The question of the content of AL2O3 in Fireclay Lightweight Insulation Bricks is a technical indicator that is not emphasized. As a refractory material in this aspect of lightweight insulation bricks, the performance value to be reflected in the thermal conductivity and compressive strength of the material in use. It is required to better reduce the outflow of the heat source and effectively achieve the effect of energy-saving.
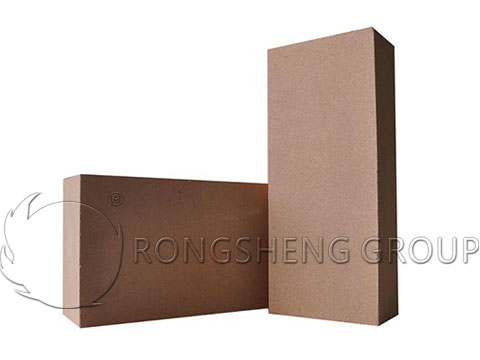
As a refractory brick manufacturer that produces lightweight insulation bricks, Rongsheng will be more inclined to study how to improve the compressive strength of lightweight insulation bricks and reduce thermal conductivity. However, as a customer who buys this product, sometimes he is obsessed with pursuing a certain index of refractory bricks. For example, many of our customers will ask about the content of AL2O3 in lightweight insulation bricks because of their purchasing habits. According to international standards, national standards, industry standards, and actual use effects, the content of AL2O3 in Fireclay Lightweight Insulation Bricks can only be within a certain range, and there is no exact value. However, no matter what point of view we consider, we ultimately want to fulfill the needs of energy-saving and consumption reduction in the production of customers.
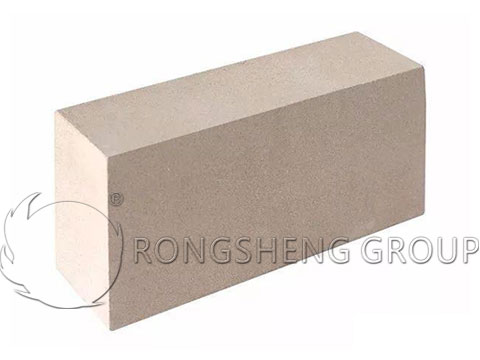
Commonly Used Fireclay Lightweight Insulation Bricks
Light clay bricks refer to light refractory products with 30% ~ 46% alumina content, using clay clinker or light clinker and plastic clay as the main raw materials. Fireclay Lightweight Insulation Bricks are mainly made of floating beads in fly ash from thermal power plants. Add an appropriate amount of binder and auxiliary materials. The auxiliary materials used are mainly Yangquan’s refractory clay whose fineness all passes through a 100-mesh sieve. Then, after being evenly mixed, it is pressed into a shape and calcined at a high temperature to form a lightweight refractory insulation product.
It is usually produced by the combustible method, and can also be formed by the chemical method or the foam method to form a porous structure. The ingredients are mixed with water to make plastic mud or mud, which can be extruded or poured. After drying, it is fired in an oxidizing atmosphere at 1250~1350°C.
The bulk density of commonly used lightweight fireclay bricks is 0.7~1.2 g/cm3, the compressive strength is 2.0~5.9Mpa, and the thermal conductivity is 0.221~0.442W/(m.K) (1350℃). The product is divided into three specifications of 0.6g/cm³, 0.8g/cm³, and 1.0g/cm³ according to the bulk density. The 0.8 and 1.0 grades can be used as the lining or heat insulation layer of various industrial furnaces that do not contact the molten material and the non-corrosive gas medium. It is an ideal energy-saving material.
The Use of Lightweight Fireclay Bricks
Lightweight fireclay bricks have a wide range of uses, mainly used in various industrial kilns that do not touch the melt and have no corrosive gas effect. The operating temperature is 1200 ~ 1400℃.
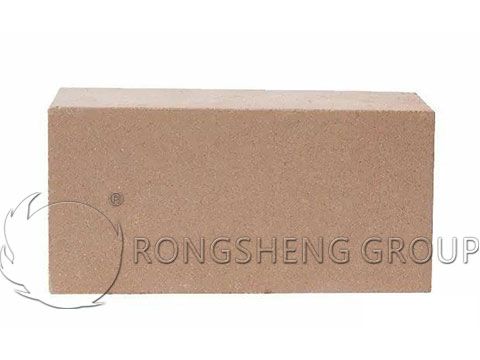
Precautions for Storage and Transportation of Lightweight Fireclay Bricks
When storing and transporting lightweight bricks for kilns, special attention should be paid to rain and moisture, otherwise, the strength of the bricks will be reduced and scrapped. Secondly, pay attention to handle with care. Because the compressive strength of lightweight fire clay bricks at room temperature is between 1-25MPa. So it is different from heavy refractory bricks, severe extrusion and collision will cause bricks to be scrapped.
Rongsheng Refractory Brick Manufacturer
Rongsheng is an experienced refractory brick manufacturer. Rongsheng’s refractory products include dense refractory bricks and lightweight insulation refractory bricks. Rongsheng refractory lining material manufacturer mainly provides customers with high-quality, cost-saving products. Rongsheng refractory manufacturer’s lightweight thermal insulation bricks currently include diatomite thermal insulation bricks, clay lightweight thermal insulation bricks, poly-light-weight thermal insulation bricks, mullite thermal insulation bricks, and alumina bubble bricks. Among them, the alumina hollow ball brick with the highest AL2O3 content is above 85, and the mullite thermal insulation brick is about 60. The price varies according to the density of the material.
To get the price for free, please contact us. We will provide you with the most suitable products and prices according to your specific needs.
Leave Your Requirements on RS Kiln Refractory Bricks And Castable Materials! We Will Reply You In 12 Hours!: