Unshaped refractories are also known as monolithic refractories. In the common terminology of unshaped refractory, it often appears, refractory mortar, refractory cement, refractory castable. They are all bulk materials, but they are three different refractory materials. From Rongsheng Refractory Manufacturer, Refractory mortar is the joint material or bonding material when building refractory bricks. Refractory cement is a kind of high temperature resistant cementing material. Refractory castables are composed of multiple materials. They all play an important role in the refractory lining of thermal kilns.
How to Reasonably Select Unshaped Refractories
First of all, it is necessary to understand the characteristics of refractory mortar, refractory cement, and refractory castables in order to select and use. Regarding the use of refractory mortar, refractory cement, or refractory castable with high-temperature resistance, it is necessary to make a suitable choice according to different situations.
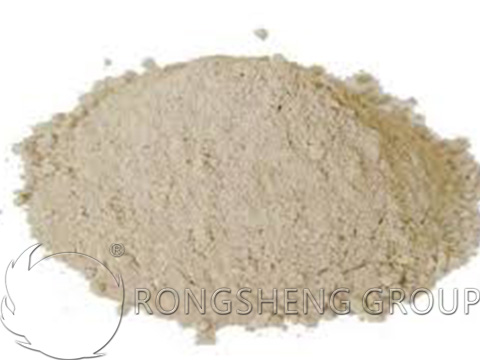
Refractory Mortars
Refractory mortar also called joint material. Used as a jointing material for refractory bricks masonry.
According to the raw material, it can be divided into clay, high alumina, silica, and magnesia. It is composed of refractory powder, binder, and admixture. Almost all refractory raw materials can be made into a powder used to make refractory mortar. The general refractory clay mortar is made of refractory clinker powder and an appropriate amount of plastic clay as a binder and plasticizer. Its strength at room temperature is low, and the ceramic bond formed at high temperatures has high strength. A chemically bonded refractory clay mortar that uses hydraulic, air-hardened, or thermosetting bonding materials as the bonding agent. A certain chemical reaction occurs and hardens before it is lower than the bonding temperature of the ceramic. The particle size of refractory mortar varies according to application requirements. Its limit particle size is generally less than 1mm, and some are less than 0.5mm or finer.
Refractory mortar is used for refractory bricks masonry. When masonry, the refractory mortar of the same material should be matched according to the material of refractory bricks. If masonry clay bricks use clay refractory mortar, use high alumina fire mortar for masonry high alumina bricks, use magnesia fire mortar for masonry bricks, and use charcoal fire mortar for carbon brick masonry.
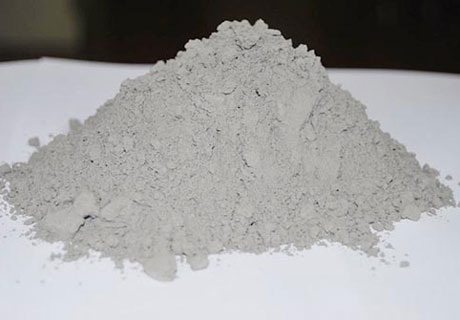
Refractory Cement
Refractory cement is usually yellow or brown, and also gray. Often refers to refractory cement with calcium aluminate as the primary component.
Refractory cement is an unshaped refractory material, especially it can be used as a binder for casting refractory materials. Refractory cement uses bauxite and limestone as materials and is calcined to produce clinker with calcium aluminate as the primary component and about 50% alumina content.
After the refractory cement is mixed with water or a liquid binder, the mixture gradually loses thixotropy or plasticity and becomes cohesive. The time required for this process is called cohesion time. The initial loss of plasticity is called the initial setting, and the complete loss of plasticity is called the final setting. In order to satisfy the construction requirements, the initial setting time shall not be earlier than 40 minutes, and the final setting time shall not be later than 8 hours. When used for spraying and eruption operations, it is required that the coalescence time be as short as possible.
High alumina cement is one of the refractory cement binders. It needs to be mixed with refractory aggregates or high alumina aggregates of different particle sizes to have a certain strength. There is a certain connection between high alumina cement and refractory castable. Because refractory castables must have refractory cement as a binder, various refractory aggregates can be cemented together to have certain structural strength and wear resistance. If castable refractory cement is used alone, the strength is low and it is easy to crack or peel off. Especially as the temperature increases, this manifestation becomes more serious. Therefore, high alumina cement cannot be used alone.
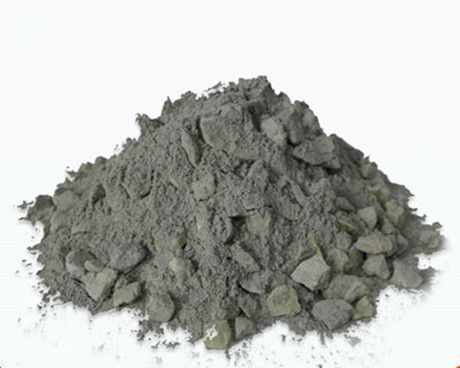
Refractory Castable
Refractory castable is currently the most widely produced and used unshaped refractory. Mainly used to construct various heating furnace linings and other integral structures. Certain high-quality refractory castables can also be used in smelting furnaces. Unshaped Refractories, For example, aluminate cement refractory castables can be widely used in various heating furnaces and other thermal equipment without slag, acid, and alkali corrosion.
Refractory castables should be used in the parts where the high-temperature furnace is in direct contact with the flame and is damaged by corrosive gas. Refractory castable is composed of various refractory aggregates as the main raw material, refractory cement as the binding agent, adding anti-shrinking agent, explosion-proof fiber, coagulant and other admixture materials to form an integral lining material. Without gaps, it has high structural strength and resistance to slag penetration.
Refractory castables are lining materials used in high-temperature furnaces. It can be cast molding, self-flow molding, ramming construction, spraying construction, custom-made pouring material precast block masonry construction, etc. As Unshaped Refractories, There are many kinds of refractory castables. Commonly used are high-alumina castables, corundum castables, low cement castables, mullite castables, wear-resistant castables, impermeable materials, self-flowing castables, plastics and so on.
Inorganic binders can be divided into cement and other types of binders. The Cement binder includes Portland cement and aluminate cement. Mainly through the hydration of cement to make the refractory castable strength. Other types of binders include water glass, phosphoric acid, phosphate sulfate, soft clay, and ultrafine powder. Mainly through its chemistry, polymerization, and cohesion, etc., make the unshaped refractory material have strength.
Bonding Agent for Refractory Castable
Binders are cementing materials that bind materials together. Mainly used for cementing refractory aggregates and refractory powders to increase the strength of refractory castables. There are many binding methods for binding agents, which are mainly divided into organic binding agents and inorganic binding agents. Generally, inorganic binding agents are commonly used.
Organic binders mainly include sulfite pulp waste liquid, dextrin, starch, methylcellulose, ethyl silicate tar pitch, and phenolic resin. Mainly through its new binding, polymerization or condensation-carbonization, etc., the refractory castable gains strength.
There are many types of bonding agents, and different bonding agents are used in different refractory castables. Refractory castables rely on binders to combine refractory aggregates and powders without high-temperature sintering before use. After high-temperature sintering, the refractory aggregate and the powder are more bonded, and the strength of the refractory castable is increased.
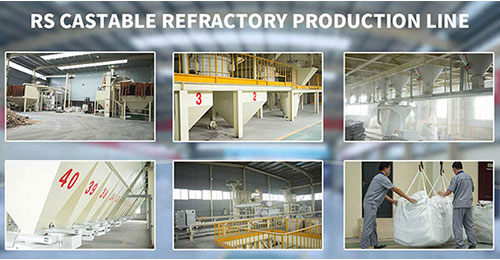
Rongsheng Unshaped Refractory Manufacturer
The above is the suggestion of Rongsheng refractory material suppliers on how to choose the monolithic refractory material. In summary, refractory mortar, refractory cement, and refractory castables are all unshaped refractory materials. Refractory mortar is used to build refractory bricks, and refractory cement is a material for making refractory concrete. Refractory castables are made of refractory aggregates, powders, and binders. They are also called castables due to the use of pouring construction. To purchase unshaped refractories, please contact us. We will provide you with not only high-quality refractory products but also satisfactory services.
Leave Your Requirements on RS Kiln Refractory Bricks And Castable Materials! We Will Reply You In 12 Hours!: