As we all know, high temperature castable refractory has a simple production process, saves labor and energy, and has high construction efficiency and good quality. And can be formulated on site or choose materials with excellent performance. Also known as refractory castable. The refractory castable is composed of cement, aggregate and admixture, and sometimes accelerator is added. Refractory castable is an unshaped refractory material with large dosage and wide application range in furnace construction, monolithic refractory.
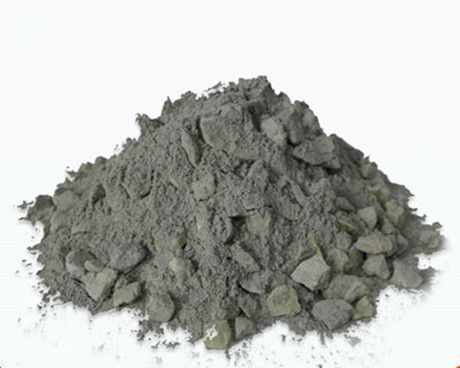
Formula Design of Refractory Castable
Refractory castable is a mixture of refractory aggregate, powder and binder. After adding water or other liquids, it is suitable for construction by pouring and vibration. It can also be prefabricated into prefabricated parts with specified shape and size for the construction of industrial furnace lining.
The formula design of refractory castables includes two parts: application design parameters and material design parameters. The refractory castables used under the set target conditions need to consider the combination of raw materials, manufacturing technology, material assembly (construction) and application technology. The goal of formula design is to find a balance between material properties and application conditions.
Generally, the type and quality of the lining refractory material of the kiln are determined according to the actual kiln operating conditions (operating temperature, furnace atmosphere, and contact state of dust, steam, liquid, or slag, etc.) and slag characteristics. If the refractory castable is selected as the target lining, the material and the suitable combination system suitable for the use conditions should be selected. And additives that can further improve and enhance performance, so that a better performance refractory lining can be made.
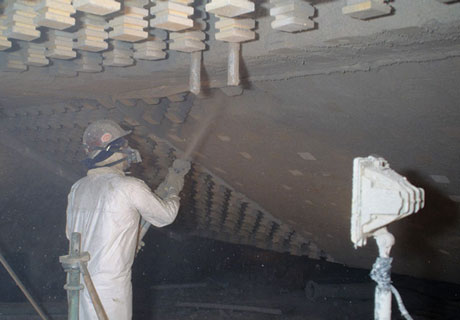
Classifications of high temperature castable refractory
Based on the actual operating conditions of the kiln, the types of castables have also become diverse.
What are the classifications of common refractory castables? According to different dimensions, common refractory castables are classified as follows.
- According to the chemical properties, it can be divided into acid-resistant castables, neutral castables and alkali-resistant castables.
- According to the composition of the bonding agent, it is divided into: organically combined casting material and inorganically combined casting material. Such as resin-bonded castable and cement-bonded castable.
- According to the selected bonding agent combination method, it is divided into: hydraulically settable castables, gas-hardened settable castables, thermosetted castables, and ceramic combined castables.
- According to the density, it can be divided into: light castable material and dense castable refractory material.
Lightweight castables are castable mixtures made of lightweight refractory aggregates and powders, binders and additives. Due to the small volume of light-weight castables and low thermal conductivity, it can also be called thermal insulating refractory castables.
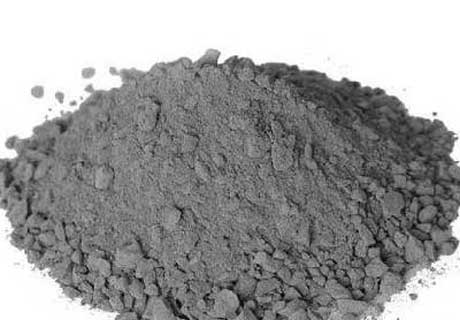
Generally speaking, light-weight refractory castables can be divided into:
Semi-light refractory castables, bulk density of semi-light castables: 1.0-1.8g / cm3.
Light refractory castables, its bulk density is: 0.4-1.0g / cm3.
Ultra-lightweight refractory castables with volume density less than 0.4g / cm3.
According to the use temperature, light castables can be divided into the following three types. Under normal circumstances, different types of lightweight castables can be selected for use according to different temperatures and different bulk densities.
Low temperature light refractory castable
The use temperature is 600-900 ℃. Low-temperature light-weight refractory castables usually use expanded vermiculite, expanded perlite and ceramsite as aggregate. Use ordinary Portland cement and alumina cement or water glass as the binding agent.
Medium temperature light refractory castable
The use temperature is 900-1200 ℃. Medium-temperature light-weight refractory castables usually use porous clay particles, clay ceramsite and shale ceramsite as aggregates. Alumina cement and calcium aluminate cement or aluminum dihydrogen phosphate are used as binding agents. Of course, we can also add a small amount of silica fine powder and floating beads to the fine powder to reduce its bulk density.
High temperature light refractory castable
The use temperature is greater than 1200 ℃. High-temperature light-weight refractory castables, this kind of refractory castables usually use corundum or high-alumina, mullite, clay, magnesium and magnesium aluminum spinel and other light particles or hollow balls as aggregate. Calcium aluminate cement, aluminum dihydrogen phosphate and silicon, aluminum sol or silica fine powder are used as the combined system.
- According to refractory raw materials, it is divided into: castables of clay, castables of high aluminum, castables of silica, mullite, castables of corundum, castables of magnesia, castables of silicon carbide, etc. .
- According to the characteristics, it is divided into high-strength wear-resistant castables, high-temperature castables, low-cement castables, steel fiber castables, acid-resistant heat-resistant castables, slag-resistant castables and other refractory castables.
The division of different dimensions, the types of refractory castables are different, and the applicable industrial kiln environment is also different. For example, aluminum-magnesium castable for ladle and aluminum silicon carbide carbon castable for blast furnace tapping. The castable can be used in a wide range. According to the industrial kiln environment, refractory castables with suitable material can be selected.
In addition, for different manufacturers of refractory castables, the classification of refractory castables is also different.
Refractory castable suppliers usually classify refractory castables based on the size of porosity, the choice of binder or bonding method, the type of aggregate and the construction method.
- According to the porosity, it can be divided into dense refractory castable and thermal insulation refractory castable;
- Classification by cementing method. Refractory castables can be divided into hydration-bonded refractory castables, chemically-bonded (including polymer-bonded) refractory castables, hydration-polymerized refractory castables (typically represented by low cement-bonded refractory castables) and cohesive-bonded refractory castables. Four types.
- According to the special effects of the binder and certain materials, it can be divided into the following 7 categories:
(1) Clay combined with refractory castables;
(2) Ultra-fine powder (such as silica fume, etc.) combined with refractory castables;
(3) Cement combined with refractory castables;
(4) Chemically combined refractory castables;
(5) ρ-Al2O3 (hydrated Al2O3) combined with refractory castables;
(6) Low cement combined with refractory castables;
(7) Silicon and aluminum sol (sol-gel) combined with refractory castables.
- According to the combination of raw materials. Refractory castables can be divided into oxide-based refractory castables, non-oxide-based refractory castables and composite refractory castables. Oxide refractory castables can be subdivided into non-alkaline refractory castables and alkaline refractory castables.
- According to the construction method. Refractory castables (body) can be divided into two categories: vibration construction refractory castables and self-flowing refractory castables.
- According to whether the refractory castable contains cement or CaO content. It can be simply divided into four categories: common refractory castable, low cement refractory castable, ultra-low cement refractory castable and cement-free refractory castable.
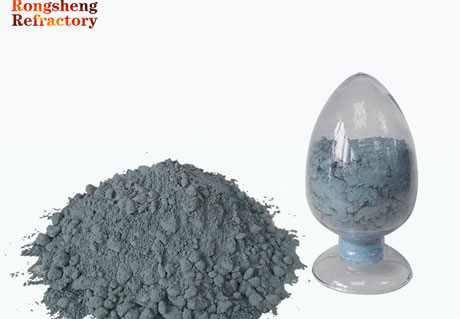
No matter how to classify refractory castables, the use of refractory castables needs to be used according to the working conditions of the kiln. A kind reminder from RS refractory castable suppliers.
Leave Your Requirements on RS Kiln Refractory Bricks And Castable Materials! We Will Reply You In 12 Hours!: