The rotary kiln adopts refractory castable integral pouring technology, which has been adopted in lime, cement, activated carbon, hazardous waste treatment, and other industries. Although it has excellent performance and reasonable cost performance, if it is poured directly in the rotary kiln, the longer curing and baking time after construction will still cause inconvenience to the user of the rotary kiln. Therefore, the application of Refractory Castable Precast Blocks for Rotary Kilns is imperative.
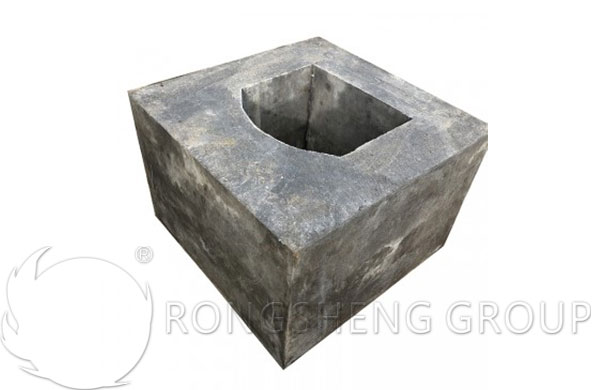
Classification of Refractory Castable Precast Blocks
Prefabricated blocks are also called prefabs, which belong to the category of unshaped refractory materials, and are a kind of material with rapid development and wide application. The reason why the Refractory Castable Precast Blocks belongs to unshaped refractory is that the raw material composition, formulation principle, use of bonding agent, and admixture of unburned bricks are basically the same as monolithic refractories, and they are unburned or light burned products.
- According to different classification standards, prefabricated blocks include refractory castable precast blocks and plastic precast blocks.
- According to different binders, there are refractory precast blocks such as aluminate cement, glass water, phosphoric acid and aluminum phosphate, clay binding, and low cement.
- According to the different forming-methods, there are vibration forming, vibration pressure forming, and ramming forming refractory precast blocks.
- According to different sizes, there are large, medium, and small precast blocks.
- Finally, there are ordinary refractory precast blocks, reinforced refractory precast blocks, and anchored refractory precast blocks.
With the method of pouring prefabrication, various prefabricated parts of different sizes and shapes can be made. It can complete “shaped” products with more complex shapes, larger quality and volume, and better performance than press forming. Therefore, the refractory castable precast blocks have become a worthy direction for the development of monolithic refractories and have broad development prospects.
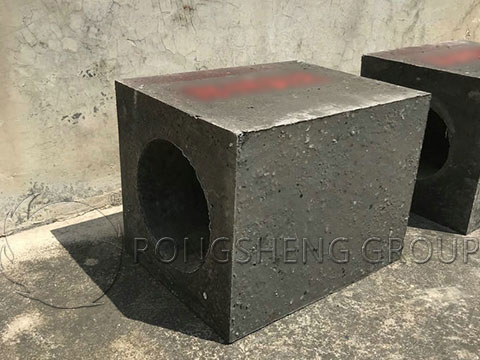
Rotary Kilns Refractory Castable Precast Blocks
The design and selection of the prefabricated parts in the rotary kiln must ensure that the kiln lining after the masonry is concentric with the kiln shell. To ensure the smooth progress of construction and use, to achieve the purpose of improving the lives of the kiln and thermal equipment. According to the characteristics of the rotary kiln, the basic shape of the Refractory Castable Precast Blocks is as follows:
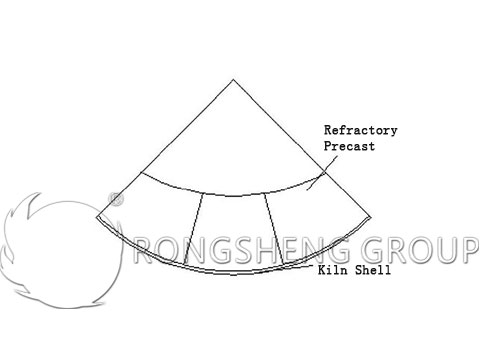
Among them, the inner and outer radii of the Refractory Castable Precast Blocks vary according to the type of rotary kiln and the different parts of use. The thickness of the refractory precast blocks is the difference between the inner and outer radius of the rotary kiln after the furnace is built. The use environment of the rotary kiln hood and the firing zone is different, so the refractory precast blocks are also different. The introduction is as follows:
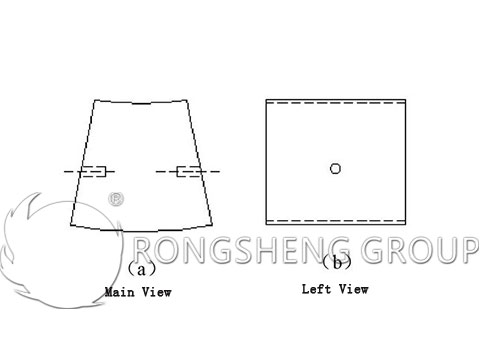
(1) Kiln Hood Refractory Castable Precast Block
The temperature at the kiln hood of the rotary kiln fluctuates between 1100°C and 1400°C, the temperature changes greatly, and the barrel is extremely easy to deform. As a result, the refractory lining material at the kiln mouth often falls off, and the service life is very short. Therefore, the refractory precast block at the kiln hood is designed as follows. The outer circumference of the Refractory Castable Precast Blocks is one-tenth of the cylinder, and the thickness depends on the radius of the cylinder. Punch φ20X40mm holes on both sides of the preform. In masonry, in addition to fixing the prefabricated parts with refractory mortar, they are also strung together with φ18X60mm heat-resistant steel sections at the punching point. In order to form a whole refractory precast block, it will not fall off during use, prolong the service life of the material, and improve the operating efficiency of the kiln.
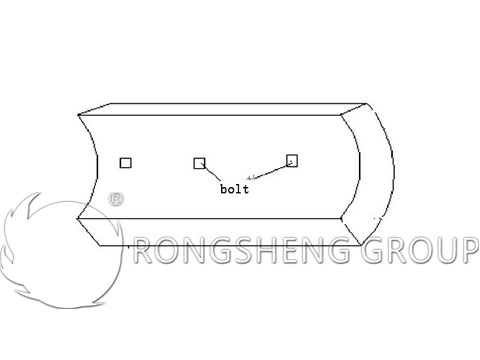
(2) Firing Zone
Considering the higher temperature of the firing zone, the shape of the refractory castable precast blocks is different from that of the kiln hood. The outer circumference of the refractory precast block is one-eighth of the cylinder, and the thickness depends on the radius of the cylinder. The preforms are bonded by refractory mortar, and the fixing method between the precast blocks and the cylinder is bolted. Weld nuts on the body of the rotary kiln, as shown in the figure below. Each piece of the precast block is equipped with six anchor bolts according to its size. The anchor bolt material is made of φ10mm threaded steel, and the length of the anchor bolt is between 1/2 and 2/3 of the thickness of the refractory precast block. The bolts are covered with mud core inserts of the same material as the prefabricated parts and fixed with refractory mortar.
In addition, in order to solve the difference in expansion coefficient between the anchor and the refractory castable in the hot state, a thick asphalt paint film is painted on the outside of the anchor. In the hot state, the pouring will not burst due to the thermal expansion of the refractory anchors. These are conducive to improving the overall strength of the castable and the adhesion strength of the equipment.
Advantages of Using Refractory Precast Blocks
Compared with the unshaped refractories constructed on-site, it has the advantages of accurate dimensions, stable performance, short construction period, and low cost. Compared with fired refractory bricks, the finished product rate is high, without firing kilns, energy-saving, low production cost, and excellent performance. Therefore, refractory castable precast blocks and unfired bricks have broad prospects for development.
In industrial kilns and thermal equipment, refractory castable precast blocks are used to build furnaces. Compared with unshaped refractory materials and fired refractory bricks constructed on-site, it has the following advantages:
- Prefabricated parts have the advantages of accurate external dimensions, stable performance, short construction period, and low cost. No need for pouring on-site, just assembling and combining, simplifying the furnace building process.
- Compared with fired bricks, the finished product rate of prefabricated products is high, without firing kiln, it can save energy, low production cost, and excellent performance.
- Because the preforms have been poured, cured, and dried at the time of delivery. It saves a lot of time for users and can speed up equipment conversion and utilization.
- The construction can not be restricted by environmental conditions or seasonal conditions.
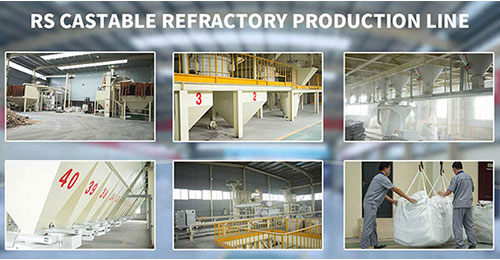
Rongsheng Refractory Castable Manufacturer
Rongsheng refractory castable manufacturer is an experienced refractory manufacturer. Rongsheng’s advanced fully automatic unshaped refractory production line has an annual output of 80,000 tons. The orders for Rongsheng Kiln Refractory Manufacturer‘s unshaped production line are also derived from the trust of customers in Rongsheng’s products and brand. Solving the problem of refractory lining of thermal equipment for customers and saving production costs are the standards for Rongsheng to serve customers. If you want to know about Rongsheng Company or want to buy unshaped refractory products, please contact us. We will provide you with services according to your specific needs.
Leave Your Requirements on RS Kiln Refractory Bricks And Castable Materials! We Will Reply You In 12 Hours!: