.
The bulk density range of lightweight refractory bricks is 0.3-1.2g/cm3. Conventional lightweight refractory bricks include lightweight clay bricks, lightweight high-alumina bricks, lightweight mullite bricks, alumina hollow ball bricks, and diatomite bricks. The bulk density of lightweight clay bricks is 0.5-1.3g/cm3. The bulk density of lightweight high alumina bricks is 0.6-1.2g/cm3. The bulk density of lightweight mullite bricks is 0.3-1.2g/cm3. The bulk density of alumina hollow ball bricks is 0.6-1.0g/cm3. The bulk density of diatomite bricks is 0.7~1.0g/cm3.
Common lightweight refractory bricks have the above materials, and different materials and bulk density physical and chemical indicators have different application ranges. The bulk density of lightweight refractory bricks is one of the indicators for purchasing and selling. It is also necessary to refer to other indicators such as compressive and flexural strength, thermal conductivity, and heat capacity to determine the application of lightweight refractory bricks.
Through the understanding of the bulk density, you can have a rough judgment on the application and price of lightweight refractory bricks. However, it also needs to be comprehensive in many aspects to determine whether it is suitable for thermal kilns.
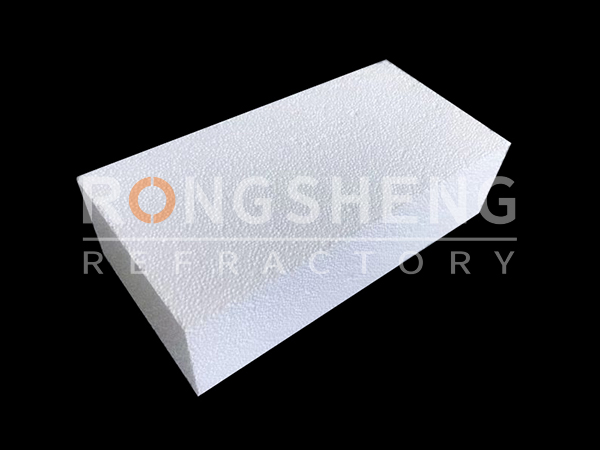
Pore-making Technology of Lightweight Refractory Materials
The formation of pores is a very important link in the production process of lightweight refractory materials. The size, shape, amount, and distribution of pores directly affect the quality of the product. There are many ways to form pores. In the industrial production of refractory materials in my country, chemical methods, foam methods, and combustible addition methods are mainly used.
- Chemical method
The chemical method refers to adding some substances that can generate air bubbles through chemical reactions in the blank. Due to the rapid reaction of this method, the generation of bubbles is not suitable for control, and an appropriate amount of inhibitors should be added according to the process requirements.
- Foam method
The foam method is to add a foaming agent to the mud, which is similar to the chemical method. The bubbles produced by the foam method are not stable enough, so a fixative should be added to control them.
The so-called Kyroplasty method to produce lightweight bricks is to add substances with low surface tension into the mud to make it foam. Pour into the model and dry together with the model. Then it is fired at a certain temperature and then processed and shaped to be a finished product. Most clay and high alumina light products can be produced by this method.
- Combustibles adding method
The method of adding combustibles refers to adding combustible substances into the mud. These additions are burned when the refractory material is synthesized at high temperatures, resulting in pores. However, this method has disadvantages such as low strength of the product blank and easy deformation of the finished product, which needs to be overcome by controlling the synthesis process.
When using the method of blending combustible additives, the combustible additives should have higher volatility and flammability. Should be able to generate fine uniform pores. It should also have less elasticity for easier molding.
Application of Lightweight Refractory Materials
As an important part of equipment such as kilns, boilers, and thermal vessels, lightweight refractory materials are widely used in industry. Due to the high apparent porosity of lightweight refractory materials, it occupies an irreplaceable position in terms of high efficiency, energy saving, and heat loss reduction. However, its products have high apparent porosity, poor chemical corrosion resistance, and cannot direct contact with fuel. So far, lightweight refractory materials are mostly used as insulation layers for high-temperature equipment. RS Kiln Refractory Factory can help you better solve the problem of refractory materials for the insulation layer of high-temperature industrial furnaces. Contact us for a free solution.
Leave Your Requirements on RS Kiln Refractory Bricks And Castable Materials! We Will Reply You In 12 Hours!: