Refractory castables for high-temperature kilns refer to mixtures composed of refractory aggregates, binders and admixtures. It is a high temperature-resistant unshaped refractory material mixed with water (or liquid binder) and constructed by the pouring method. The difference from other amorphous refractories is that there is a certain setting and hardening time after the construction of refractory castables. Therefore, it takes a certain time of curing after casting to demold. Then it can be put into baking after a proper period of natural curing.
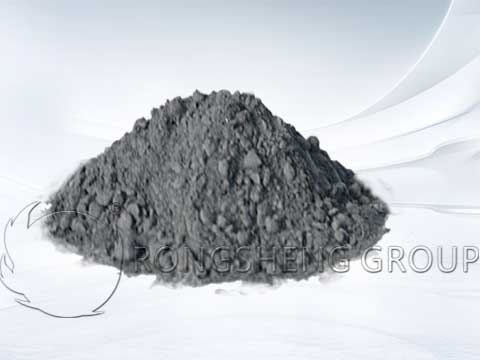
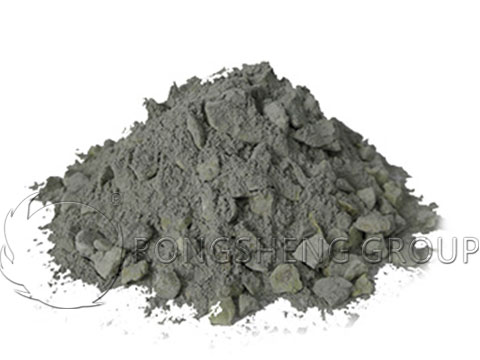
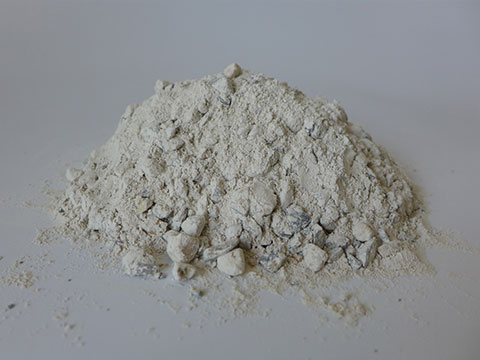
Classification of Refractory Castables for High-Temperature Furnaces
Refractory castables are mainly classified according to porosity, binder, and aggregate variety. In actual use, it is generally classified according to the use temperature or the functional characteristics required by the use site.
Porosity is divided into two types: dense castables and heat-insulating castables with a porosity of not less than 45%. In dense refractory castables, the matrix accounts for 25-35% of the total volume of the castable, while the pores account for about 10% of the total volume of the matrix.
Hydraulic bonding, chemical bonding, and condensation bonding castables are classified according to binders.
Hydraulic castables harden by condensation at room temperature and harden by hydration. The main varieties are Portland cement, ordinary calcium aluminate cement, pure calcium aluminate cement, fused pure calcium aluminate cement castables, etc. At room temperature, chemically bonded castables are usually hardened by adding a hardener to form a chemical reaction. The main varieties are water glass, aluminum sulfate, phosphate castable, and so on. Condensation-bonded castables are hardened after sintering during the calcination process, and the main variety is clay castables.
The refractory aggregate, it is divided into clay aggregate, high alumina aggregate, and silicon aggregate. Alkaline aggregate, magnesia, dolomite, etc. Special aggregates, carbon, carbide, spinel, zircon, nitride, etc. Thermal insulation aggregates, including perlite, vermiculite, ceramsite, floating beads, light brick sand, porous clinker, alumina hollow spheres, etc.
Key factors affecting high-temperature flexural strength of refractory castables
The working environment of refractory materials requires them to have good mechanical properties not only at room temperature but also at high temperatures. Therefore, high-temperature flexural strength is one of the important performance indicators of refractory materials. The high-temperature mechanical properties of a material mainly depend on two factors:
- (1) The amount and viscosity of the glass matrix (glass effect);
- (2) The degree and manner of contact or bonding between crystals (crystallization effect).
High-temperature flexural strength refers to the ultimate bending stress that a material can withstand per unit section at high temperatures. Indicates that the material resists bending moments at high temperatures. The high-temperature flexural strength of refractory materials is closely related to their actual use and is an important indicator for evaluating material properties. Its size depends on the chemical and mineral composition of the material, its structure, and its production process. The impurities in the material and the combustion temperature have a significant effect on the high-temperature flexural strength of the material. The mechanical behavior of ceramic composites at different temperatures can be divided into three stages:
- (1) Elasticity stage. The temperature curve of flexural strength is a straight line, and creep will not occur under long-term stress. After the fracture test, the fracture was smooth, and the crystal was mainly fractured.
- (2) Plastic deformation stage. Flexural strength-temperature curve hysteresis. Under long-term stress, the creep is obvious, the fracture is smooth and rough, and the crystal and transgranular are mixed to fracture.
- (3) Viscosity flow stage. The temperature curve of flexural strength is arc-shaped, the permanent deformation is large, the creep rate increases sharply, and the fracture is rough, mainly along the crystal.
Buy dense castable refractory 1700℃ for high-temperature industrial kilns. Please contact us. Based on your specific needs, we will provide you with the most suitable refractory castable product for your production needs.
Leave Your Requirements on RS Kiln Refractory Bricks And Castable Materials! We Will Reply You In 12 Hours!: