The rotary kiln is the core equipment of cement plant production and operation. Whether continuous production can be guaranteed depends largely on the use of the refractory lining of the rotary kiln. However, there are many factors that affect the service life of the rotary kiln refractory, but the main factors are chemical erosion, heat load, and mechanical load.
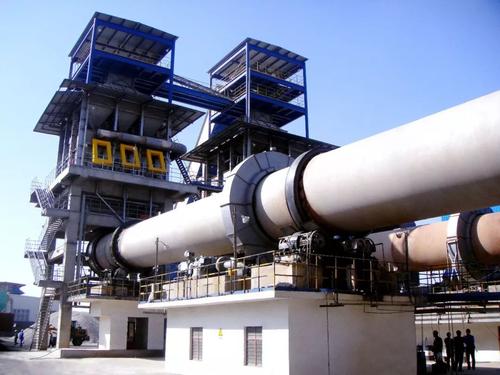
Functions of Refractory Lining for Rotary Kiln
- 1) Prevent high-temperature materials, flames, and airflow from directly damaging the cylinder, protect the kiln cylinder, and avoid high-temperature deformation of the kiln cylinder.
- 2) Prevent liquid phase clinker and harmful substances such as CO, Cl2, and SO2 from directly eroding the cylinder during the firing process.
- 3) During the calcination process, the firing temperature of the clinker is about 1450℃, but the temperature of the combustion gas in the kiln can reach more than 1700℃. The refractory material in the kiln plays a heat insulation role, reduces the temperature of the cylinder, prevents heat loss, and saves energy.
- 4) It has the function of heat storage and heat preservation. The refractory kiln lining can act as a heat transfer medium. It absorbs heat from the high-temperature gas in the kiln and transfers the heat to the material by conduction and radiation.
- 5) The refractory kiln lining can improve the performance of the kiln skin, prevent high temperatures and harmful substances from eroding the cylinder, and better protect the kiln cylinder.
Factors Affecting the Service Life of Rotary Kiln Refractory Materials
The rotary kiln can be divided into the front kiln mouth, lower transition zone, firing zone, upper transition zone, pre-decomposition zone, and rear kiln mouth. According to the temperature of different parts, refractory linings of different materials need to be configured. During the production process, the refractory materials will be subjected to mechanical loads from the kiln body and the forward movement of materials, thermal loads from the combustion of coal powder in the coal injection pipe and high-temperature materials, chemical erosion of clinker and harmful gases, etc. Factors such as the design, quality, masonry, drying of refractory materials in the kiln, and wear from materials will also cause premature damage to the refractory lining.
After theoretical analysis and combined with actual production experience, the factors affecting the service life of refractory bricks in the kiln are obtained. There are three main factors: chemical erosion, thermal load, and mechanical load.
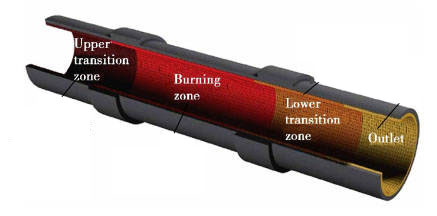
The impact of mechanical load on the service life of refractory materials
The mechanical load of the rotary kiln is mainly the relative movement and heat transfer of the cylinder, refractory materials, materials, and dusty gas during the calcination of cement clinker. The kiln lining is subjected to mechanical loads generated by relative movement as well as gravity and abrasion from the materials. When the mechanical load borne by the refractory materials in the kiln exceeds its own strength, it will cause damage to the refractory materials. The factors that generate mechanical loads are mainly the following three reasons:
- The cylinder is twisted and deformed. The cumulative weight of the refractory materials, materials in the kiln and the cylinder itself is too large. Under the action of gravity and heat load, or due to local high temperature, the cylinder will be partially deformed. The circular cross-section of the cylinder will become elliptical. When the kiln is running, the deformed part of the cylinder will generate mechanical load on the refractory material, and the greater the ellipticity, the greater the mechanical load generated. The shear stress generated by the change in ellipticity acts on each ring of bricks, causing the bricks to peel off. In general, the peeling thickness is uniform and hard.
- The axis of the rotary kiln is offset. The rotary kiln is supported by tires, supporting wheels and rollers. The lines connecting the center points of each cross-section circle should be on a straight line. However, after the kiln shell is installed and part of the shell is cut and replaced, or after the kiln body has been running for a period of time and the thermal system in the kiln is unstable. Under the action of heat load and load, the axis of the kiln body will be offset. After a long period of operation, the wear of the tires and rollers, the outward and inward deviation of the rollers, and the loads at each support point will change differently. In particular, when the load at the support point is too large, the surface of the tires and rollers will peel off or crack abnormally, which will further aggravate the axis deviation of the kiln body. The axis deviation will result in the refractory material being squeezed and deformed, causing damage or falling off. The shape of the damaged refractory bricks varies in depth.
- Poor masonry quality. Due to construction factors, the refractory bricks are too loose and twisted. During the operation of the rotary kiln, the kiln body and the cold surface of the refractory bricks move relative to each other. Excessive thrust on the brick lining will cause the refractory bricks to twist, tilt, and dislocate, crack the brick layers, drop corners, and even drop bricks.
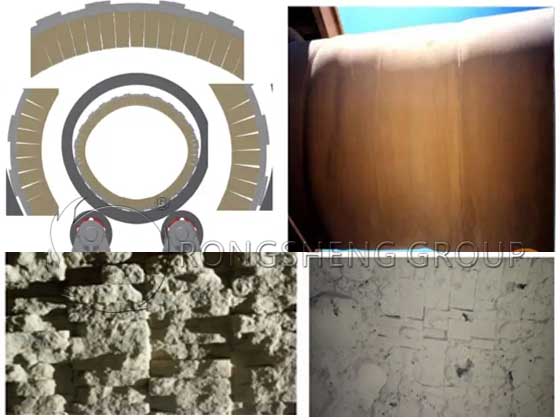
The influence of heat load on the service life of refractory materials
Thermal load refers to the thermal expansion of refractory materials caused by high temperature during the temperature rise of the kiln lining, which causes the adjacent refractory materials to squeeze each other. When the extrusion stress generated by the inability to expand completely freely is greater than the strength of the refractory bricks, it will cause the hot surface of the refractory bricks to peel off. Thermal stress is one of the important reasons for the peeling and breakage of refractory bricks in the kiln. Taking magnesia iron bricks or magnesia aluminum spinel bricks as an example, the expansion rate at 1400℃ is calculated as 1.6%, and the expansion amount of refractory bricks with a length of 198mm can reach 3.16mm. For such a large expansion, the annular joint (expansion joint) needs to be correctly reserved. Too much reservation may cause the refractory bricks to draw and fall off. The thermal stress generated by too small reservation has nowhere to be released, which will cause the refractory bricks to peel off. This seriously shortens the service life of the refractory bricks.
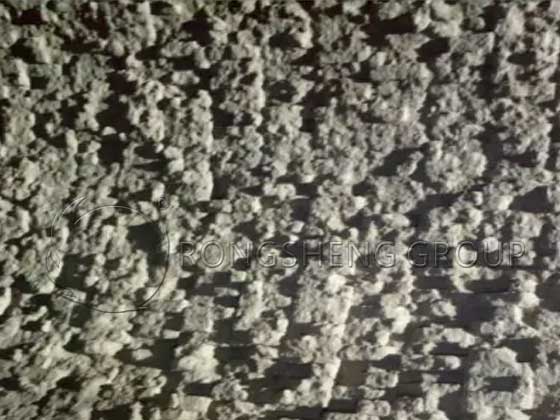
Effect of chemical erosion on the service life of refractory materials
Chemical erosion on refractory materials exists in any kiln and is one of the important factors affecting the service life of the kiln. And the erosion mechanism is more complex.
- The calcination temperature is too high or fluctuates. In the rotary kiln, the material is gradually converted into cement clinker, and the liquid phase of the clinker in the burning zone is about 25%~30%. The converted clinker phase mainly includes C3S, C2S, C3A and C4AF. At high temperatures, the liquid phase clinker will react chemically with the surface of the refractory bricks, and the refractory materials will also be penetrated and corroded by harmful substances such as alkali salts and some harmful gases. If the calcination temperature is too high, the amount of clinker liquid phase will increase. The chemical reaction between clinker and refractory materials will intensify, resulting in a deepening of the reaction layer between clinker and the hot end of refractory materials. Due to the difference between the reaction layer and the internal structure of the brick, a qualitative change occurs. If the temperature in the kiln suddenly fluctuates greatly or the kiln is stopped for cooling, the metamorphic layer of the refractory material will cause peeling and cracking. Therefore, in order to ensure the service life of refractory bricks, production operations should be stabilized and a reasonable system of heating and cooling kilns should be formulated.
- Faster kiln speed. The speed of the new dry rotary kiln is usually 3.5-4r/min, and sometimes even higher than 4r/min, and the linear speed of the drum can reach more than 1m/s. If the kiln speed is increased, the clinker will come into contact with the refractory material more frequently under high speed, large diameter, and high-temperature conditions. This makes the combined damage effect of heat load, mechanical load, and chemical erosion on the kiln refractory lining much greater than that of a low-speed rotary kiln or a static kiln. This requires that the refractory kiln lining of large and medium-sized rotary kilns must have sufficient strength and stability, and a reasonable rotary kiln system must be established.
Nowadays, under the policy background of green development planning, the lining of rotary kiln refractory materials is developing towards “energy saving, environmental protection, long life, lightweight, and chromium-free”. If the configuration scheme, design, quality, storage, masonry, kiln drying, production operation and other factors of the lining of cement rotary kiln are not handled properly, they can affect the service life of rotary kiln refractory materials. Through the analysis of the above factors, a series of measures should be formulated to maintain the refractory materials. Only in this way can the service life of the refractory materials be extended and the best use effect can be achieved.
Leave Your Requirements on RS Kiln Refractory Bricks And Castable Materials! We Will Reply You In 12 Hours!: