After the cement rotary kiln lining is welded with anchors, laid with calcium silicate board, and supported by the mold, the correct way to construct the refractory castable for cement kiln should be carried out in the following manner. Such as the construction of the monolithic refractories in the cement kiln refractory lining.
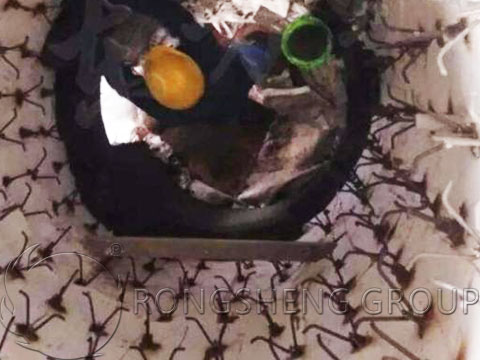
1) Check.
Check the packaging and delivery date of the refractory castable. The general shelf life is 6 months, to avoid moisture regain, conduct a pre-test to check whether it is invalid. Check the shape and cleanliness of the equipment to be poured. Check the integrity of the construction equipment, vibrating tools and other spare parts must be intact. Check the type, size, layout and welding quality of anchors. Metal anchors must be properly compensated for expansion with bituminous paint and plastic caps. Check the surrounding refractory brick lining and the measures to which are taken to prevent the water loss of insulating castable in the insulation layer. Check the water, the water quality must meet the quality of drinking water. Check whether the pouring equipment has loose parts (such as kiln mouth iron protection), if it is loose, it must be fastened with iron plates and then welded.
Where the inspection of the above items is unqualified, construction shall be carried out only after being qualified. Expired materials shall not be used. In the construction of refractory castables, it is necessary to ensure that there is no power outage, water stop and construction interruption. Especially the pouring of monolithic refractory castable on the top of kiln headcover. Once the construction is stopped, the interlayer will appear in the casting layer, the hot gas entering the layer joint will burn out the anchor, and the castable will collapse.
2) The amount of water added to the castable material should be strictly controlled according to the instructions.
The limit shall not be exceeded. On the premise of ensuring the flow performance of the construction, the amount of water added should be small, not large. Note: Use clean water to avoid other components or debris in the water from affecting the solidification.
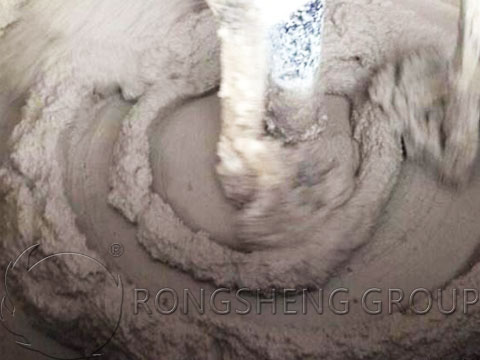
3) The mixing time of the refractory castable should be no less than 5min, and manual mixing is strictly prohibited.
When mixing, dry mix in advance. After the dry mix is uniform, add 80% of the total water demand to stir. Then, depending on its dryness and wetness, slowly add the remaining water and continue to stir until a suitable working consistency is obtained. When mixing casting materials with different qualities, the mixer should be cleaned first.
4) Refractory castables must be used in barrels and bags.
Stirred castables are generally used up within 30 minutes. In a high-temperature and dry working environment, this time should be shortened appropriately. Casting materials that have been initially set or even agglomerated may not be poured into the mold frame, and it is strictly prohibited to add water and stir for a second use.
5) The refractory castable poured into the mold should be immediately layered and vibrated with a vibrating rod.
The height of each layer should be <300mm, and the vibration spacing should be about 250mm. Try to avoid touching the anchor when vibrating, and do not vibrate and re-vibrate in the same position for a long time. After seeing the slurry on the surface of the castable lining, the vibrating rod should be slowly pulled out to avoid segregation and voids in the castable layer. After the casting is completed, the casting body can no longer be compressed or vibrated before solidification.
6) When pouring in a large area, construction shall be carried out in blocks.
The area of each pouring area should be 1.5~2.0 m. Expansion joints should be left at every 2.0m with plywood, and must not be left out. Expansion joints should be left at intervals between anchors.
7) After the surface of the castable is dry, cover the exposed part with plastic film immediately.
After the initial setting, it should be regularly sprinkled and maintained to keep its surface moist. The curing time should be at least 2 days, and the first day should be watered frequently. Generally, after 6~8h, the castable is finally set. After the final set, the side mold can be removed to continue sprinkling and curing. However, the load-bearing formwork must wait for the strength to reach 70%, and the mold can be removed after 48h.
8) After the formwork is removed, the casting body should be inspected in time.
Quality problems such as honeycomb, spalling, and voids should be dealt with and repaired in time. When the problem is serious, the defective part should be chiseled to expose the anchor, and then filled with the same quality castable to continue the maintenance, and it is forbidden to replace it with cement mortar.
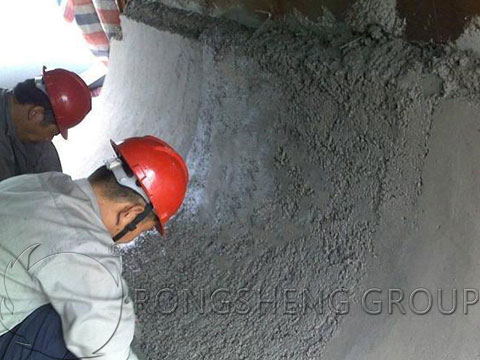
In order to pursue the construction speed, some construction teams arbitrarily increase the amount of water added to the refractory castable. The mixed castable can be transported into the mold with a rubber hose of several meters or even dozens of meters like flowing water. If the strength of the mold is poor, it is easy to cause deformation of the lining or increase the amount of water added to the castable, which will affect the construction quality. The mold is not supported and the castable is applied manually. This situation is generally used during the construction of the blanking pipelining, and sometimes even appears in the construction of the partial preheater cone lining. Expansion joints, gate valves and other equipment should be prefabricated on the ground before installation. These prefabricated parts have strict requirements for mold making due to their complicated geometric dimensions. The mold is made of metal steel plate, and it cannot be deformed during construction. Therefore, the mold support should be firm and the mold support position should be correct.
Learn more at the RS Refractory Materials Manufacturer.
Leave Your Requirements on RS Kiln Refractory Bricks And Castable Materials! We Will Reply You In 12 Hours!: