Refractory mortar and refractory cement are two different refractory materials. The following is their introduction:
Refractory Mortar
Definition and composition: Refractory mortar is composed of refractory aggregate, binder and admixture, and is the joint material of molded products.
Classification: It is divided into two categories: heavy and light. According to the binder, it is divided into phosphate mortar, water glass mortar and organic binder mud. According to the material, it is divided into clay, high aluminum, magnesium silicon, carbon mud, etc.
Characteristics: Good plasticity and convenient construction. High bonding strength and strong corrosion resistance. High refractoriness, up to 1650℃±50℃. Good slag resistance and good thermal spalling.
Application: Used for bonding gaps between refractory bricks for masonry linings of various industrial kilns. For example, magnesia refractory mortar is mainly used for masonry magnesia bricks in converters, electric furnaces, and non-ferrous metal smelting furnaces. Silica refractory mortar is mainly used for coke ovens, glass kilns, etc.
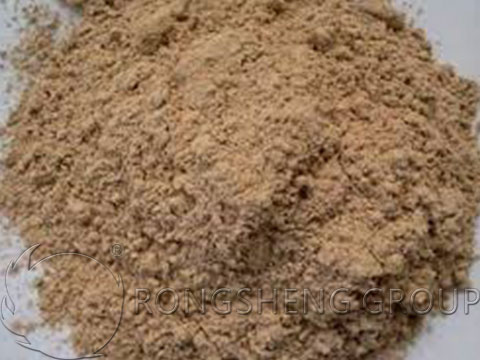
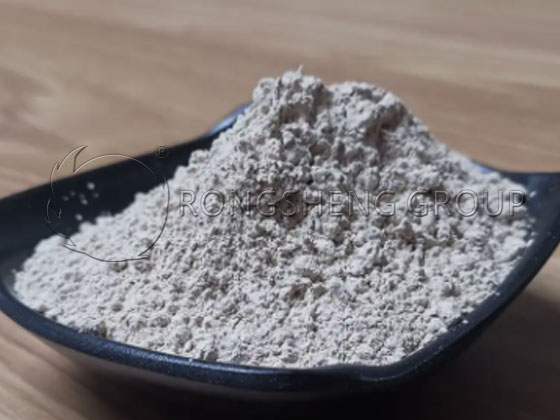
Refractory cement
Definition and composition: Refractory cement, also known as aluminate cement, is a hydraulic cementitious material made from bauxite and limestone, which is calcined to produce clinker with calcium aluminate as the main component and about 50% alumina content, and then ground.
Classification: According to the different raw materials and components, it can be divided into aluminate refractory cement, low calcium aluminate refractory cement, calcium magnesium aluminate cement and dolomite refractory cement.
Characteristics: The refractoriness is not much different from that of refractory bricks of the same quality, but it is not sintered, and shrinks more during the first blasting, and the load softening point is slightly lower than that of refractory bricks. It is better than the effect of low-temperature binders, and has a higher constant temperature compressive strength. It has good thermal stability, most or all of the aggregates are clinkers, and the expansion and shrinkage of the binder are offset. The thermal expansion of the masonry is relatively smaller than that of bricks, and the temperature stress is also small, and the ability to resist low temperature stress is strong. The production process is simple, and it can be made into various prefabricated blocks, and can be mechanized for construction, which greatly speeds up the furnace construction speed. Waste bricks can also be used as aggregates to turn waste into profit.
Application: Used to cement various refractory aggregates (such as corundum, calcined high-alumina bauxite, etc.) to make refractory mortar or concrete, used as lining for cement rotary kilns and other industrial kilns. It can be mixed with light aggregates to make insulating concrete and heat-resistant concrete. It can be mixed with asbestos to make asbestos cement products with insulation and heat-resistant properties.
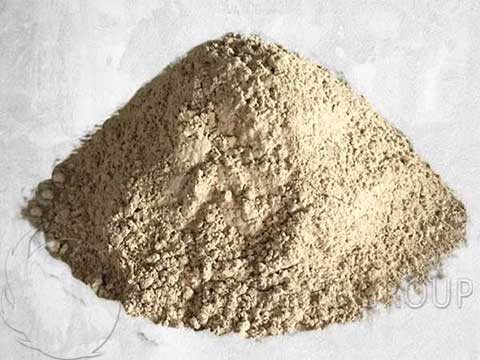
Refractory Cement for Refractory Castables
Refractory castable cement is a kind of refractory cement used in the production of refractory castables, which can be used as a binder, additive and other ingredients. Castable cement is an indispensable refractory raw material because of its stable performance and good use effect.
Castable refractory cement is a kind of cement with a refractoriness of not less than 1580℃. It uses bauxite and lime as raw materials and is mixed into raw materials with appropriate components in a certain proportion. The clinker with aluminate as the main component obtained after sintering is then ground into fine powder to make a hydraulic cementing material with refractory properties. It is a refractory clinker that can be directly added when making castables. According to the different raw materials and components, it can be divided into aluminate refractory cement, low calcium aluminate refractory cement, calcium magnesium aluminate cement and dolomite refractory cement.
What are the Characteristics and Scenarios of Refractory Mortar?
Refractory mortar is divided into two categories: heavy and light: according to the binder, it is divided into phosphate mortar, water glass mortar and organic binder mud. According to the material, it is divided into clay, high aluminum, magnesium silicon, carbon mud, etc. Refractory mortar is composed of refractory aggregate, binder and admixture, and is the joint material of molded products. It is used to bond the gaps between refractory bricks in the lining of various industrial kilns. Different refractory mortars have different proportions. The refractory mortar data obtained by testing after construction, refractory cement mortar flexural strength: 24 hours: 6.0MPa. 72 hours: 7.0MPa. Refractory cement mortar compressive strength: 24 hours: 45.0MPa. 72 hours: 55.0MPa.
Characteristics of refractory mortar:
- Good plasticity and convenient construction.
- High bonding strength and strong corrosion resistance.
- High refractoriness, up to 1650℃±50℃.
- Good slag resistance.
- Good thermal spalling resistance.
The use scenarios of refractory mortar will change according to the different materials. Magnesium refractory mortar is mainly used for masonry magnesia bricks in converters, electric furnaces, and non-ferrous metal smelting furnaces. Silicon refractory mortar is mainly used in coke ovens, glass kilns, etc. Refractory mortar is widely used and plays a significant role in construction, industry, metallurgy and other industries.
Leave Your Requirements on RS Kiln Refractory Bricks And Castable Materials! We Will Reply You In 12 Hours!: