After the monolithic refractories are mixed with water or liquid binder, the mixed material gradually loses thixotropy or plasticity and is in a solidified state, which is called the Coagulability of Monolithic Refractories. The time required to go through this process is called the setting time. The initial setting time is the time when the mixture begins to change from a “viscous-plastic” body or a “viscous-plastic-elastic” body to a “plastic-elastic” body. The time from a “plastic-elastic” body to an elastomer is the final setting time.
Monolithic Refractory Materials Setting Time
Monolithic Refractory Materials containing coarse aggregates are still in a unified setting time determination standard. However, the setting time of the matrix part can be determined using the Chinese national standard “Cement Slurry Setting Time Determination Method GB 146”. When measuring, the aggregate particles larger than 100μm can be screened out, and the powder (containing binder) can be added with water or a mixture composed of a liquid binder and a coagulant can be used for determination. That is, put the slurry (mixed material) adjusted to a standard consistency into the trial mold of the Vicat meter (setting time tester). According to the operating procedures specified in the standard, it is repeatedly measured that the measuring pointer on the Vicat meter from adding water and mixing into the slurry until the distance from the bottom of the mold is 0.5~1.0mm, the required time is the initial setting time. When the test pointer sinks into the slurry and the distance from the upper surface is not more than 1.0mm, the required time is the final setting time.
For refractory castables, also called monolithic castable refractory, in order to meet the requirements of the construction operation time, it is generally required that the initial setting time should not be earlier than 40 min, and the final setting time should not be later than 8 h. But for sprayed refractories, the shorter the setting time, the better. Such as the wet spray material, is required to flash and solidify immediately after spraying on the spray surface to prevent the spray coating from falling off or collapsing.
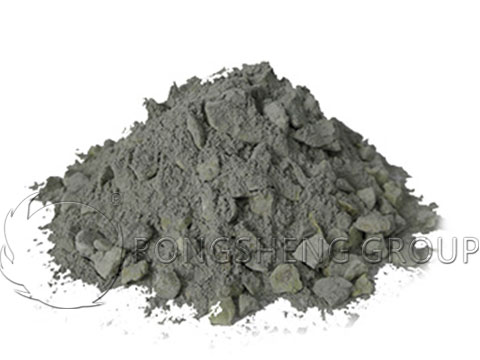
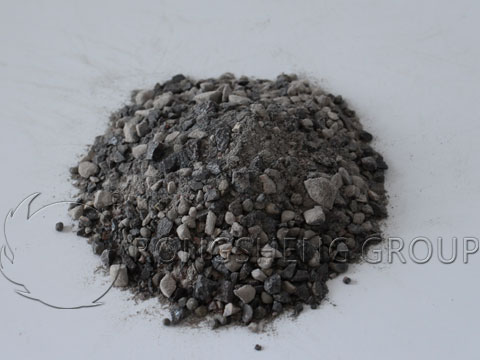
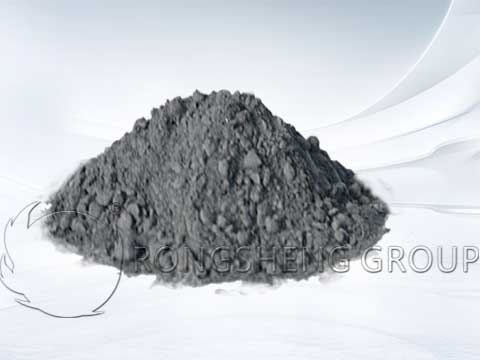
Monolithic Refractory Application
Now, due to the continuous updating of materials and varieties, the quality of monolithic refractory materials has been greatly improved, and the preparation technology and construction technology, and equipment have made significant progress. This makes the application range of monolithic refractories continue to expand. The application field has been developed from low-temperature and medium-temperature thermal equipment to high-temperature smelting furnaces. From the lining body that can only build the atmosphere furnace to the kiln lining body that can be built in contact with the high-temperature melt.
In the metallurgical industry, from iron ore sintering, coking, ironmaking, steelmaking, refining outside the furnace, continuous casting to steel rolling, etc. The lining of thermal equipment and smelting furnaces in almost every production link must be constructed or repaired more or less with monolithic refractory materials. For example, in the steelmaking system, the converter should use alkaline refractory gunning material, hot feeding material, and slag splashing to protect the furnace material. The ladle lining is made of aluminum-magnesium castable and repairing material, and the external refining device RH, DH, dip tube, argon blowing, and powder spraying spray gun, CAS-OB immersion cover, the top cover of various ladle furnaces, etc., are all used High-grade refractory castable is used as the lining body. The permanent lining and working lining of the continuous casting tundish are also constructed with aluminum-silicon castables and magnesia (or magnesia-calcium) coatings or dry vibrating materials.
In other industries, including non-ferrous metallurgy, petrochemical, building materials, machinery industry, electric boilers, garbage incinerators, and other industrial kilns, there are examples of using monolithic refractory materials to construct linings. And its comprehensive use effect is better than using refractory brick products.
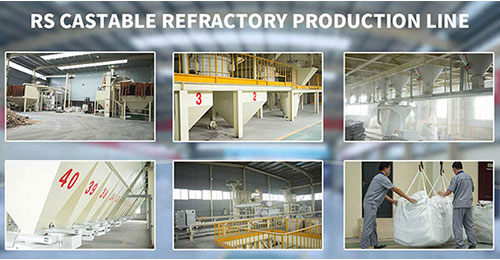
Monolithic Castable Refractory Manufacturer
A powerful manufacturer of monolithic refractories, with an environmentally friendly, advanced, and fully automatic monolithic refractory production line. Rongsheng’s monolithic refractory production line has an annual output of 80,000 tons. Whether in various monolithic castable refractory or in the production of refractory plastics and refractory ramming materials, the refractory formula can be customized according to the customer’s actual thermal furnace equipment refractory lining requirements. To purchase high-quality monolithic refractory products, please contact Rongsheng monolithic refractory castable manufacturers.
Leave Your Requirements on RS Kiln Refractory Bricks And Castable Materials! We Will Reply You In 12 Hours!: