In the part of the incinerator wall, the structure and materials on the client’s original design drawings include calcium silicate board 100mm, thermal insulation castable 60mm, lightweight brick 115mm, and silicon carbide bricks 171mm. The air ducts for air cooling and ventilation use thermal insulation castables. According to this situation, because the masonry of silicon carbide bricks is not a whole, and it is used for a long time, it is prone to local brick drop and space bulge phenomenon. It may cause the inner insulation layer to fall off and increase the temperature of the outer furnace wall, so the furnace must be shut down for maintenance.
By understanding the structure and configuration of their original refractory material according to the problems the customer has encountered. It was found that the main reasons for the bulge and cracks in the furnace wall were that the bricks were not integral, the anchoring ribs were not connected enough, and the anchoring bricks were not welded to the external steel plate, resulting in bulging. During this repair, the repair materials were adjusted to reduce the occurrence of refractory falling off. New refractory configuration: calcium silicate board 100mm, thermal insulation castable 165mm, corundum castable 171mm, with type 310 heat-resistant stainless steel anchoring nails.
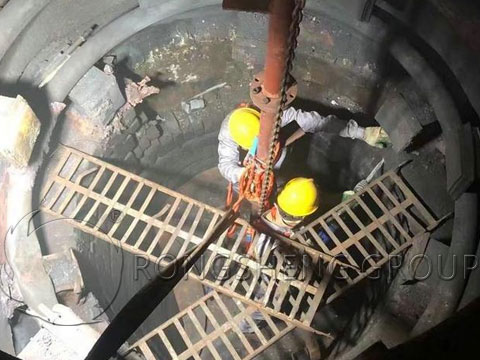
The model is 310 flat steel welding anchors, and the anchor nails are welded according to the size of the calcium silicate board, so as not to damage the structure of the calcium silicate board. After welding the anchoring nails, build calcium silicate boards and thermal insulation castables. After completion, the top of the heat-resistant flat steel is welded with a mesh steel mesh with a spacing of 150mm, and then the formwork is supported and the corundum castable is poured. When pouring the corundum castable, add water-soluble explosion-proof fiber to facilitate the discharge of water in the castable during the oven. When constructing air cooling ventilation ducts, apply a layer of anti-abrasion glue on the surface of the thermal insulation castable to prevent excessive wind pressure and wind speed from scouring the air duct and damaging the thermal insulation castable air duct. In this way, there will be no local falling bricks and bulging during construction, and the best use effect can be achieved.
Construction Schedule and Construction Schedule
Notify the construction party in advance of the shutdown time, notify the materials and workers in place in advance, and do all the preparatory work for construction.
On the day before the furnace shut down, turn on the induced draft fan to quickly reach the cooling construction temperature.
On the second day, the scaffolding in the furnace of the incinerator was erected to a working height. Remove the original furnace wall expansion joints, rear arches, refractory materials, and thermal insulation materials repaired by water walls. Check where the heat-resistant flat bar needs to be welded and weld in place.
On the third day, the masonry of calcium silicate boards was started and the pouring of the thermal insulation castable was completed.
On the fourth day, the steel mesh with a diameter of 6mm on the outside of the flat steel is welded, and the formwork is supported.
On the fifth day, the corundum material was poured and the castable was kept warm. The clot is removed from the formwork and the site is cleaned up.
On the sixth day, remove the original castables on both sides of the pusher platform drop wall, the feed chute, and the slag drop cone, and weld the heat-resistant nails and steel mesh in place.
On the seventh day, restore the thermal insulation layer on both sides of the drop wall of the pusher platform, the chute of the feed inlet, and the cone bucket of the slag outlet, and then pour the corundum material and keep the castable material. The clot is removed from the formwork and the site is cleaned up.
On the eighth day, remove the original castables on the side walls of the economizer and the manhole door, weld the gripping nails, restore the thermal insulation layer, and then restore the castables.
RS Kiln Refractory Manufacturer
Professionally solve the problem of refractory lining materials for high-temperature furnaces. RS kiln refractory manufacturer produces and sells silicon carbide refractory bricks for incinerators, high alumina bricks, corundum castables, chrome corundum bricks, thermal insulation bricks, thermal insulation castables, and other refractory materials. At the same time, we also provide the scheme configuration of refractory materials for the refractory lining of the incinerator, so as to improve the service life of the lining materials of the kiln, and reduce the number of downtimes for enterprises, save production costs and improve economic benefits.
Leave Your Requirements on RS Kiln Refractory Bricks And Castable Materials! We Will Reply You In 12 Hours!: