Air bricks play an important role in the steel refining process. By stirring the molten steel, it can quickly disperse and promote the melting of alloys, deoxidizers, desulfurizers, etc. added to the molten steel, and promote the removal of gas and non-metallic inclusions in the steel. It has the function of uniforming the temperature and composition of the molten steel, cleaning the molten steel, and improving the quality of the steel, thereby achieving the purpose of refining. As a refractory product, porous bricks will be consumed and damaged during use. If the usage method is not correctly mastered, it will affect normal production and even cause serious production accidents such as steel leakage. What are the general reasons for the steel leakage accident of the refining ladle purging plugs? RS Kiln Refractory manufacturer has conducted an analysis based on many years of experience in the production and sales of refractory materials and the specific situation after the use of ladle purging plugs.
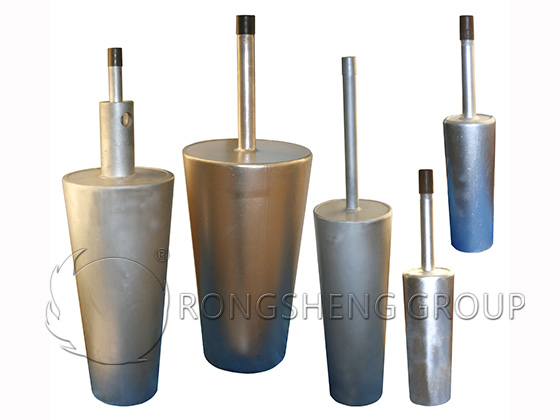
The Brick Core is Too Short
The air brick is at the bottom of the ladle and has to withstand the static pressure of molten steel during use. When the remaining length of the brick core is too short, the contact area between the brick core and the seat brick (well block) is reduced, the strength of the brick core will also be reduced, and cracks are prone to occur under the influence of rapid cooling and heating. If the pressure that the brick core can withstand is less than the static pressure of molten steel, the molten steel will press the brick core to fall off, or the molten steel will penetrate through the cracks in the brick body, resulting in steel leakage accidents.
Excessive use of purging plugs with too short remaining length, Reason: The porous bricks are gradually consumed during use, and the length becomes shorter and shorter. If the safety limit is exceeded, the purging plug will leak steel. The erosion rate of air bricks is generally within the range of 5 to 10 mm. It is mainly affected by production processes, steel types, and workers’ oxygen-burning habits.
Another way to express the life of the porous brick is the blowing time. The same purging plugs’ single-use time is extended, which will also reduce the number of times the air brick is used.
In specific use, most customers only care about the service life of the ladle, but ignore the total argon blowing time of the porous brick. In addition, the methods for judging the remaining length of the purging plugs are different, and many methods are not accurate enough. This can easily lead to excessive use of the air brick core and cause the remaining brick to be too short.
Solution: Design a safety display device. Generally, a safety display sign is installed at a height of about 150mm below the porous brick. The material has obvious differences in appearance and brightness from the purging plugs body material in the hot state, which is easy to judge. If you see the safety display during use, go offline immediately, which can effectively avoid steel leakage accidents caused by too short air bricks.
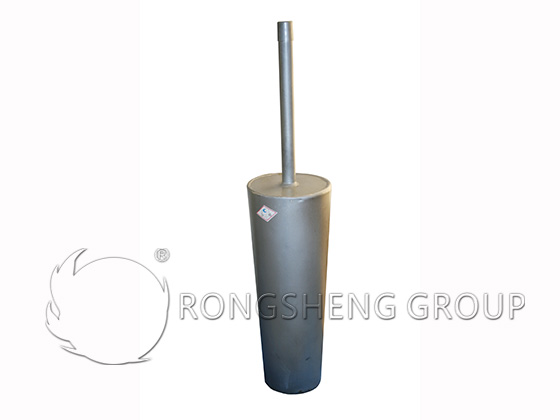
Oxygen Content Exceeds the Standard
Phenomenon: The purging plugs penetrate the steel from the center in a short time of use, and the slit in the brick core is honeycomb-shaped.
Photo of the broken purging plugs with excessive oxygen content in the blown gas, Reason: The purity of argon used in the molten steel refining process is required to be 99.99%, and oxygen mixing is not allowed. However, some steel mills use argon with lower purity during refining, and oxygen is mixed in. The mixed oxygen will cause secondary oxidation of molten steel and affect the refining effect. During the blowing process, oxygen reacts with molten steel, and its temperature is as high as 2000℃, which accelerates the melting loss of the air-permeable brick surface. Under the action of air flow scouring, the purging plugs will be quickly eroded, reducing the service life of the air-permeable brick, and in severe cases, causing the air-permeable brick to leak steel. Whether it is a slit, a ceramic rod or a diffused purging plugs, it cannot resist the melting loss caused by the reaction of oxygen and molten steel.
Solution: Strictly control the oxygen content of the back-blowing gas argon to ensure the purity of the back-blowing gas.
Steel Leaks from the Fire Mud Seam Outside the Steel Shell of the Air-Permeable Brick Core
Phenomenon: Molten steel leaks from the fire mud seam between the iron sheet of the air-permeable brick and the well brick.
Steel leaks between the iron sheet and the well brick. Reason: When the air-permeable brick is assembled on site, a layer of fire mud should be evenly applied to the outside of the brick core, and the thickness of the fire mud seam is generally required to be 2 to 3 mm. The operating procedures require that the brick core and the inner hole of the well brick be aligned horizontally, and the fire mud at the bottom of the brick core cannot be scraped off by other objects such as the seat brick during installation. If uneven application occurs or the fire mud falls off during installation, the fire mud of the brick core in the well brick will be thicker on one side and thinner on the other side. Since the fire mud powder has very low strength at high temperatures and is not resistant to erosion. The thick side of the fire mud seam is easily washed away by molten steel, which reduces the service life of the air-permeable brick. In the later stage of use, the molten steel penetrates through the fire mud seam as a channel, which is easy to cause steel leakage accidents. If the fire mud on one side is scraped off, since the iron sheet cannot be completely combined with the inner hole of the seat brick, a certain gap is left, and the high-temperature atmosphere will gradually oxidize and corrode the iron sheet, which is also prone to steel leakage.
Solution: Use breathable bricks with pad brick structure. Pad bricks play a supporting and protective role at the bottom of split bricks. Fire mud should be applied to the front and surrounding of pad bricks to seal the lower hole of the breathable brick core. If there is steel seepage in the brick core, the molten steel will flow to the pad brick position, the temperature will drop, and the molten steel will solidify here, preventing the accident from expanding. If the pad brick fire mud is not full, it cannot play a secondary protective role. Therefore, in the actual construction process, it is necessary to strictly abide by the operating specifications to ensure the construction quality.
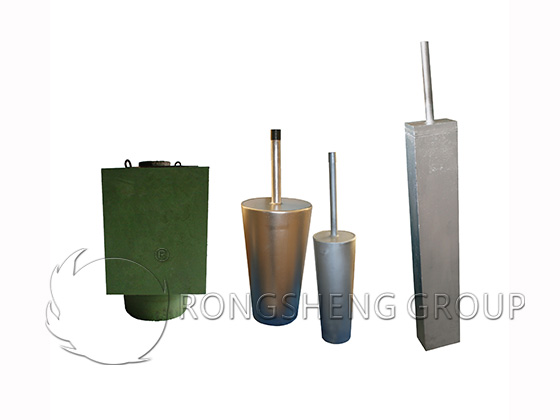
Steel Leaks from the Fire Mud Seam Inside the Steel Shell of the Purging Plugs Core
Phenomenon: During the refining process of the purging plugs, the molten steel penetrates downward along the fire mud seam between the steel shell and the porous brick core, and directly penetrates into the bottom air chamber, causing the bottom plate of the purging plugs to turn red. In some serious cases, the molten steel flows directly to the rear pipe of the air brick, and flows out from the rear pipe, causing a more serious steel leakage accident of the purging plugs. It is a layer of cold steel formed by the steel seeping through the fire mud seam inside the steel shell.
The reason why the molten steel seeps into the air chamber and forms cold steel inside the air chamber:
- 1) The lower part of the porous brick core and the bottom plate are not tightly pressed during installation. During use, the air brick core moves slightly downward, and a gap appears between the purging plugs core and the steel shell. This provides a channel for the penetration of molten steel, causing the molten steel to seep downward.
- 2) During the use of the air brick, the blowing pressure is too high, and the porous brick core moves slightly upward under the action of air pressure. The original tight installation will become loose. At this time, if the purging plugs falls back again under the action of external force when not blowing, a gap will be formed between the brick core and the steel shell. Steel seepage will also occur when it is used again.
- 3) When the porous brick is installed on the steel shell, the fire mud used does not sinter at low temperatures and has very low strength. During use, due to the disturbance of the blowing air flow, the local fire mud is slowly blown off from the bottom, forming a gap between the air brick core and the steel shell. The molten steel will seep down along the gap and enter the air chamber, forming steel seepage in the purging plugs fire mud seam.
Solution:
- 1) The amount of fire clay used to install the purging plugs should be appropriate. It has a certain strength at low temperature and is not affected by airflow, which will be safer and more reliable.
- 2) Change the appearance structure of the breathable brick. There are many breathable bricks with recessed rings on the market, which can effectively prevent the occurrence of steel seepage. The purging plugs uses a steel shell instead of a mold, and is directly cast inside the steel shell without using fire clay.
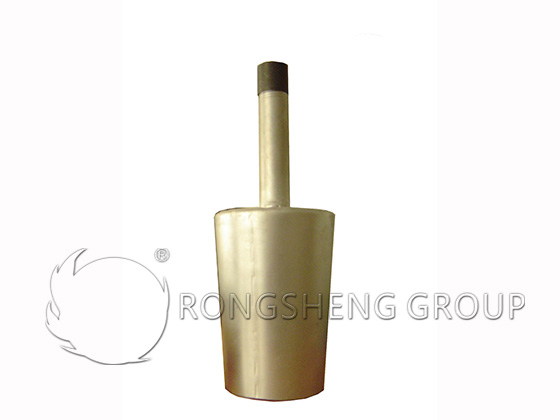
Steel Seepage in Narrow Slits
Phenomenon: During the use of narrow slit purging plugs, the slit size is too large, and molten steel seeps steel through the slits.
Reason: The slit design is unreasonable. The slit design of narrow slit breathable bricks is very critical. While ensuring the air permeability, it is also necessary to ensure that the molten steel does not infiltrate the slits in large quantities, causing the slits to be blocked and the purging plugs to be impermeable. At present, the slit width of breathable bricks is mostly between 0.15 and 0.2 mm. According to the wettability of molten steel and refractory materials, it is impossible for the slits not to infiltrate steel, and a small amount of steel seepage does not affect the blowing of breathable bricks. If one or part of the slits of the purging plugs are too large, the molten steel will seep into the slits, forming cold steel, blocking the slits, and causing these slits to be unable to be blown through. It is generally believed that the depth of steel seepage in the slits of breathable bricks is less than 15 mm, and the blow-through rate is higher when used again. The blow-through rate is low when the steel seepage reaches about 30 mm. The steel seepage cannot be blown through at all above 40 mm.
Solution: Design a reasonable number and width of slits. The purging plugs are designed with 20 to 36 slits and a width of 0.15 to 0.2 mm. The number of slits for large ladles is the upper line, and for small ladles is the lower line. Under a pressure of 0.3 to 0.6 MPa, the air permeability reaches 20 to 40 Nm3·h-1.
The function of the purging plugs well block is to protect the air brick core. If the seat brick cracks during use, it will not only fail to effectively protect the brick core and affect its service life, but also cause steel leakage in severe cases. In addition to the quality problems of the well block itself, external factors also have a crucial impact on the cracking of the purging plugs seat brick.
With the rapid development of steel smelting technology, the refining process outside the furnace has become an important part of the steel smelting process. The correct use of porous bricks can ensure production safety. When using purging plugs, various hidden dangers should be checked in time. According to different damage conditions, reasonable improvement measures should be selected to avoid the occurrence of air brick leakage accidents.
Leave Your Requirements on RS Kiln Refractory Bricks And Castable Materials! We Will Reply You In 12 Hours!: