Refractory linings for lime kilns are used in harsh environments, and the linings are affected by wear, mechanical stress, and chemical erosion. Therefore, the refractory materials used for the lining of the lime rotary kiln must be resistant to wear, corrosion, and thermal shock.
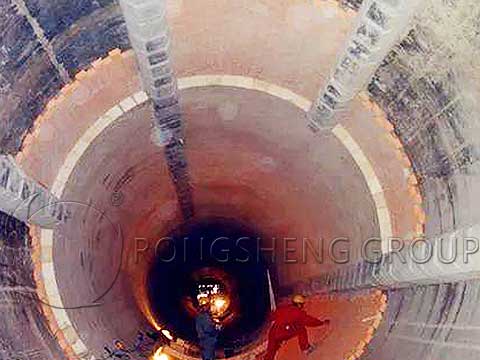
Lime rotary kiln is a dynamic kiln, and there are many requirements for refractory materials for the lining. For example, it is resistant to high temperatures and can be chemically stable at high temperatures for a long time. Re-burning is small, with high mechanical strength, compact structure, and low porosity. More wear resistance and very strong corrosion resistance. Especially in the low wall part, the use of wear-resistant bricks has a longer service life than the castable. Because the use of wear-resistant bricks is small, many manufacturers still use steel fiber wear-resistant castables.
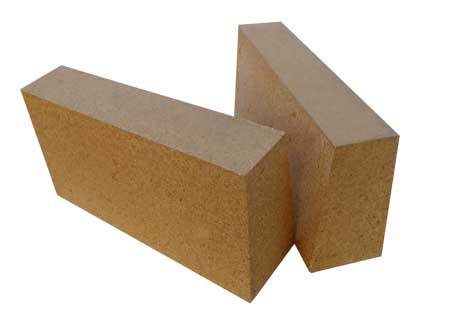
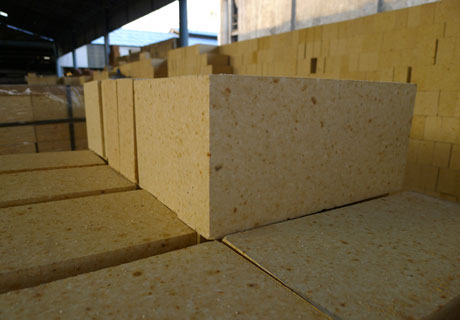
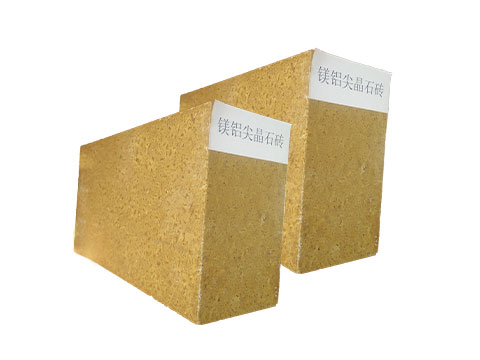
Refractories for Various Parts of Lime Rotary Kiln
In front of the lime rotary kiln preheating zone is a preheater. The limestone is heated in a preheater with a particle size of 10-30mm, and the temperature of the preheating section is 1000°C. Refractories in this area should be high strength, wear-resistance, and thermal shock resistance. Either clay bricks with better compactness or alkali-resistant castables can be used.
The transition zone temperature is about 1100°C, which is the transition stage before limestone enters the firing zone. During this period, the temperature fluctuates greatly, and part of the limestone will react. Choose high alumina bricks or phosphate bricks. In order to make the raw materials evenly heated and distributed, several protrusions can be added in the length direction to drive the raw materials to flip. This material generally uses prefabricated blocks of the same material, that is, mullite castable prefabricated blocks.
The temperature in the high-temperature zone is around 1200℃, and the temperature fluctuates greatly. Refractory materials must have a high load, high-temperature volume stability, and thermal shock resistance. High-load soft bricks are used for direct masonry without permanent layers.
The calcining zone is the final reaction stage of lime, and the working temperature is 1300°C. The firing temperature is affected by the activity of the raw material limestone. The higher the required activity, the higher the firing temperature. Choose etherate composite bricks or high-load soft bricks, and choose magnesia-alumina spinel bricks for masonry with large kiln diameters. Add steel plate between refractory bricks. The steel plate and refractory materials react to form mafic spinel at high temperatures, which makes the masonry more durable.
The cooling system of the cooling zone is the cooling part of the finished lime, which is cooled by a fan. The temperature of the cooling belt is lower than 100℃, and the cooled lime enters the silo through the conveyor belt. The temperature of the hot air after heat exchange is about 600°C, and it enters the rotary kiln to mix and burn with the combustors. The cooling zone is generally built with high alumina bricks. The temperature of several layers of bricks/casting materials in a small area at the front end of the cooling zone is 1200°C. Either high alumina bricks or phosphate bricks can be used.
High-strength steel fiber castable or corundum mullite castable should be used for the kiln mouth and coal injection pipe.
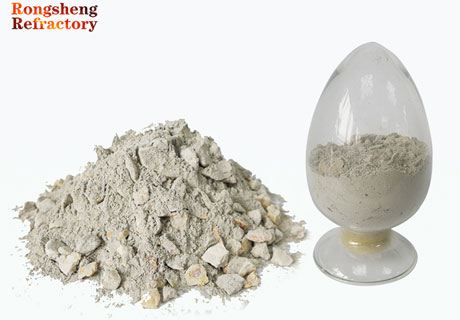
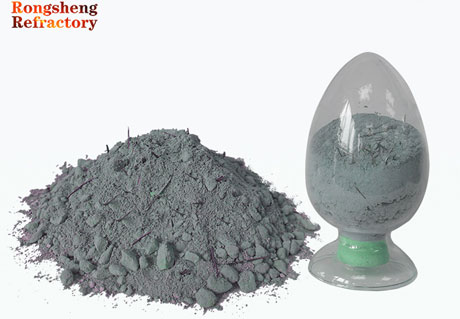
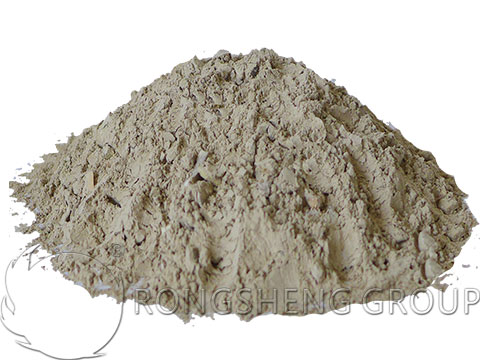
Refractory Castables for Lime Kiln
Lime rotary kiln preheater and front and rear kiln mouth usually use refractory castable, but the quality of preheater and kiln mouth is different. Although the use temperature of the lime shaft kiln inlet and the lining of the preheating zone are not high, they are quickly damaged by the mechanical and airflow of the material. The wear-resistant castable is made of steel fiber. Steel fiber castables are used for the preheater. The steel fiber castables are mainly selected for their high wear resistance. Can resist the erosion of special parts of the kiln mouth.
Refractories used in lime kilns have short application life and large repairs. Choosing appropriate refractory materials to improve the masonry technology and strive for the life of the kiln lining is a common concern of the manufacturers and the castable manufacturers. According to the difference of each part of the lime kiln, different refractory castables are used. Steel fiber reinforced castable for kiln headcover. The simple wear of the low wall of the grate cooler uses mullite high-strength wear-resistant castable, and some manufacturers use wear-resistant bricks. Steel fiber high-strength wear-resistant refractory castables or corundum mullite castables should be selected for coal injection pipes.
However, when building refractory materials, the construction requirements must be strictly followed in order to make all kinds of refractory castables fully achieve the use effect. If it is a vertical kiln, the necking of the split furnace should be made of anti-skinning and refractory castables, and the lower arc of the cooling zone should be fully cast with heat-resistant concrete to prevent the brick joints from running out of the wind. This masonry will improve the stability and wear resistance of the shaft kiln.
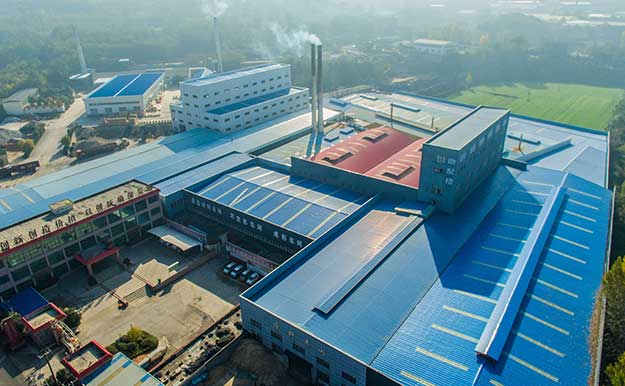
Rongsheng Kiln Refractory Materials Manufacturer
Rongsheng is an experienced manufacturer and seller of furnace refractories. Rongsheng’s refractories have been used in furnace equipment in more than 60 countries around the world. For example, Vietnam, Thailand, Malaysia, Singapore, Indonesia, Philippines, Turkey, Kuwait, South Africa, Egypt, Russia, Uzbekistan, etc. In the application of rotary kilns and steel mills, the customer return rate is very high. In addition, Rongsheng has many refractory projects for glass kilns. If you need to buy refractory materials for kilns, please contact us. We will provide you with services according to your specific needs. Get the factory price of the most primitive refractory materials.
Leave Your Requirements on RS Kiln Refractory Bricks And Castable Materials! We Will Reply You In 12 Hours!: