Application of zirconium silicate. Zirconium silicate is a raw material in ceramic formula, and it is one of the indispensable chemical components in glaze. This raw material not only whitens the glaze, but also resists wear, corrosion, and hydrolysis. It is indispensable and can not be easily replaced. In order to improve the wear resistance of ceramic glaze, a ceramic factory increased the amount of zirconium silicate from 8% to 10%. Ordinary zirconium silicate products, such as standard zirconium silicate, low-grade zirconium silicate, and high-purity ultrafine zirconium silicate, all belong to this part. Their various properties can adapt to the process requirements of ceramics without any adjustment.
The generation of premium mainly depends on brand, scale, and cost management. For the selection of raw material zirconium silicate, from the perspective of reducing high-temperature viscosity, alumina raw materials should be avoided. That is to say, for zirconium silicate used in glaze, alumina balls should be avoided as much as possible for ball milling, and it is more advantageous to use zirconium silicate balls or zirconium oxide balls as grinding media. All studies have shown that the high-temperature viscosity of the opalescent glaze with the addition of zircon and zirconium oxide increases linearly with the increase of the amount of zircon and zirconium oxide added. Therefore, zirconium glaze is prone to defects such as pinholes, ripples, and rolling glaze. The reason is that zirconium compounds are highly refractory substances and are not easy to be melted in glass. It needs to be modified and coated to make it a fusible substance. In this way, it can become a perfect whitening agent.
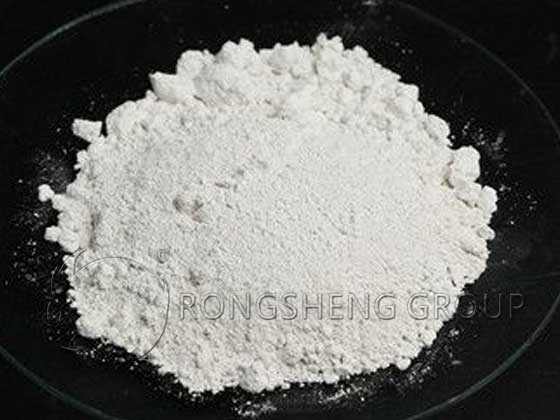
The practice has proved that in the process of grinding zirconium silicate, adding 0.1-0.5% lanthanum carbonate can effectively coat zirconium silicate. In addition, when zirconium silicate powder is added to the slurry, it is also very important to dissolve quickly and disperse effectively. 0.2% sodium acetate dihydrate can be added. Or directly adding 0.2-0.4% lanthanum acetate dihydrate can also achieve good results.
Nano zirconium silicate functional (powder) agent, zirconium silicate is the carrier of this technology, and the premium is a certain function that the product brings to the ceramic glaze. For example, self-cleaning, brightening, anti-static, sterilization, negative oxygen ions, etc. For example, a company customized and produced 450nm (350nm) zirconium silicate additives for Jiumu Company. The application technology of nano zirconium silicate in glaze is more complicated. As the fineness decreases, its specific surface area increases exponentially, and the nano effect is prominent. It is difficult to obtain a good slurry when making glaze. During the firing process, due to the high activity of the particles, it is easier to melt and link with the silicon in the glass, strengthen the network structure, and make the high-temperature viscosity of the glass greater. This makes dispersion and coating more urgent. It is even difficult to use nano zirconium silicate directly in ceramic glaze without modification.
Nano-Zirconium Silicate Coating Dispersion Modification
Nano-particles have a wide range of applications and potential markets. According to the forecast of the National Science Foundation (NSF), the potential market size of nano-powders will reach 340 billion US dollars from 2010 to 2015, and new applications of nano-powders are constantly being developed. For example: it is hoped that traditional industrial products can be nano-sized to enhance the value and performance of the products. Its application areas (such as coatings, inks, plastics, resins, functional color pastes, ceramic wind, etc.) are nano-sized in traditional industries. New products can also be developed using the characteristics of nano-materials, such as optical films, photocatalysts, health products, pharmaceuticals and other products. The application of nano-technology will lead to a new industrial revolution.
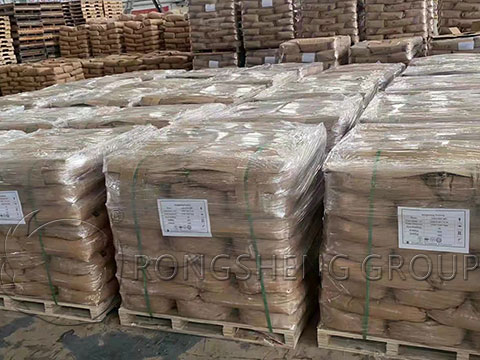
However, despite the huge potential market size of nanomaterials predicted by NSF, the United States, Japan, Germany and other countries have also invested a lot of manpower and material resources to develop the application of nanopowders. For example, Degussa of Germany has developed nano-grade SiO2. However, in 2003, the output value of nano-ceramic powder in the world was only 150 million US dollars, which is far from the predicted value.
Nano powders have not yet been successfully applied to the mass production stage. The main reason is that producers have not yet mastered the transformation conditions of all processes in the traditional industrial nano-process. These include the design of process formulas, the pre-treatment of nano powders, and the transformation conditions of nano powders. In particular, nano powders are prone to agglomeration due to the action of van der Waals forces. If traditional dispersion technology is relied on, nano powders cannot be dispersed. Therefore, if traditional industry is to be successfully nano-processed, the key technology must be mastered first, that is, how to properly transform nano powders. Make them still nanoparticles after adding them to the next interface, without the phenomenon of hard agglomeration. At present, most nano powders on the market have not been properly modified. Therefore, they cannot be directly and successfully applied to the development and manufacture of nano products. Up to now, at least 200 nano products have been developed in the market. However, most powders (inkjet, SiO2, AlO2, TiO2, ZrO2, ATO, ITO, etc.) have not been modified according to the needs, so they cannot be successfully applied. At the same time, many companies want to develop nano products, but cannot find modified powders suitable for their use. Therefore, how to properly modify nano powders and make them successfully applied to products will be a technology that nano technology personnel must master.
Modification of Nano Zirconium Silicate
Design of Chemical Interface Modifier. The general method of treating the surface of slurry has complex interaction forces, such as electrostatic repulsion, steric repulsion, and volume exclusion force to form a stable state of solid and liquid surface. The purpose is to avoid powder reagglomeration.
1) The first method is to adjust the pH value, so that the surface of the nano powder is charged, so that the powder and the powder have electric repulsion. However, due to the limitations of the application and formulation of the final product, the application of nano powder using this method is not much.
2) The second method is to use steric repulsion to form a stable state between solid and solid, solid and liquid. This method most often uses high molecular weight polymers or monomers as dispersants. When the particle size of the slurry is micron or submicron, this method works quite well. However, when the particle size of the slurry required to be dispersed or ground is less than 100 nanometers, when it is continued to be used as a disperser, most of the volume in the slurry has been occupied by obstacles formed by high molecular weight polymers or monomers. At this time, the slurry will easily produce the following problems. ① The solid content is greatly reduced, generally less than 35%. ② The viscosity of the slurry is increased, which is not conducive to the movement of the small grinding balls in the grinder, resulting in the inability to reduce the fineness of the particle size. ③ The powder is prone to re-agglomeration and nano-dispersion cannot be achieved.
3) In order to avoid the above problems, mechanical method is used to select low molecular weight functional agents. According to the concept of solution chemistry, functional agents formed by chemical bonds with smaller molecular weight are easier to connect to the surface of nanopowders, and the selected interface modifier is a low molecular weight organic acid functional machine. In principle, the interface modifier should have two functional machines at the same time: one functional machine is designed to connect to the surface of nanopowders, so that a stable phase is produced on the surface of nanopowders to avoid reagglomeration of powders; the other functional machine is designed to be connected to the interface performance added later to avoid incompatibility. Therefore, the tool used for interface modification customization is wet dispersion nano-grinding equipment. Therefore, the selected interface modifier must be compatible with the solvent used. Although the molecular weight of the selected interface modifier is very small, it can still produce a film with a thickness of 2-5nm on the surface of nanoparticles, which is sufficient to support the stability of nanoparticles. The interface modifier tailored according to the above principle can meet the following requirements: ① The solid content can be increased to 35-45%. ② The particle size can be reduced to the size of the primary particle size (about 10nm). ③ The viscosity of the slurry is no longer affected by the reduction of particle size and increases rapidly. ④ The separation is not easy to produce hard agglomeration again.
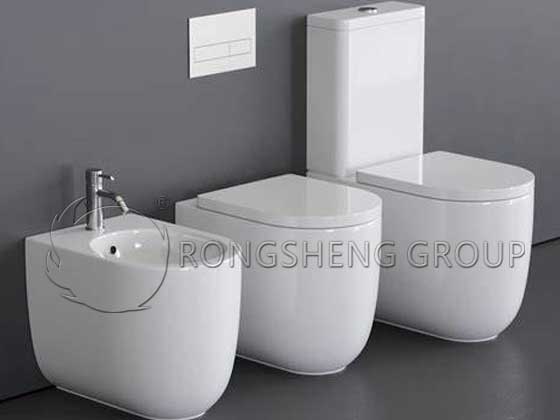
Research on the Application of Nano Zirconium Silicate in Sanitary Ceramics
Mao Zedong said that reading is learning, and using is also learning, and it is more important learning. Similarly, we say that the research and development of nano zirconium silicate is also a complex system engineering. The use of nano materials such as nano zirconium silicate is also a revolutionary innovation project in the ceramic industry. This is because nano zirconium silicate can not only reduce the amount of use by more than 30% when used on the glaze, but also make it whiter, warmer, smoother, more wear-resistant, and have lower radiation after use on the ceramic glaze. More importantly, nano zirconium silicate, like other nano powders, has quantum size effect, small size effect, surface effect and macro quantum tunnel effect, thus showing many unique properties, and has broad application prospects in catalysis, light filtering, light absorption, medicine, magnetic media and new materials.
Indeed, the ceramic industry has achieved some positive research results in the research and application of nano materials and nano technology, especially in nano glaze (or functional glaze). Main achievements: nano lead-free antibacterial glaze, nano self-cleaning (easy to clean) glaze, nano negative ion glaze, recognized by the industry, and thus the manufacturers with huge benefits are rarely reported. This is of course because ceramics need to be fired at high temperatures, which prevents the function of nanomaterials from being effectively exerted. In order to find an effective way to solve this problem, let’s show this process.
R&D Process of Nano Zirconium Silicate
Since the nano zirconium silicate product was launched, it has been deeply loved by well-known sanitary ware manufacturers at home and abroad due to its advanced product indicators, stable quality and moderate price. The product has become in short supply. On this basis, a joint R&D team of experts in multiple fields, including sanitary ceramics experts, nano material experts, composite materials experts, and glaze spraying equipment experts, has been formed. The team’s goal is to open up the intermediate link from nano powder to nano ceramic glaze (nanoceramics) and find an effective way to give full play to the superior performance of nano powder materials under the existing ceramic process conditions. Recently, the R&D team has mainly done three aspects of work. ①, Nanostructured ceramic glaze. Through the structural design of the 0.8-1mm glaze of sanitary ceramics. Under the premise of reducing the amount of nano zirconium silicate by 70%, the glaze quality of ceramic products is made whiter, brighter, smoother, more wear-resistant, and has lower radiation. The small test of this work has been completed and is in the pilot test. It is expected that the product will be put on the market in the second half of next year. ②, Nano self-cleaning antibacterial functional glaze. Design a ceramic glaze with nano zirconium silicate as a carrier, strong bactericidal ability, and long-lasting and effective performance. In order to achieve the requirements of continuous high efficiency, we proposed a design model of ceramic element, which is a micro ceramic element smaller than 43 microns (325 mesh). There are functional particles inside, and the outer layer is a shell composed of nano zirconium silicate, with channels on the shell that allow functional particles to enter and exit. The element needs to remain functional at normal firing temperature, and countless ceramic elements form functional powder. ③. Nano health functional glaze. Using the design concept of ceramic element, a functional powder with nano zirconium silicate as the carrier is designed and applied to the glaze slurry of bathroom ceramics. The fired ceramic glaze has the function of releasing negative ions and activating water (turning large molecule water into small molecule water), making the bathroom a place beneficial to human health.
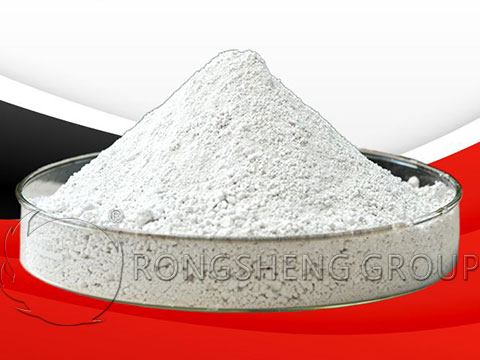
At the same time, manufacturers will also study other related topics. But the main task is to make good nano powders and provide customers with high-quality and low-cost raw materials. The research on the middle section – material application methods that we undertake is just a starting point. Therefore, more application issues should be solved by experts from all links of the industrial chain. Together, we will find ways to give full play to the excellent properties of nano zirconium silicate, so that nano zirconium silicate powders and nano ceramic products can benefit mankind more.
It has been eight years since the birth of nano zirconium silicate. We have indeed made many improvements for this project, including the characterization, formulas, and mechanisms of various grinding modes, and have made new assumptions and verifications one by one. We have done what our predecessors have not done, and have perfectly polished a large-scale nano powder production line. Maybe this is just a small step in the application of nano in ceramics, but it is the most important step. Because this is the beginning of physical processing of nano powders, it represents the beginning of low-cost processing of mixed nano powders, and low cost and the use of mixtures are the essential needs of ceramic materials.
Since the birth of nanotechnology in the 1990s, people have begun to predict that the future of ceramics lies in nanotechnology. Recently, exciting news came from the ceramic industry that 300 nanometer ceramic inks were used on a large scale in inkjet printing and glaze spraying, causing a revolution in the field of ceramic glazes, and the momentum is very strong. The future of ceramics lies in nanotechnology and nanomaterials. Sanitary ware will need more nanomaterials like nano zirconium silicate powders in the future. The future of nano zirconium silicate lies in the strong cooperation of ceramic manufacturers, scientific research institutions and zirconium silicate ultrafine powder manufacturers.
Leave Your Requirements on RS Kiln Refractory Bricks And Castable Materials! We Will Reply You In 12 Hours!: