The reason why the insulating fire bricks can be insulated is that the brick contains a large number of pores, including closed pores and open pores. The methods for forming pores include a combustible material method, foam method, and chemical method. Silica Insulating Refractory Bricks have low compressive strength, poor slag resistance, and poor thermal shock resistance, and cannot be in direct contact with glass liquid or flame.
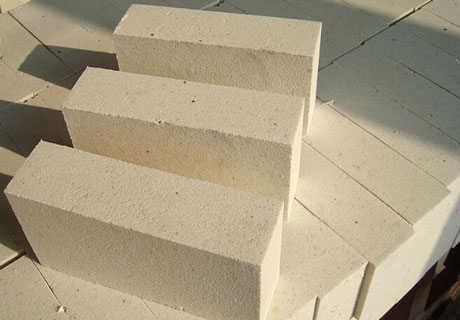
Introduction of Silica Insulation Refractory Brick
Insulation fire bricks products made of silica as the main raw material, with SiO2 content not less than 91%. In addition to the thermal insulation performance, the Silica Insulating refractory bricks maintain the characteristics of silica bricks to a large extent. Its load softening starts at a high temperature. During the heating process, the volume expands slightly, enhancing the integrity of the kiln.
Manufacture of silica insulation refractory bricks, using silica as raw material, adding some waste silica bricks or waste silica insulation refractory brick powder, mineralizers, and burn-out additives, etc. According to a certain ratio, add water to the kneading machine to mix it into the mortar. After mechanical or manual molding, the residual moisture of the brick after drying is less than 0.5% before it can be installed in the kiln. In order to prevent violent volume expansion due to SiO2 polycrystalline transformation and cause cracks in the product, a relatively slow temperature increase, and decrease speed is required during firing.
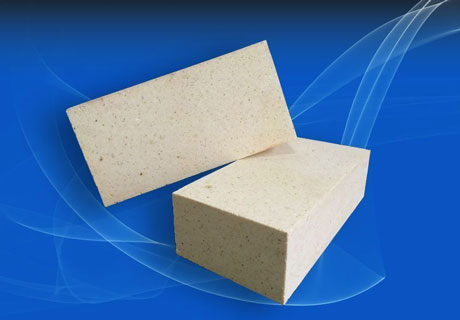
Performance of Silica Insulating Firebrick
Product performance of silica insulation firebrick for industrial furnace:
- The bulk density is not greater than 1.2g/cm3.
- The compressive strength at normal temperature is not less than 3.43MPa.
- The fire resistance is not less than 1670℃.
- The load softening start temperature is not less than 1560℃ under 0.098MPa.
- The SiO2 content is not less than 91%.
Advantages of Silica Insulating Refractory Bricks
Lightweight heat-resistant refractory bricks are also called the insulating materials, which can reduce the heat dissipation of the kiln body, save the energy consumption of the kiln, and reduce the quality of the kiln body and the overall cost of the kiln. The main performance of silica insulating refractory bricks is volume density, porosity, thermal conductivity, service temperature, and mechanical strength. There are not many insulation materials that fully meet the requirements of various performances. The shortcomings of Silica Insulating Refractory Bricks are poor heat insulation performance, and the advantage is good long-term high-temperature resistance.
The pores in the silica insulating refractory bricks are made by adding combustible materials, foaming agents or hollow spheres, and other light aggregates and the pores have a large size. These pores not only have a low thermal insulation effect but also affect the mechanical properties of the product. If the volume fraction of pores is increased, many atmospheric pores will reunite together, affecting the strength of the insulating brick. However, the specific surface area of the silica insulating refractory bricks is low, so the thermodynamic stability is good. After being exposed to heat for a long time, it is not easy to deteriorate.
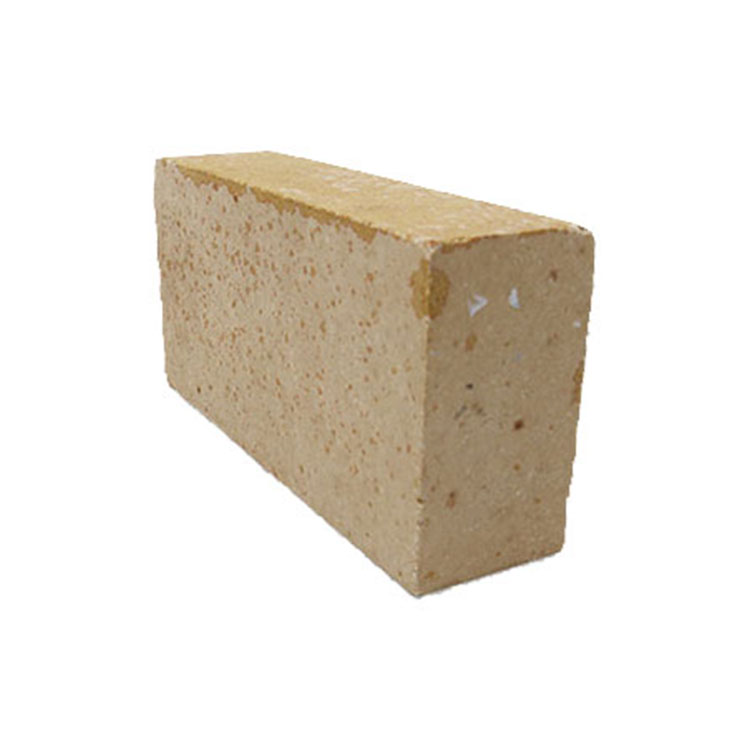
Precautions for the Use of Silica Insulating Refractory Bricks
This kind of insulating firebrick product is suitable for industrial furnace lining or heat insulation layer where the working temperature of masonry does not exceed 1550℃, does not directly contact with high-temperature molten materials and is not directly exposed to aggressive gases.
Silica insulation refractory bricks are harmful to the human body due to silica dust. The process is more complicated than clay and high alumina insulation refractory bricks, and they account for a small proportion of the total output of thermal insulation refractory materials.
Rongsheng Refractory Brick Manufacturer
Rongsheng is a manufacturer of kiln refractory bricks, with rich experience in production and sales. Rongsheng’s refractory brick products, such as high-alumina bricks, magnesia bricks, magnesia-chrome bricks, silica insulation bricks, etc., have been sold to more than 60 countries and regions around the world. Such as Malaysia, South Africa, India, Indonesia, Pakistan, Netherlands, Kuwait, Kenya, Russia, United States, Philippines, Vietnam, etc. If your thermal furnace equipment needs to use refractory brick products, please leave your specific needs on our website page. We will provide you with refractory services that satisfy you.
Leave Your Requirements on RS Kiln Refractory Bricks And Castable Materials! We Will Reply You In 12 Hours!: