Alumina ceramics are becoming the future of the materials industry with their outstanding performance. They have high hardness, wear resistance, corrosion resistance, and high-temperature resistance, and are widely used in machinery, electronics, medical treatment, food, chemical industry, and other fields. At present, alumina ceramics have become one of the most widely used and largest-volume ceramic new materials among oxide ceramics.
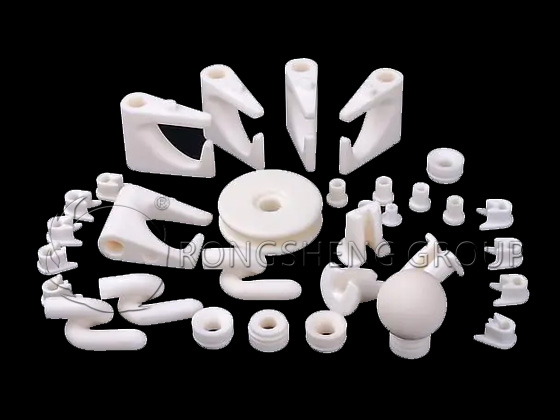
Categories of Alumina Ceramics
Alumina ceramics are advanced ceramic materials containing aluminum oxide (Al2O₃) as the main component. They are made through artificial synthesis, precision design, and precise preparation and show excellent performance. Alumina ceramics are divided into high-purity and ordinary types.
High-purity alumina ceramics are ceramic materials with an Al2O3 content of more than 99.9%. Because its sintering temperature is as high as 1650-1990℃ and the transmission wavelength is 1-6μm, it is generally made into molten glass to replace platinum crucibles. It is used as a sodium lamp tube based on its light transmittance and resistance to alkali metal corrosion. In the electronics industry, it can be used as an integrated circuit substrate and high-frequency insulation material.
Ordinary alumina ceramics are divided into 99 porcelain, 95 porcelain, 90 porcelain, 85 porcelain, and other varieties according to the content of Al2O3. Sometimes those with an Al2O3 content of 80% or 75% are also classified as ordinary alumina ceramics. Among them, 99 alumina ceramic materials are used to make high-temperature crucibles, refractory furnace tubes and special wear-resistant materials, such as ceramic bearings, ceramic seals, and water valve plates. 95 alumina ceramics are mainly used for corrosion-resistant and wear-resistant parts. Since 85 porcelain is often mixed with some talc, the electrical properties and mechanical strength are improved. It can be sealed with metals such as molybdenum, niobium, and tantalum, and some are used as electric vacuum device components.
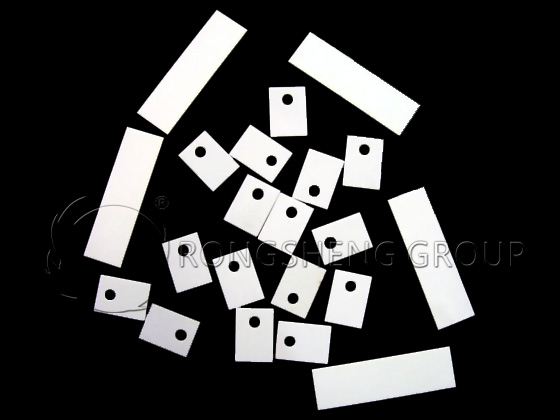
Characteristics of Alumina Ceramics
- High hardness
The Rockwell hardness of alumina ceramics is HRA80-90, which is second only to diamond and far exceeds the wear resistance of wear-resistant steel and stainless steel.
- Excellent wear resistance
The wear resistance of alumina ceramics is equivalent to 266 times that of manganese steel and 171.5 times that of high-chromium cast iron. According to the manufacturer’s follow-up survey of customers over the past decade, under the same working conditions, the service life of the equipment can be extended by at least ten times.
- Lightweight
The density of alumina ceramics is 3.5g/cm3, which is only half of that of steel, which can greatly reduce the load on the equipment.
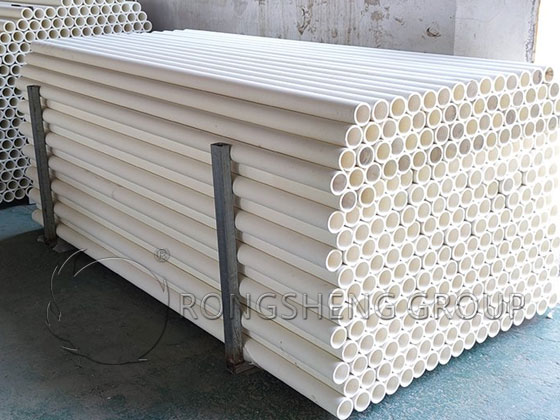
Wide Application of Alumina Ceramics
Alumina ceramics have attracted much attention due to their powerful performance and wide application. From purity, and microscopic morphology to electrical properties, alumina ceramics have shown unique advantages and provided diversified solutions for different industries.
From the perspective of purity:
Alumina ceramics show different physical and chemical properties with their different alumina contents, providing rich options for product research and development. High-purity alumina ceramics (Al2O3 content is 99.9%) have excellent transmittance (transmission wavelength is 1-6μm), high sintering temperature (up to 1650℃) and stability, and are suitable for the manufacture of high-precision electronic devices. Ordinary alumina ceramics meet the needs of general industrial applications with their wear and corrosion resistance.
It is worth mentioning that the preparation technology of high-purity alumina granulation powder has been successfully broken through. Alumina ceramics with 99.5%, 99.7% and 99.9% purity can be customized according to customer needs to meet the personalized needs of different process formulas and product designs.
From the perspective of density:
Through the high-temperature sintering process, alumina forms a compact and uniform crystal structure. This structure gives it high hardness, high melting point and excellent chemical stability. Products used in the electronics field must have good density to ensure good bending resistance and wear resistance.
From a functional perspective:
Alumina porous ceramics, as a high-performance ceramic material, have uniform pore size distribution and are interconnected internally, allowing fluids or gases to pass smoothly, with efficient adsorption capacity. And it can still maintain a large vacuum force in a high-temperature vacuum environment and is not easily blocked. This partial area adsorption characteristic makes it an ideal choice in many specific application scenarios. Whether in extreme temperature, pressure or chemical environment, it can maintain the stability and reliability of its performance. This makes it an ideal material for high-precision and high-requirement fields such as electronics and panels.
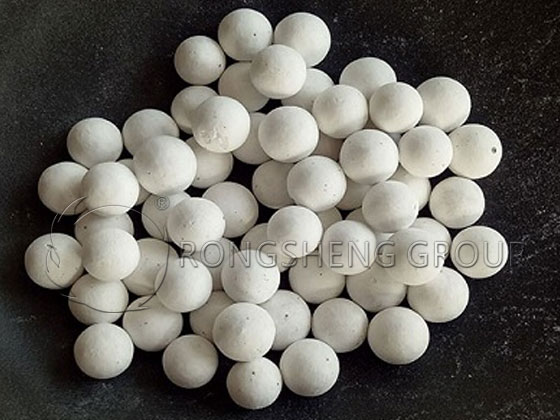
From the perspective of electrical performance:
Alumina ceramics can be generally divided into the following two categories according to their electrical uses:
Alumina insulating ceramics:
Insulators, alumina ceramics, as a high-performance ceramic material, have become an indispensable part of the electronics industry because of their high electrical insulation performance, excellent mechanical strength and excellent thermal stability. In conventional electrical applications, this ceramic material can effectively isolate current, ensure the stable operation of electronic equipment, and maintain the stability of its performance under high-temperature environments.
Alumina antistatic ceramics:
In the fields of electronics, optics, etc., the accumulation and discharge of static electricity may cause serious damage to the equipment, and even cause the equipment to fail. Antistatic alumina ceramics can effectively prevent the accumulation and discharge of static electricity, thereby protecting electronic equipment from static damage. For example, in the manufacturing process of electronic equipment, the use of antistatic alumina ceramics can effectively prevent static electricity from damaging the internal circuits of the equipment. In the manufacture of optical instruments, the use of this material can protect optical components from the influence of static electricity and ensure the normal operation of the optical system.
High-Quality Alumina Ceramic Manufacturers
In the manufacture of high-precision and high-performance electronic components, alumina materials are widely used in the manufacture of some key electronic components due to their unique physical and chemical properties. These components have extremely high requirements for the performance of ceramic materials, including lower dielectric loss, excellent microscopic grain distribution, and fewer contaminant particles.
Dielectric loss is an important indicator for evaluating the degree of energy loss of ceramic materials in an electric field. For electronic products, low dielectric loss means less energy waste, higher efficiency, and more stable performance. Alumina ceramic manufacturers are committed to optimizing the preparation process, precisely controlling the purity of raw materials, and optimizing the crystal structure of ceramic materials through advanced technology. These efforts ensure that alumina ceramic materials can meet the strict requirements of low dielectric loss in the electronics manufacturing industry.
Microscopic grain size and distribution are also one of the key factors affecting the performance of ceramic materials. Through scanning electron microscope (SEM) scanning image analysis, the difference in microscopic grain size and distribution between unqualified powder and high-quality alumina powder is compared. Among them, unqualified powders, adhesion and agglomeration, and apple-shaped and pitted powder forms may lead to microscopic defects in the finished ceramic products, which in turn affect the macroscopic properties of the products such as corrosion resistance, wear resistance, and mechanical strength. High-quality alumina ceramic powders have round and full powder shapes, uniform sizes, and excellent distribution of powder particle sizes, which provide excellent performance guarantees for ceramic products.
In addition, the presence of contaminated particles will seriously affect the purity and performance of ceramic materials. During the manufacturing process, the number and size of contaminated particles must be strictly controlled to ensure that the purity and performance of ceramic materials meet the requirements. This is of great significance for improving the reliability and service life of electronic components. We are well aware of the importance of alumina ceramics in the production process. Therefore, we have implemented strict monitoring of the amount of pollutants introduced in all aspects of production. Once a particle contamination problem is discovered, we immediately initiate rectification and optimization measures to ensure that the problem is quickly resolved, thereby ensuring that the purity and performance of ceramic materials are in the best state.
Leave Your Requirements on RS Kiln Refractory Bricks And Castable Materials! We Will Reply You In 12 Hours!: