High-temperature furnace refractory bricks are indispensable refractory materials for building high-temperature furnaces. High-temperature furnace refractory bricks are subjected to severe tests such as high temperature, thermal shock, and corrosion. Their correct laying can not only improve the stability and durability of the furnace but also ensure the smooth progress of the production process.
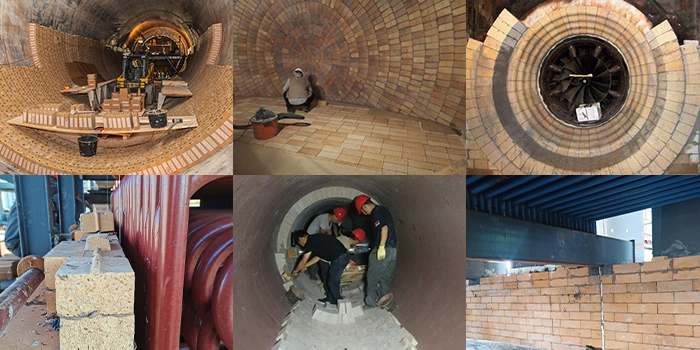
High-Temperature Furnace Refractory Bricks
Before laying high-temperature furnace refractory bricks, the interior of the furnace should be reasonably planned and designed. By understanding the shape, size, and use requirements of the furnace, determine the appropriate brick type, size, and laying method. During the laying process, the interior of the furnace should be cleaned. Ensure that the surface of the base is flat and clean, and remove oil and debris. Then, according to the design drawings, determine the laying position and arrangement of the bricks, and use refractory mortar or high-temperature glue to firmly bond the bricks to the base. During the laying process of bricks, ensure that the gaps between bricks are uniform and use special tools and measuring instruments to ensure the horizontality and verticality of the bricks. At the same time, control the thickness and density of the bricks to ensure that the bricks are tightly combined without gaps, so as to improve the high-temperature resistance of the furnace.
During the laying process of high-temperature furnace refractory bricks, after the furnace refractory bricks are laid, the brick surface needs to be maintained and dried. To ensure that the bonding between bricks is stronger. Regular inspection and maintenance of the laid high-temperature furnace refractory bricks is also very important. Timely repair and replace bricks that need to be replaced due to aging or damage to extend the service life of the furnace. The above is the process of laying high-temperature furnace refractory bricks. In the actual construction process, it is completed in strict accordance with the design requirements and construction specifications. Only reasonably designed and carefully laid high-temperature furnace refractory bricks can ensure the safe operation of the furnace and provide solid and reliable support for industrial production.
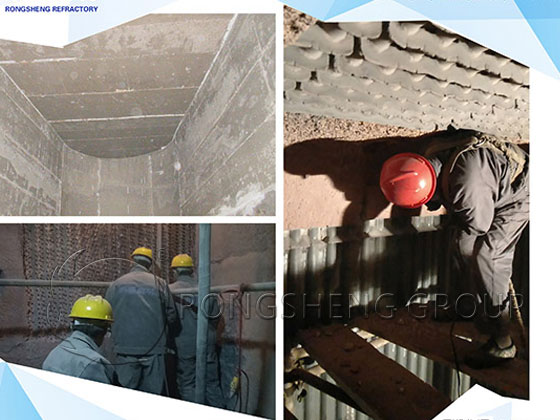
Application of Unshaped Refractory Materials in the Metallurgical Industry
Unshaped refractory materials, also known as bulk refractory materials, are composed of bulk particles and fine powders and do not need to be fired or formed before use.
A blast furnace is an important piece of equipment for ironmaking. Small blast furnaces used to be hoisted and built with prefabricated blocks of high-alumina cement and high-alumina phosphate refractory sintering materials. Now, resin-bonded aluminum-carbon unfired bricks are commonly used for masonry.
The water-cooled walls of large blast furnaces are rammed with silicon carbide castables. The bottom cushion and surrounding brick joints are made of refractory castables and silicon nitride fillers. One of the development trends of refractory materials for furnace walls is to use of castables. my country mainly uses corundum-silicon carbide castables. Most of the blast furnaces in Japan use ASC castables and repair gunning materials for the iron ditch. The iron ditch of some small blast furnaces uses alumina or synthetic mullite-silicon carbide-silicon ramming materials. The iron ditch of blast furnaces in Germany and France generally uses ASC ramming materials. France has developed self-flowing castables to increase the service life of the working lining of the main iron ditch.
The reverberatory furnace is a major consumer of refractory materials in aluminum smelting. The refractory materials for the furnace have changed from brickwork to an integral structure. The refractory materials in contact with the hot metal surface of the furnace are usually acid-bonded plastics, phosphate-bonded bricks, and low-cement castables. The composition of the hot surface refractory materials of the lower side wall is usually the same as that of the furnace. The insulation material can be lightweight insulation castables, insulation clay bricks, or ceramic fibers. The furnace roof material is usually high-quality refractory materials such as ramming materials and burning injection materials. The furnace door is usually cast with dense castables lightweight castables, or a mixture of the two.
RS Kiln Refractory is a manufacturer with strong capabilities in the production and sale of refractory lining materials. Our environmentally friendly fully automatic monolithic refractory production line provides a guarantee for the production of monolithic refractory lining materials for high-temperature industrial furnaces. In addition, our newly built refractory brick factory is about to be put into production, and the product quality is guaranteed. Contact us to get free solutions and quotes for refractory materials for the metallurgical industry.
Leave Your Requirements on RS Kiln Refractory Bricks And Castable Materials! We Will Reply You In 12 Hours!: