Refractory Cement is a kind of quality castable refractory material with refractoriness that is not less than 1580℃. This unshaped refractory has many excellent properties of thermal shock resistance, strong acid resistance and high wear resistance, which can be used to cement refractory bricks or repair linings of all kinds of industrial furnace.
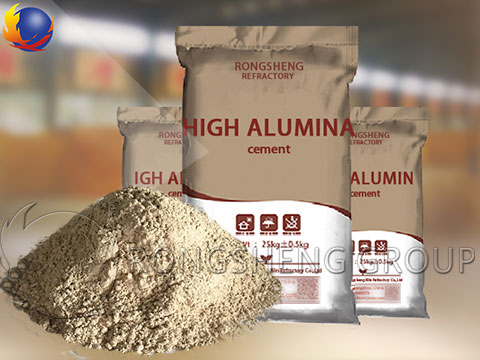
Description
Refractory Cement is made of bauxite and limestone as the raw materials, calcium aluminate as the main components and clinker containing 50% alumina content through grinding. So that it has the similar refractoriness with the refractory brick that has the same structure materials.
Such unshaped refractory can be classified into aluminous refractory cement, low calcium aluminous refractory cement, calcium-magnesium aluminate cement and dolomite refractory cement etc. Heat Resistant Cement can be used for furnace linings as the working layer for resisting high temperature erosion.
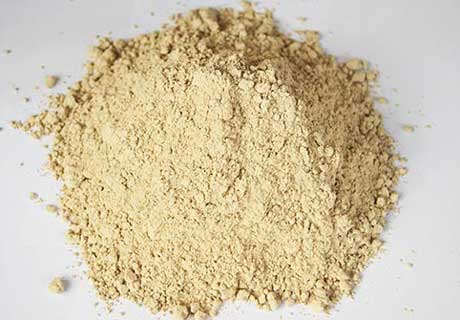
Performance
- Strong resistance to acid erosion.
- Good thermal shock resistance.
- High resistance to wear.
- Resistance to spalling.
- Complete monolithic refractory.
- Easy to construct.
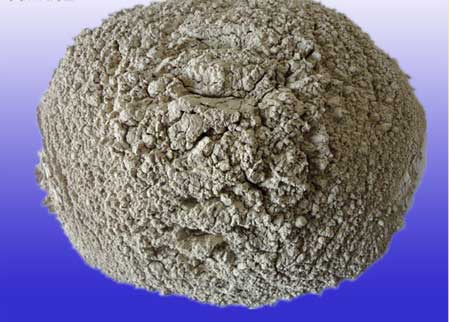
Application of Refractory Cements
Refractory Cements can be used to cement all kinds of fireproof aggregates (such as corundum, high-alumina bauxite burnt and etc.) and be made to refractory mortar or refractory concrete for linings of cement rotary kiln and other industry furnace.
Refractory Cement Recipe
Pay attention to the following matters when firing refractory lining:
- Special attention to fire slowly when at the common temperature of 350℃ which is easy to be resulted to partial cracking. If there still are amount of vapors rising, slow down the rate of temperature increase.
- Prolong the thermal insulation time suitably at the situation of thermal insulation and take strict precautions against heavy oil gush on the lining surface when fired with heavy oil in case of partial cracking.
- Take special prevent when fired with firewood and directly attach fire resulting the partial temperature increasing fast.
- New castable cement shall be fired at least after 3 days.
- Avoid forced ventilation, cool down the refractory cements lining slowly.
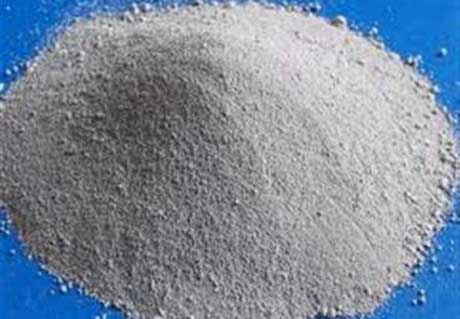
Technical Requirement for Refractory Cement
- Fineness: The cement particle is lower, the specific surface area is greater and the hydration reaction is faster and more sufficient. The early and later strength are all stronger. Nation specification: specific surface area should be greater than 300 m2 / kg, or it is unqualified.
- Setting Time: The initial setting time of cement should not be too short and ensure that there are enough time to complete all kinds of process of mix, transport and molding when in the construction. After the construction, hope the cement become harden fast and come into strength, so the setting time is not suitable to be long. The initial setting time of silica acid salt cement should not be earlier than 45 mins and the final setting time should not be later than 390 mins.
- Volume Stability: The volume of cement mortar changes at stability in the process of setting harden. If the volume change nonuniform means the bad volume stability and easy to buckling and cracking reducing the construction quality and accident happened.

Refractory Cement Suppliers
The manufacturers of refractory materials are producing and selling all kinds of refractories, for the different thermal equipment and furnaces used. As one of the supplier of Refractory Cement 3000 degree, RS Refractory Company provides you much more selection for buying refractory castable cements. RS Refractory Manufactyurer owns a new and large high quality castable refractory cements production line. For customers with the low price based on our pround of production technology and advanced equipments. Any need? Please Email Us Now For Free Quote or Use Suggestion.
Leave Your Requirements on RS Kiln Refractory Bricks And Castable Materials! We Will Reply You In 12 Hours!: